Introduction
The manufacturing method of Injection molding produces many plastic goods that everyone uses every day, including those made more efficiently by a heated manifold . Manufacturing technology experts have created the hot runner system which now powers better quality and faster production techniques in plastic production. Due to its advanced nature the system directs molten plastic from the injection unit into specific mold openings while supervising thermal conditions all through production.
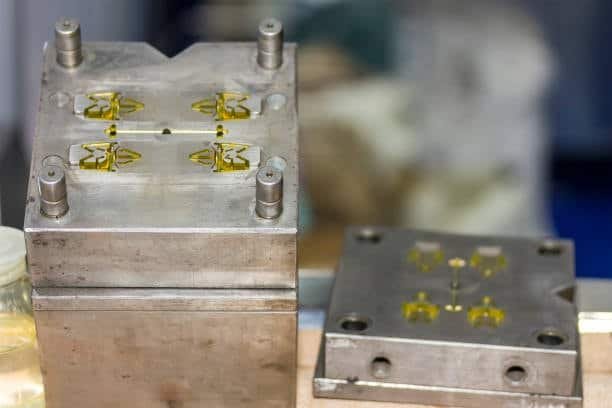
Hot runner technology now replaces old recycling systems for sprues and runners in plastic manufacturing to save space and time and reduce total operating costs, showcasing hot runner advantages . Suppliers need to understand hot runner molds because clients worldwide want manufacturers to make their products in ways that save money while maintaining top quality and supporting environmental goals.
We will examine all critical elements of injection mold hot runner systems with their advantages and applications for both injection molding experts and beginners.
Understanding Injection Mold Hot Runner Systems
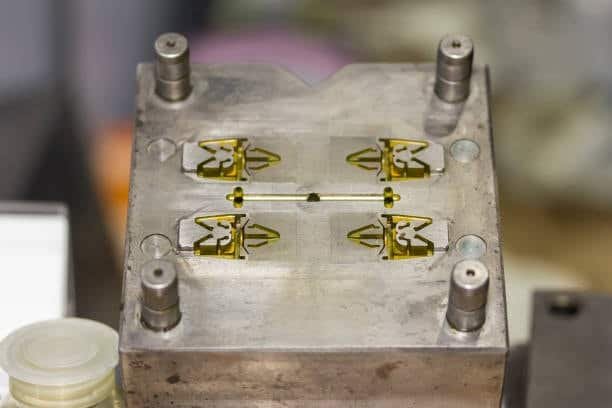
Definition and Basic Principles
The hot runner system combines multiple heated components in an injection mold that keeps plastic material in liquid form throughout its travel from injection to mold cavities. The heated channels of hot runners maintain plastic fluidity while cold runner systems cool down and require material replacement.
The basic benefit of hot runner systems depends on precise control of the exact temperatures throughout the mold process. Controlled heating systems operate across the whole system to maintain temperature stability from the temperature controller at machine nozzle to the part entrance.
Key Components of Hot Runner Systems
Hot runner systems bring together the following basic features in their design, including the molding machine nozzle :
- Manifold: The primary distribution block gets plastic melted from the machine then guides the molten material to several flow paths. Each internal path through a manifold holds heated plastic that needs precise temperature control.
- Hot Runner Nozzles: The Hot Runner Nozzles combine the heat source with the mold opening to hold output material temperatures steady before release into the cavity. The heating section inside each nozzle controls its temperature to regulate melt flow.
- Heating Elements: Electric heating elements put in targeted spots monitor temperatures through all system zones.
- Temperature Controllers: Electronic temperature systems monitor multiple. zone temperatures in the hot runner system while providing diagnostic and process data.
- Gates: The mold cavity section accepts plastic material through open entry points created in specific patterns to meet diverse manufacturing conditions.
- Valve Gates (in valve gate systems): Valve Gate Systems include mechanical pins that adjust each gate position to customize the flow of plastic into the mold
Historical Development of Hot Runner Technology
Hot runner technology began as a simple device in 1940 but professional manufacturers have refined it over many decades. The older versions of these systems proved basic in design with weak temperature calibration and often needed repair. Development in electronic technology helped take hot runner systems to better performance levels.
The 1970s brought better and more accurate ways to heat materials. During the 1990s computer control systems and state-of-the-art materials made hot runner systems more dependable and efficient at making intricate plastic parts with excellent output results.
Modern systems work better because of enhanced modeling tools plus superior manufacturing standards along with state-of-the-art control mechanisms that help them run with optimum results while using less power and needing less upkeep.
Types of Hot Runner Systems
Externally Heated vs. Internally Heated Systems
Externally Heated Systems: The system features heating elements installed on the outside parts of the manifold and nozzles. They need basic care and produce lower production costs. These systems cannot provide temperature accuracy as well as their international counterparts yet use more energy than heating systems within the manifolds, leading to costly secondary operations .
Internally Heated Systems: Manufacturers put heating components straight into flow channel pathways for this design concept, making it suitable for high volume production . They heat the injection material directly and efficiently resulting in quicker response times plus better temperature regulation skills. Their higher costs justify their better performance results in demanding use situations.
Thermal Gate Systems vs. Valve Gate Systems
Thermal Gate Systems: Stating temperature controls the entry point for plastic injection in thermal gate systems. Part of the plastic at the gate line turns solid when the process stops before melting back during the injection phase. These systems use basic designs and few moving elements to reduce production costs and need minimal upkeep. The technology provides less direct control of when the gate should be activated or disabled.
Valve Gate Systems: Some production lines open and close valve gates mechanically with physical pins. Pedestals of these gates deliver power from pneumatic, hydraulic, or electric motors. Valve gate systems deliver superior control for injection molding by creating better gate quality and multicavity balance plus sequential filling functions. Valve gate technology becomes essential when building exact parts that need high-quality gates and need to show their development stage.
Open Nozzle vs. Valve Gate Nozzle Designs
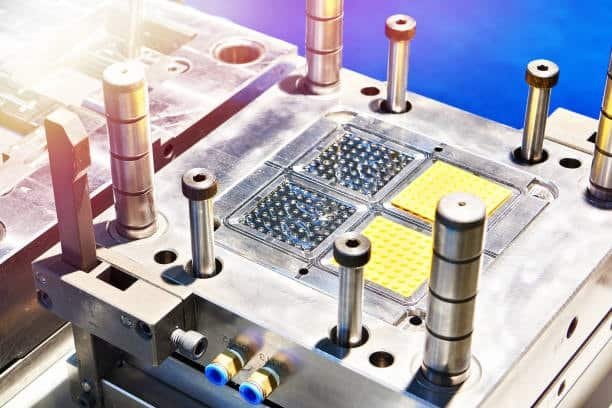
Open Nozzle Systems: In open nozzle systems the passage from the manifold to the cavity remains unblocked during standard operation. During manufacturing stops the gate system shuts off automatic heating which freezes the material at the gate point. Open nozzles save money but create more visible imperfections and harder control of the manufacturing process.
Valve Gate Nozzle Systems: A valve gate nozzle operates by means of movable mechanical pins to switch the flow channel on and off. By adding control features this technology brings multiple main benefits to users.
- Reduced or eliminated gate vestige
- We stop dripping from the nozzle between molding cycles
- Total management over when gates begin and stop functioning
- Capability for sequential filling of complex parts
Single vs. Multi-Cavity Hot Runner Systems
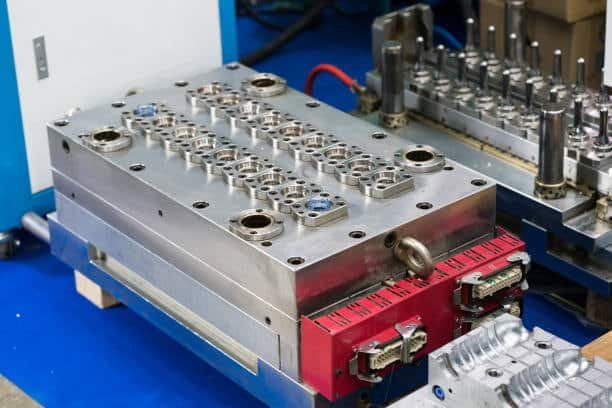
Single Cavity Systems: Single Cavity Systems deliver material flow into one mold chamber mainly to produce large component types or custom products. They have basic setups and demand low support yet make poorly small items at high numbers.
Multi-Cavity Systems: TMany Cavity Systems draw contents from a single manifold unit to produce products faster. Multi-cavity hot runner systems work correctly when they direct each cavity to receive mold material at the right time. This practice makes every part produced by this system the same quality.
Benefits of Hot Runner Systems in Injection Molding
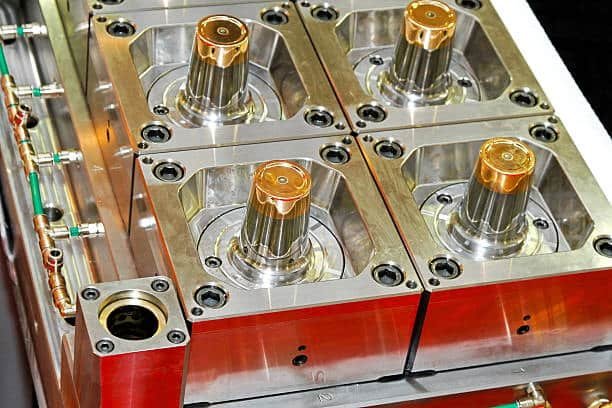
Production Efficiency Improvements
Use of hot runner systems enhances production by giving companies these main benefits, which help to reduce waste significantly :
- Reduced Cycle Times: After removing the runner system from cooling and ejection the production time reduces between 20% and 40%.
- Automated Operation: Hot runner systems let you run molding operations automatically and need less human help for making parts continuously.
- Faster Color Changes: Specialized hot runner components let manufacturers change colors more quickly so they spend less time preparing for new runs.
- Higher Productivity: The number of finished products increases because faster cycles work together with reduced downtime.
Material Cost Savings
A hot runner system helps manufacturers save material through its main benefits.
- Elimination of Runners and Sprues:Hot runner systems make better use of material since everything injected finds its way into the final product without needing it for the runner system.
- Reduced Material Consumption: The use of hot runner systems helps customers reduce their material requirements by up to 40% while saving high-cost engineering resins.
- Less Regrind: Plastic parts receive better properties because we produce less recycled runners when hot runners replace traditional tools.
- Reduced Purging Material: Special hot runner systems need less purging material during color or material changes since they work better than older systems.
Quality Improvements
The hot runner system creates better part quality by
- Balanced Filling: Appropriate hot runner design makes sure all cavities receive equal filling at the same instant to create similar parts across the batch.
- Reduced Warpage: A well-controlled filling and packing process decreases internal stress levels and part warpage.
- Improved Surface Finish: Parts show enhanced surface quality because the cold runners do not interrupt the flow process.
- Enhanced Dimensional Stability: The stable production process helps create parts that maintain their designed shape better than before.
Environmental Benefits
Hot runner systems serve in environmental preservation by helping manufacturers:
- Reduced Material Waste: Because the parts receive less plastic material from hot runner systems manufacturers can lower their scrap waste levels.
- Lower Energy Consumption: Heated shoot systems consume less power per part because they run in less time than regular processes even with their heating needs.
- Smaller Machine Requirements: Higher Production Speeds Reduce the Machine Size That Manufacturers Need Making the Investment and Power Use More Efficient.
- Extended Mold Life: Orthogonal or side-to-side removal of runners makes hot runner molds work longer and suffer less physical damage compared to ordinary runner molds.
Design Considerations for Hot Runner Systems
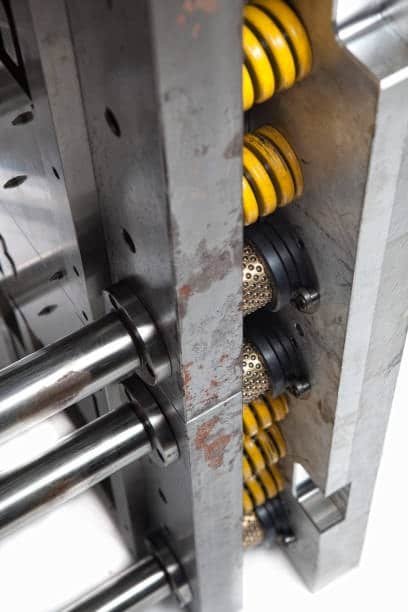
Material Compatibility
The type of plastic affects its flow habits and tolerances during the production stage so our hot runner solution needs special design details for many materials.
- Temperature Sensitivity: Heat-sensitive plastics like PVC and POM acetal need specific temperature settings because they break down fast when fettered..
- Shear Sensitivity: PVC plastic types and certain filled compounds can degrade if shear forces appear through improperly laid flow channels.
- Thermal Properties: The thermal elements of processed material such as conductivity specific heat and melting temperature affect hot runner design choices.
- Corrosiveness: Standard hot runner components cannot work with corrosive materials so producers need special manufacturing materials.
Gate Location and Design
The gate’s design directly affects product quality appearance and production productivity.
- Gate Placement: The gate placement must distribute material evenly across the mold while limiting flow problems and cosmetic defects in viewable areas.
- Gate Size: Gate size has to work well with injection flow while matching automatic degating power and gate remnants.
- Gate Style: Gate builders have multiple choices between edge gates, submarine gates, direct gates and valve gates for each production purpose.
- Vestige Control: When designing cosmetic parts the gate vestige must be kept at minimum levels which requires specialist valve or thermal gate manufacturing technology.
Thermal Management
Hot runner design depends on excellent temperature control more than any other factor, particularly in addressing cold runner limitations .
- Zone Control: Several separate temperature control systems help maintain perfect heat levels everywhere in the equipment.
- Thermal Isolation: Mold parts stay separated from thermal sources with space barriers and insulating materials to lower power usage and stop solidification too early.
- Heater Selection: Cartridge heaters, coil heaters, and band heaters each offer different performance characteristics suitable for different applications.
- Temperature Monitoring: Employee positions thermocouples in key spots to track and regulate temperature correctly across essential system components.
Balancing Multi-Cavity Systems
Good part quality depends on getting every cavity of a multi-unit mold to work equally well.
- Geometric Balance: Uniform distribution of molding material across all runner channels creates perfect filling results naturally.
- Artificial Balancing: If natural mold balance cannot be achieved valve timing adjustments and flow restrictions create filling equilibrium.
- Pressure Drop Calculations: Our simulation tools let us foresee how pressure changes during filling and mold construction.
- Sequential Valve Gating: Our system controls valve opening order to fill parts step by step which eases pressure needs while producing better results.
Implementation and Operation Best Practices
Installation and Setup
The correct setup of hot runners determines their successful performance.
- Alignment: Proper part positioning during build-up keeps wear even and blocks material leakage from happening.
- Torque Specifications: You need to follow bolt torque guidance from the manufacturer to maintain good part appearance and sealing.
- Electrical Connections: Quality electrical links attached with proper labels need to be secured to avoid problems with temperature control.
- Startup Procedures: The startup procedure ordered by the manufacturer protects components from thermal stress during their first use.
Temperature Control Strategies
Advanced temperature systems help our systems reach maximum efficiency levels easily.
- Startup Sequencing: A correct heating series in startup allows us to protect the materials from damage and maintain component functionality.
- Temperature Profiling: An automated temperature system uses multiple heating sections to find the best material flow.
- PID Control: Advanced controllers apply PID controls to reach intended temperatures while reducing temperature swings.
- Standby Temperatures: Periodic temperature reduction at production stops conserves energy without affecting system availability.
Maintenance Requirements
Performing regular upkeep enhances system stability and extends its total operation time.
- Preventive Maintenance Schedule: Following component documentation helps avoid maintenance interruptions by keeping the system functional.
- Cleaning Procedures: Our regular cleanings remove broken materials and impurities from our flow paths.
- Heater Testing: Routine <-Testing of resistance checks lets us spot Heater defects before they fail.
- Valve Pin Maintenance: Maintaining valve pins and actuators on valve gate systems helps keep the system working as intended.
Troubleshooting Common Issues
Identifying and resolving regular problems helps us run production without interruptions
- Temperature Control Problems: Tainted temperature control happens because thermocouples break down combined with heater faults and controller breakdowns.
- Material Leakage: Thermal expansion when components fail or get installed incorrectly creates leaks along their points of contact.
- Gate Freeze-off: The cooling system failures or temperature mistakes lead to early material solidification at the gate.
- Color Contamination: The stagnant material zones that experience material breakdown continue to produce color stains during the next melt cycle.
Applications and Industry Trends
Industry-Specific Applications
The hot runner system shows its value in many different sector applications, particularly in minimizing plastic waste .
- Automotive: The automobile sector uses many-cavity molds for interior trim parts alongside special valve controls for bumper production plus highly accurate systems to make cosmetic auto parts.
- Medical: Technical solutions designed for medical device production handle cleanroom standards while working with hard-to-use medical polymer materials.
- Packaging: These systems produce more than 144 cavities to make closed parts at very fast cycle speeds.
- Consumer Electronics: Specialized systems for optical components, multi-material applications, and miniature precision parts.
Innovations in Hot Runner Technology
Modern technology develops hot runner applications further each year, enabling faster processing in manufacturing .
- Miniaturization: Engineers make smaller micro-scale hot runner systems for medical and electronic part production.
- Multi-Material Systems: Advanced hot runner technology lets users put multiple materials into the same mold during specified or simultaneous injection operations.
- Electric Valve Gate Actuation: Electric valve gates control valve pins through programmed movement patterns.
- Smart Systems: Smart Technologies: Sensors detect performance data while monitoring equipment tracks issues before breakdown occurs.
Hot Runner Systems for Specialized Materials
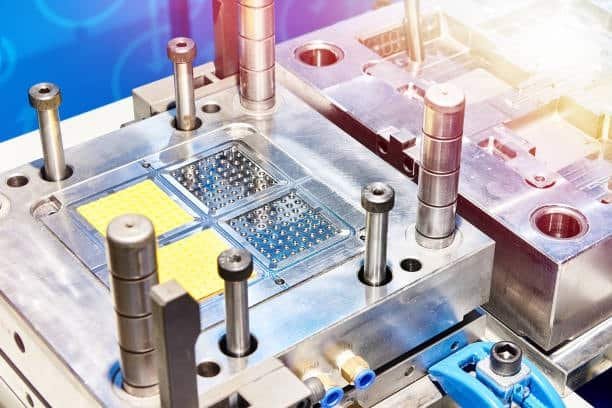
Specialized hot runner technology supports different material types
- High-Temperature Materials: Special systems work with PEEK and PEI engineering plastics plus other high-temperature materials at temperatures above 350°C.
- Bioresins: Our modified hot runner systems help process biodegradable and bio-based plastic materials without problems.
- Highly Filled Compounds: The wear resistance parts of the system and improved cavity shapes help prevent damaged components during fiber-reinforced plastic processing.
- Liquid Silicone Rubber (LSR): Custom valve gate systems enable cold runner use during LSR processing.
Integration with Industry 4.0
Manufacturing networks now link to and control hot runner systems.
- Data Collection and Analysis: Modern hot runner controllers measure production outputs to find superior processing settings.
- Predictive Maintenance: Monitoring system activity helps us see coming component problems sooner than their usual failure.
- Remote Monitoring and Control: Through internet accessibility our systems let technicians fix problems while making system parameter changes remotely.
- Process Optimization: Machine learning systems review processing data to identify the best parameter changes for high performance results.
Economic Analysis of Hot Runner Implementation
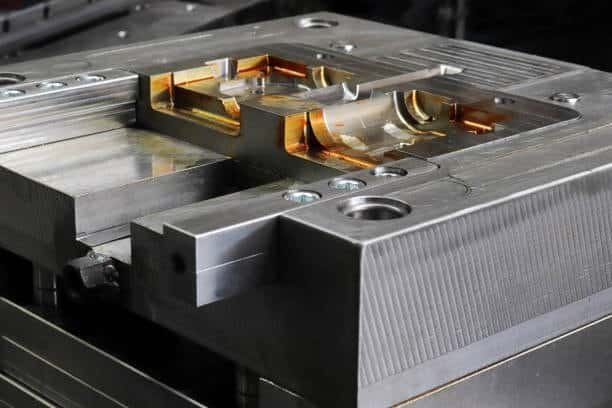
Initial Investment Considerations
You need to pay substantial startup funds for hot runner systems.
- System Cost: A basic hot runner system increases mold expenses by $20,000 to over $200,000 due to its technical specifications molten plastic enters.
- Additional Infrastructure: Establishing the technology requires new temperature controllers and training staff while maintaining the setup demands additional support personnel mold masters.
- Design Complexity: Complex part designs made possible by hot runners need more engineering assistance to achieve success injection points manifold systems.
- Production Interruption: Household production needs special attention when changing to hot runner technology multiple cavities.
Return on Investment Calculations
Although hot runner systems have greater upfront expenses they provide excellent return on investment.
- Material Savings: Manufacturers normally save 20% to 40% of the material since hot runner systems remove the need for runners and sprues mold plate.
- Cycle Time Reductions: A production line working faster through shorter production cycles can make up to 30% more products in each application.
- Labor Savings: Hot runners help companies reduce their workforce for handling runners and grinding mold portions along with minimizing manual tasks.
- Quality Improvements: Product enhancement reduces scrap items and simplified post-mold procedures which add to direct money savings injection molding system.
Total Cost of Ownership Analysis
When you look at overall TCO during product life it includes all expense categories.
- Energy Consumption: Hot runner systems need powered heating but they use less energy for each part because they operate better than regular systems.
- Maintenance Expenses: Hot runner systems need precise maintenance but their enhanced productivity covers most of these maintenance costs.
- System Longevity: A hot runner system that receives proper care can perform reliably across multiple million production cycles.
- Flexibility: Making swift color and material changes brings more flexibility to our production line at lower changeover expense injection molding machine.
Conclusion
The latest hot runner technology improves both plastic production efficiency while creating superior quality with eco-friendly benefits, helping to reduce waste . The initial cost increase brings benefits like lower material usage and faster production processes that bring back investment money through better part quality and adaptable manufacturing.
Manufacturing requirements for enhanced accuracy plus better performance and eco-friendly products drive hot runner technology toward new developments. These high-end control systems along with optimized designs for demanding materials are helping these advanced systems do more for Industry 4.0.
Manufacturers who want better market success through increased production performance should adopt hot runner technology. Whenever manufacturers utilize hot runner systems correctly, they enhance overall quality and earn financial returns plus they help protect the environment.