خدمة القولبة بالحقن
شركة ZCmold هي واحدة من أفضل موردي خدمات القولبة بالحقن. مع أكثر من عشر سنوات من الخبرة في مجال التصنيع، نحن خبراء في خفض نفقات التشكيل وصناعة القوالب طوال عملية التصنيع. تتفوق ZCmold باستمرار على منافسيها بفضل كفاءتنا في تصميم القوالب، والتصنيع الدقيق، والآلات المتطورة، وأوقات التسليم السريعة.
إذا لزم الأمر، يمكننا توقيع اتفاقية عدم إفشاء قبل تقديم عرض الأسعار.
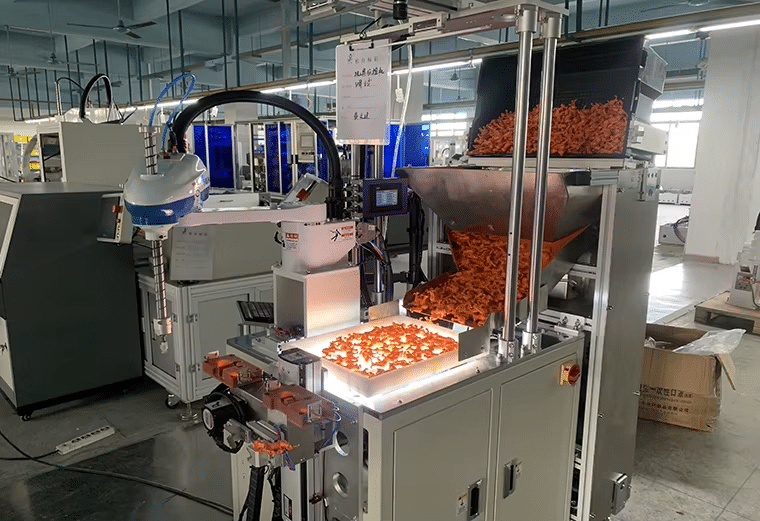
ما هو القولبة بالحقن?
باستخدام القولبة بالحقن، يمكنك صنع قطع غيار مخصصة بأعداد كبيرة عن طريق إدخال المواد المنصهرة، بما في ذلك المواد البلاستيكية ذات الدرجة الهندسية أو اللدائن ذات الدرجة الهندسية أو الرقائق البلاستيكية المدمجة أو مواد مركبة مختلفة، في قوالب دقيقة.
هل بدأت للتو في التعرف على القولبة بالحقن؟ لقراءة المزيد عن القولبة بالحقن، اضغط على "ما هو القولبة بالحقن؟"
أنواع تقنيات القولبة بالحقن التي نقدمها
على الرغم من أن القولبة بالحقن تنطبق عادةً على البلاستيك، إلا أنها تتضمن عدة طرق أخرى، بما في ذلك قولبة حقن البلاستيك والمعادن. كما ترى أدناه، تقدم ZCmould خمس خدمات مختلفة لقولبة الحقن.
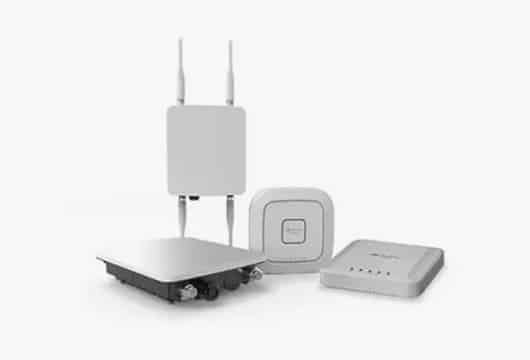
قولبة حقن البلاستيك
ولصناعة الكثير من السلع الاستهلاكية المعمرة وقطع غيار السيارات والحاويات، فإن التقنية الأكثر استخدامًا هي البوليمرات مثل النايلون أو الكمبيوتر الشخصي أو ABS.
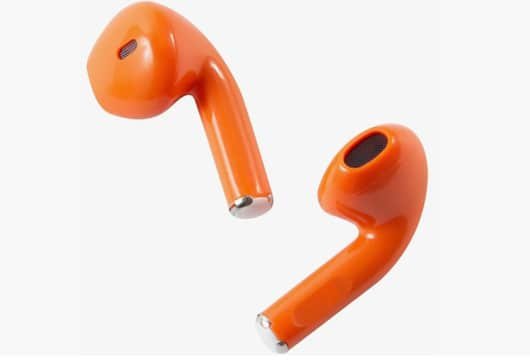
صب القوالب بالحقن ثنائي اللون
قادرة على صنع مكونات للصناعات والمعدات المقاومة للتآكل والعديد من ألوان السلع الاستهلاكية من خلال توحيد مادتين.
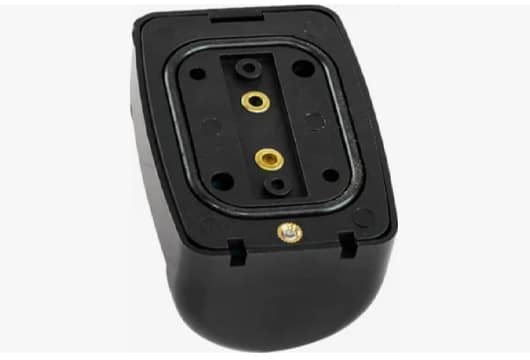
إدراج القوالب
يدمج السيراميك أو الأجزاء المعدنية في البلاستيك والتي تعتبر قياسية في أغطية الحساسات والبراغي والتركيبات المستخدمة في الكهرباء.
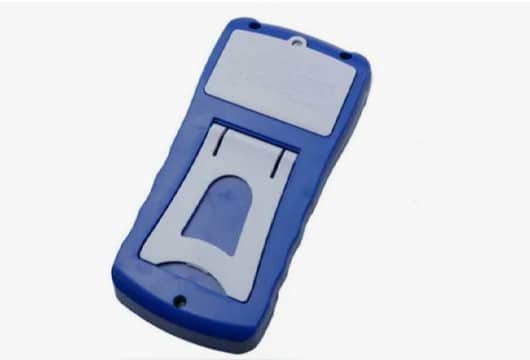
التشكيل الزائد
وغالبًا ما يستخدم في الأختام المثبطة للاهتزازات والأزرار الطبية ومقابض الأدوات لأنه يغطي قاعدة صلبة بمادة TPE الناعمة أو ما شابهها.
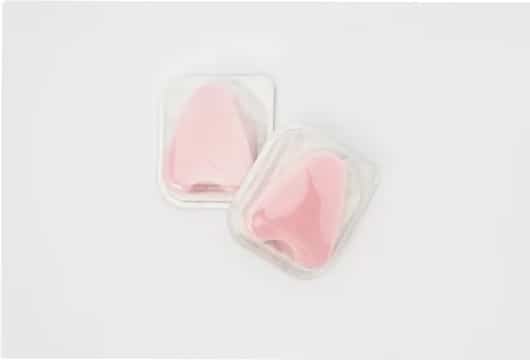
قولبة حقن السيليكون بالحقن
استخدامات LSR لإنتاج موانع تسرب قابلة للتكيف للسيارات وحلمات زجاجات الأطفال والمنتجات المخصصة للاستخدام في درجات الحرارة العالية في الصناعة الطبية.
الكمال الحرفي بنقرة واحدة
سير عمل القولبة بالحقن بالحقن المخصص
قد يكون التشكيل بالحقن المخصص أمرًا معقدًا، ولكن مع منصة ZCmould عبر الإنترنت، ما عليك سوى تحميل رسوماتك ثلاثية الأبعاد للبدء.
الخطوة الأولى
تقديم المشروع ومراجعة عروض الأسعار
بعد أن ترسل إلينا مستندات التصميم الخاصة بك، سنقوم بتقييم احتياجاتك في يوم واحد ونقدم لك مساراً مقترحاً لمشروعك.
الخطوة الثانية
تحليل التصميم من أجل التصنيع (DFM)
من خلال مراجعة وتحسين تصميم القِطع واختيار المواد وتصميم القوالب باستخدام طريقة سوق دبي المالي، يمكننا إنتاج كل من النماذج والأجزاء الكبيرة الحجم بأكثر الطرق فعالية من حيث التكلفة.
الخطوة الثالثة
الموافقة على التصميم وتأكيد الطلب
تحقق من تصميم قالب الحقن وتأكد من أن التفاوتات والتشطيبات السطحية تفي بمتطلبات الجزء قبل طلب الإنتاج.
الخطوة الرابعة
تصنيع القوالب الدقيقة
يتم بناء القوالب المصنوعة من الصلب أو الألومنيوم باستخدام عمليات EDM أو CNC من قبل المهندسين ويتم إثبات متانتها من خلال صنع الكثير من القطع بنجاح.
الخطوة الخامسة
مراقبة الجودة والتعديلات
لذلك، في كل دفعة، يتم إجراء فحص الأبعاد (CMM) واختبار المواد في كل دفعة ويتم إجراء التعديلات اللازمة على الفور للوفاء بمعايير السيارات أو المعايير الطبية.
الخطوة السادسة
دعم التسليم وما بعد الإنتاج
تقوم المنشآت الحديثة في الصين والمكسيك بتجميع قطعنا، وإعطائها ملمسًا/طلاءً معينًا وشحن المنتجات النهائية في جميع أنحاء العالم. ويمكنك الاهتمام بصيانة الأدوات وتخزينها بنفسك.
تشمل حلول القولبة بالحقن المتكاملة التي نقدمها ما يلي:
- سوق دبي المالي
- تصميم القوالب
- اختيار المواد
- تصنيع القوالب
- التشغيل التجريبي
- مراقبة الجودة
- صيانة الأدوات
- إصلاح الأدوات
- عملية التشكيل
- تشطيب السطح
- التركيب
- المعالجة اللاحقة
- تجميع القالب
- التعبئة والتغليف
- التخزين
لماذا تختارنا كمورد قطع الغيار الخاص بك

خبرة واسعة
- لدينا فريق عمل مكون من أكثر من 40 شخصًا وخبرة كبيرة في مجال القولبة بالحقن منذ أكثر من 20 عامًا.
- لقد انتهينا من مشاريع القولبة بالحقن لقطع غيار في أكثر من اثنتي عشرة صناعة.
- تم حل العديد من مشكلات القولبة بالحقن بنجاح.
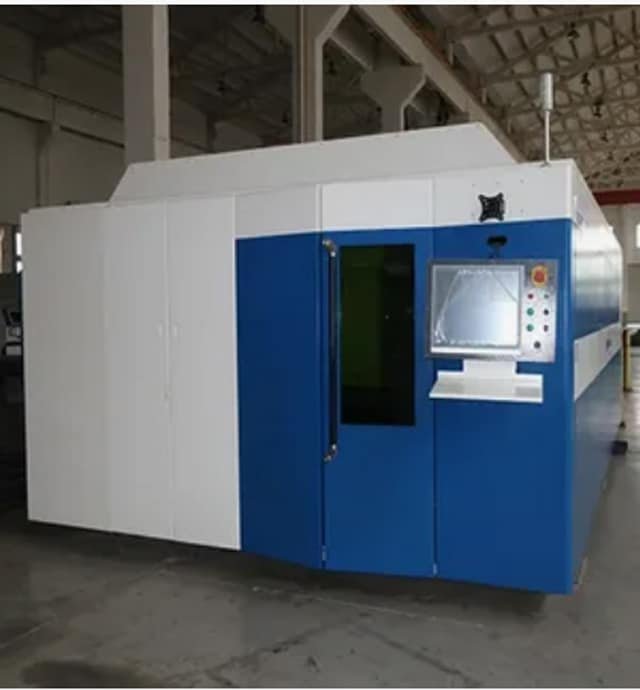
المعدات المتطورة
- يمكن لمركز التصنيع ضمان إنتاج القِطع بدقة تصل إلى ميكرون.
- ماكينات القولبة بالحقن القادرة على إنتاج أنواع عديدة من المنتجات وبحمولات مختلفة.
- تستخدم الشركة الكثير من المعدات لفحص الجودة، مما يساعد على التأكد من ثبات المكونات النهائية.
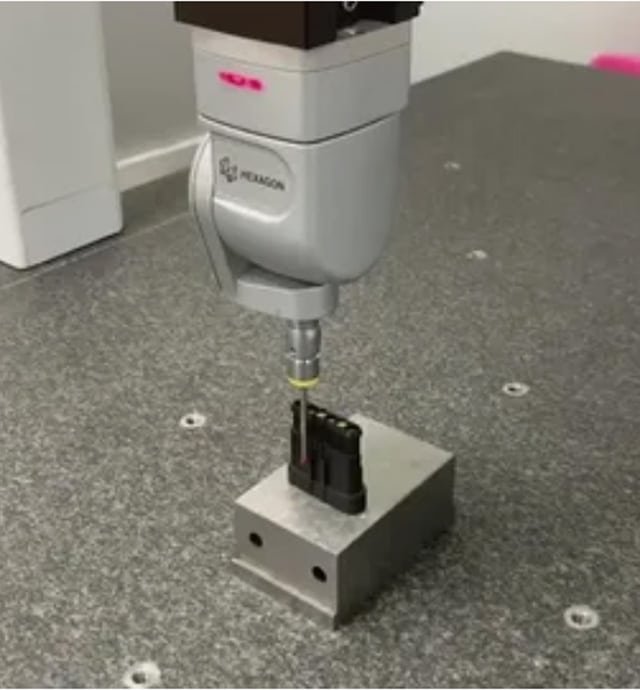
الفحص المتقدم ومراقبة العمليات
- للمراجعات التفصيلية والتحقق من جودة المنتجات، استخدم أحدث معدات CMM و NDT.
- لكي يبدو المنتج بشكل جيد ومنظم، تأكد من التركيز على المواد الخام والقوالب.
- لتقليل الأخطاء قدر المستطاع، انتبه لكل جزء من أجزاء العملية.
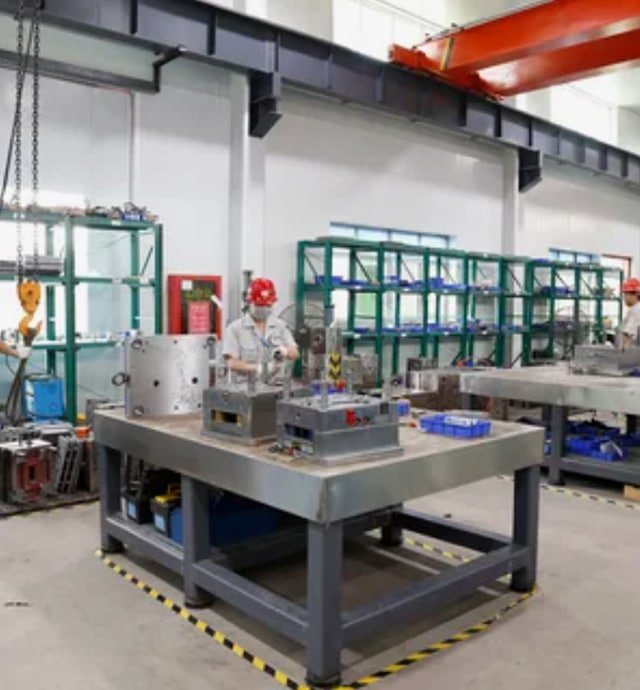
أحدث المعدات وفريق تصميم خبير في هذا المجال
- أحدث المعدات المستخدمة هنا هي المطاحن الدقيقة، وماكينات التآكل الشراري ومراكز الماكينات خماسية المحاور.
- يقدم فريقنا المتمرس من مصممي القوالب حلولاً يمكن تطبيقها على أرض الواقع.
- تُعد إدارة الإنتاج المثالية أمرًا حيويًا لمنشأة تصنيع القوالب والتجميع.
العناصر | الوصف | العناصر | الوصف |
---|---|---|---|
أبعاد الجزء القصوى: | 1600 مم × 1400 مم × 500 مم | الحد الأدنى لأبعاد الجزء: | 1 مم × 1 مم × 1 مم × 5 مم |
مجموعة المواد المستخدمة: | أكثر من 200 نوع، بما في ذلك المواد البلاستيكية المعدلة | مهلة حقن القالب بالحقن: | أسرع وقت للتسليم هو أسبوع واحد |
دورة القولبة بالحقن: | 20 ثانية للأجزاء الهيكلية العادية | قسم الأدوات والقولبة بالحقن: | أكثر من 130 موظفاً في مناصبهم |
التطبيقات في الصناعات المختلفة
يتم تصنيع الأجزاء البلاستيكية المبتكرة في صناعة السيارات والفضاء والأجهزة المنزلية والاستهلاكية والطبية والإلكترونية والروبوتات وغيرها من الصناعات بمساعدة القولبة بالحقن. فيما يلي قائمة بالصناعات الرئيسية التي تستخدم خدمات Zcmold كمورد موثوق به لقولبة الحقن.
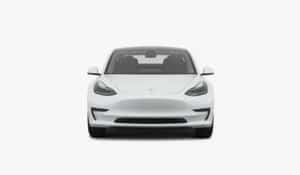
السيارات
مناسب لخزانات السوائل، والأجزاء الموجودة في حجرة المحرك، ولوحات العدادات، ووحدات وحدة التحكم الإلكترونية وأجزاء مختلفة.
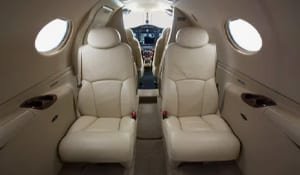
الفضاء الجوي
يجب أن تكون أشياء مثل أغطية الرادار، وحافظات الطائرات بدون طيار وأجهزة التحكم في قمرة القيادة قوية ومقاومة للنيران.
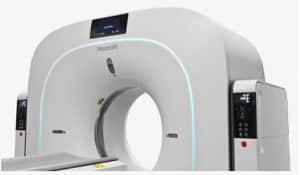
الطب الباطني
بدءًا من مرحلة التصميم، نشارك في تصنيع الأجهزة الجراحية والوصلات الوريدية وتغليف الغرسات ووحدات توصيل الأدوية وفقًا لإرشادات ISO 13485.
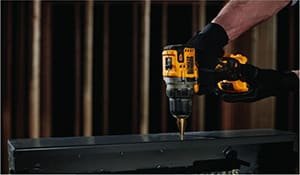
الأدوات والمعدات
الأجزاء المصنوعة من أجسام الصمامات الهوائية وواقيات الماكينات ومقابض الأدوات الكهربائية القوية ضد الصدمات والزيوت والاستخدام المنتظم.
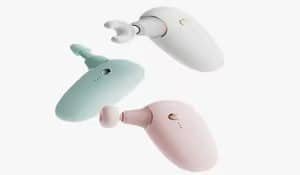
الإلكترونيات الاستهلاكية
استخدم أحدث التقنيات لإنتاج قطع إلكترونية تعمل بشكل جيد وتدوم طويلاً.
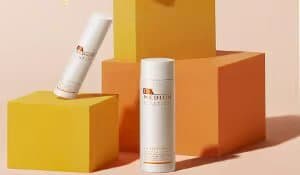
العناية الشخصية
يتم توفير عبوات مريحة لأجسام ماكينات الحلاقة المقاومة للماء ومقابض فرشاة الأسنان ومستحضرات التجميل والأشياء المماثلة.
مواد القولبة بالحقن
تستخدم عملية القولبة بالحقن أكثر من 200 مادة، منها ما هو للأغراض العامة ومنها ما هو هندسي ومنها ما هو عالي الأداء.
يساعد إجراء تعديلات على الجزيء أو إدخال الألياف أو إضافة مثبطات اللهب على تحسين المواد الأساسية. يمكن للناس استخدام أكثر من 18,000 مادة متخصصة متوفرة في جميع أنحاء العالم لتطبيقات مختلفة.
مبادئ اختيار مواد القولبة بالحقن لمصممي المنتجات
- يجب أن تكون المادة شفافة (PC أو PMMA)، ومقاومة للصدمات (ABS)، ومقاومة لدرجات الحرارة العالية (PC أو PEEK) وخفيفة (PP) وفقًا للوظيفة.
- يتم التسخين الدقيق للمادة من خلال الإشارة إلى انكماشها وسيولتها أثناء التشكيل.
- اختر المواد التي يمكن إعادة تدويرها والتي ليست باهظة الثمن. في الصناعات التي تخضع للوائح مثل المجالات الغذائية والطبية، اختر فقط المواد المعتمدة للأغذية أو التي تتحلل بيولوجيًا.
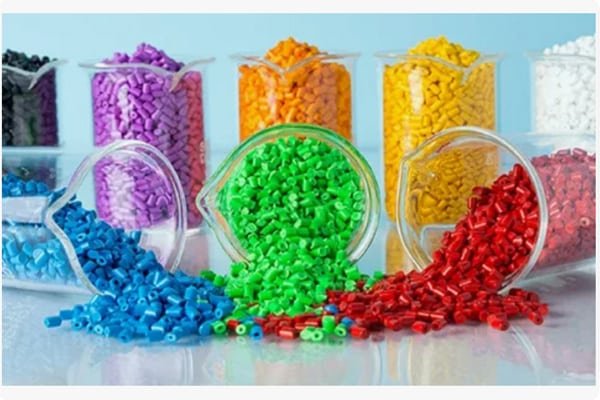
- ABS
- بى بى
- ملاحظة
- السلطة الفلسطينية
- كمبيوتر شخصي
- ص
- بولي كلوريد الفينيل
- بيك
- جزيرة الأمير إدوارد
- PBT
- بوم
- ب م أ م أ
- TPU
- TPE
- PC+ABS
- PA+GF
- PP+EPDM
- PA+ABS
- POM+GF
- PEEK+CF
التشطيب السطحي المخصص للأجزاء المصبوبة بالحقن
تعمل الأسطح جيدة التشطيب على تقوية العناصر الخاصة بك، وتجعلها تبدو جيدة وتدعم عملها بشكل صحيح. هنا في ZCMold، نقدم لك في ZCMold القوام والألوان والطلاءات التي تتماشى مع علامتك التجارية من خلال الجمع بين خدماتنا القياسية وفريق من الموردين المتخصصين الذين يتمتعون بخبرة تزيد عن 15 عامًا. وفي كلتا الحالتين، فإن النتائج ستلبي توقعاتك بغض النظر عما إذا كانت قطعك مصبوبة في المكسيك أو الصين.
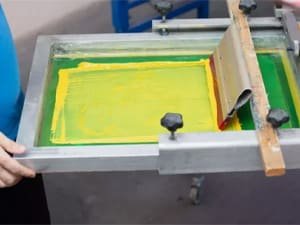
حلول تشطيب الأسطح الداخلية
اللمسة النهائية القياسية (SPI الفئة A/B)
- تُستخدم معايير VDI 3400 للأسطح ذات الحبيبات الدقيقة أو الأنماط الجلدية.
- الحصول إما على مظهر منخفض اللمعان أو غير لامع أو لمسة نهائية شديدة اللمعان حتى 0.05 ميكرومتر Ra.
- يؤدي استخدام خشونة موحدة (Ra 1.6-3.2 ميكرومتر) أثناء السفع الرملي إلى تعزيز قدرة الطلاء على الالتصاق بالسطح.
تقنيات التزيين
- في العملية المعروفة باسم طباعة الوسائد، يتم تطبيق النصوص والشعارات القوية على العناصر المنحنية (مقابض الأدوات والمعدات الطبية).
- ينتج النقش بالليزر علامات دائمة للشهادات مثل UL وISO والأرقام التسلسلية.
التشطيبات المتخصصة المعززة للشركاء
الطلاءات الوظيفية
- يعمل استخدام النيكل على حماية العبوات الإلكترونية من التداخل الكهرومغناطيسي والترددات اللاسلكية.
- يحمي الإلكترونيات الاستهلاكية من علامات الأصابع ويحميها من التعرض لأشعة الشمس.
العلاجات التجميلية
- عادةً ما يتم طلاء الزخارف وغيرها من ميزات هيكل السيارة بالكروم أو النيكل أو الذهب.
- إدخالات معدنية مصممة لمنتجات الألومنيوم المؤكسد الثابتة الألوان.
القولبة بالحقن مقابل الطباعة ثلاثية الأبعاد مقابل التصنيع باستخدام الحاسب الآلي: كيف تختار؟
تتمثل الطرق الرئيسية لصنع القطع البلاستيكية في التصنيع الآلي باستخدام الحاسب الآلي والطباعة ثلاثية الأبعاد والقولبة بالحقن؛ وهناك نقاط معينة يجب تذكرها عند اختيار مورد لكل عملية.
3 سيناريوهات رئيسية لاختيار القولبة بالحقن:
الطلب على الإنتاج الضخم
عدد أكبر من الوحدات يعني تسليمًا أسرع؛ حيث يمكن أن تكون نفقات الطباعة ثلاثية الأبعاد 101 تيرابايت لكل قطعة فقط عندما يزيد عدد القطع عن 500 قطعة.
متطلبات أداء المواد
القدرة على تحمل درجة حرارة تصل إلى 120 درجة مئوية أو خاصية التمدد مثل أختام السيليكون.
اتساق العلامة التجارية
لا يمكن تثبيت المظهر والقوام واللون المناسبين للعديد من الوحدات في التصنيع الضخم إلا بتناسق 99% عند استخدام قوالب الحقن لصناعة المكونات.
العامل | القولبة بالحقن | الطباعة ثلاثية الأبعاد | التصنيع الآلي باستخدام الحاسب الآلي |
---|---|---|---|
الدفعة المثلى | أكثر من 1,000 قطعة (قوالب فولاذية) | 1-100 قطعة (نماذج أولية/دفعات صغيرة) | 1-500 قطعة |
التكلفة لكل وحدة | رخيصة | متوسط | باهظة الثمن |
اختيار المواد | أكثر من 200 من اللدائن الهندسية/اللدائن البلاستيكية الهندسية (ABS، والكمبيوتر الشخصي، وLLSR، وغيرها) | محدودة (بشكل أساسي PLA، الراتنج) | بلاستيك محدود |
المهلة الزمنية | صنع القوالب: 7-30 يومًا؛ الإنتاج الضخم: 1-3 أيام لكل 10,000 قطعة | لا حاجة للعفن، 1-5 أيام توصيل خلال 1-5 أيام | لا حاجة للعفن، 3-10 أيام |
الدقة | ± 0.1 مم، قوام VDI 3400 | ± 0.3 مم، تتطلب علامات الطبقات معالجة لاحقة | ± 0.05 مم، صقل المرآة |
الاستدامة | عالية (المواد القابلة لإعادة التدوير، معدل النفايات <5%) | منخفض (الراتنج غير قابل لإعادة التدوير، نفايات مواد الدعم 30%+) | متوسط |
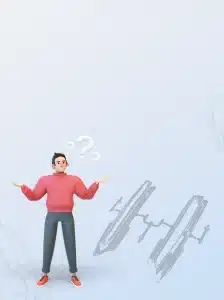
الأسئلة الشائعة حول قولبة الحقن بالحقن
عليك أن تأخذ في الاعتبار عدة عوامل مختلفة عند اختيار مزود خدمة صب الحقن المناسب.
أولاً، قسّم المعدات ومدى إمكانية استخدامها. يجب أن يلبي حجم الماكينة ودقتها متطلبات منتجاتك. وعلاوة على ذلك، تأكد من أن عدد الماكينات ومستوى الأتمتة سيساعدان على توفير التصنيع الفعال والوفاء بالمواعيد النهائية.
ثانياً، تأكد من ملاحظة كيفية التحكم في الجودة في الشركة. تأكد من أن المزود حاصل على شهادة الأيزو 9001 وأن أدوات وأساليب الاختبار الخاصة به تتم صيانتها بشكل صحيح.
ثالثاً التأكد من حسن إدارة وتوريد المواد المطلوبة. تأكد من أن لديهم المنتجات البلاستيكية المطلوبة حتى تعرف أنه سيتم التعامل معها بشكل صحيح وصيانتها لتبقى في حالة جيدة.
تحقق من خبرة المرشحين في مجال التكنولوجيا أيضاً. فاختيار المورد الذي يتمتع بخبرة وخبرة مثبتة في هذا المجال يضمن لك خدمات أفضل.
من المهم أيضًا مراعاة جودة خدمة مقدم الخدمة ومدى سرعة استجابته. يجب أن تضمن الشركة الدعم بعد إجراء عمليات الشراء والتواصل الممتاز.
يجب الموازنة بين التكلفة والسعر في نهاية العملية. بعد مراجعة الجودة وتكلفة التصنيع وغيرها من التفاصيل الضرورية، اختر المزود الذي يمنحك أكبر قيمة من أموالك. ونتيجة لذلك، ستتمكن من العثور على شركة قولبة الحقن المناسبة لمشروعك.
يجب التحقق من عدة عناصر لتحديد ما إذا كان التصميم مناسبًا للقولبة بالحقن: شكل المنتج، ونوع المادة المستخدمة، وكيفية أدائه، وما إذا كان القالب يمكن إنتاجه.
فيما يتعلق بسماكة الجدران في المنتج، تأكد من أنها متجانسة. حاول الحفاظ على سُمك متجانس على الجدران لإيقاف المشاكل المرتبطة بالتشوه غير المتساوي والتغيرات في درجات الحرارة. تأكد من أن الزوايا التي تستخدمها تتيح لك تحرير القالب بسهولة. رتب أضلاع التسليح بشكل مناسب حتى لا تظهر على المنتج علامات انكماش غير مرغوب فيها. من المهم أيضًا النظر إلى أحجام وأشكال الثقوب والأخاديد لدعم عملية التشكيل بالحقن.
يجب أن تتلاءم المواد مع تجويف القالب بسلاسة وبشكل مناسب لكل من تركيبها وطريقة عملها. اختر المواد التي تتناسب مع أغراض العناصر الخاصة بك وكذلك مظهرها.
إذا كانت فحوصات الجدوى تشير إلى أن القوالب الخاصة بمشروع ما سيكون إنتاجها صعباً ومكلفاً، فتجنب القيام بالمشروع لتجنب مواجهة تحديات إضافية. تأكد من إمكانية إكمال جميع أجزاء التصميم الخاص بك باستخدام الأدوات والمعلومات المتاحة لك.
بالفعل. فيما يتعلق بالمعدات، توفر zcmould آلات التشكيل التي تستخدم أدوات الحقن. يعد استخدام ماكينات القولبة بالحقن صغيرة الحجم مناسبًا للمنتجات البلاستيكية الأصغر حجمًا نظرًا لسهولة إعدادها وإصلاحها. تستخدم ZCmould القوالب السريعة لخفض نفقات الإنتاج.
يتم تعديل طريقتنا في التعامل مع تكاليف التصنيع على دفعات صغيرة بشكل مختلف عن الإنتاج على دفعات. تتسم أسعارنا بالواقعية لأننا نقوم بتضمين تكاليف الشراء ونفقات الإنشاء والعناصر الضرورية الأخرى. وفي الوقت نفسه، نظرًا لأن العملاء المختلفين لديهم احتياجات فريدة من نوعها، فإننا ننفذ الإنتاج على دفعات صغيرة لمساعدة العلامات التجارية المتخصصة والشركات الإبداعية على تعزيز مزاياها.
تلعب ثلاثة جوانب رئيسية في تصميم المنتج دورًا في خفض تكاليف القولبة بالحقن.
يجب أن يكون تحسين بنية المنتج هو الأولوية الأولى. ونتيجة لذلك، يكون الوقت اللازم للقولبة بالحقن أقل، حيث أن سمك الجدار يظل كما هو ولا يختلف بأكثر من 25%. كما أن طريقة تصميم أضلاع التقوية مهمة للغاية. يجب ألا يزيد السُمك عن 60% إلى 70% من إجمالي سُمك الجدار، لزيادة قوة المنتج وتقليل فرص حدوث عيوب. يجب عليك دمج زوايا السحب الصحيحة في التصميم أيضًا. لتقليل المدة التي تستغرقها عملية إزالة القالب من السلعة ومنع حدوث تلف، يجب أن تكون زوايا الجوانب بزاوية 1° - 2° من الداخل وفوق 0.5° - 1° من الخارج.
تأكد أيضًا من زيادة نوع المواد التي تستخدمها إلى أقصى حد. اختر الموارد المناسبة لوظيفة المنتج لتجنب استخدامها غير الضروري. انظر أيضًا إلى سهولة التعامل معها واختر تلك المواد البلاستيكية التي لا يصعب معالجتها، لأن ذلك سيقلل من التكلفة والوقت اللازم.
ثالثًا، جعل تصميمات المكونات المختلفة أكثر توحيدًا وتنظيمًا. دمج عدة قطع في جزء واحد مصبوب يقلل من الأجزاء اللازمة للمنتج. كما أن جعل التصميم الخارجي أقل تفصيلاً من خلال تجنب الأشكال المعقدة والزخارف يمكن أن يقلل من تكاليف القوالب ويجعل عملية تصنيع البلاستيك أسهل.
نحن نوفر حلولاً كاملة لقولبة الحقن للمساعدة في تحويل الأفكار الإبداعية إلى واقع ملموس وتوفير فرص للتخصيص. ونظرًا لأننا نتولى تغيير المواد، فهناك رسوم منخفضة للإدارة، مما يضمن أعلى جودة في تطبيقات الألوان المتعددة. يتيح لك القيام بهذا الإجراء التشغيلي القياسي منع خلط منتجك أثناء الإنتاج مما يحافظ على تماثله في كل دفعة.
يساعد استخدام مزج الألوان المتقدمة والتكامل في عمليات القولبة بالحقن لدينا على إنشاء تصميمات فائقة وأداء أفضل. نتيح للمصممين تطوير تقنيات فريدة من نوعها للأغراض الطبية أو الألوان الأنيقة للأجهزة الاستهلاكية.
ظهور الألوان الرئيسية لعلامتك التجارية في مقاطع الفيديو الموسيقية الخاصة بك
تعديل العقد لكل من التحقق من اللوائح التنظيمية والاستخدام اليدوي