Computer Numerical Control (CNC) machining is a flexible manufacturing process that can produce complex parts out of material pieces by scientifically controlling the machinery’s movement. The process incorporates the utilization of a wide range of materials which are selected based on their individual characteristics and suitability to respective applications. The choice for the material is of great importance for the quality, course, and performance of the final product. In this article, we will discover how the most common cnc materials used for CNC machining are, their properties and their availability in different industries.
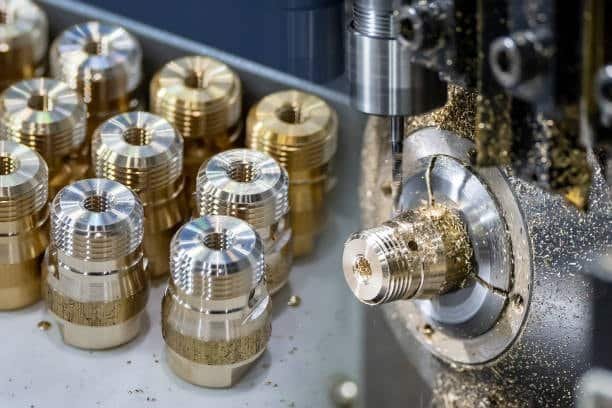
Specifically, such metals as aluminum, alloy steel, steel alloys brass alloy, and titanium are most commonly used in CNC machining thanks to their strength, durability, and machinability. For example, a lightweight characteristic of aluminum alloys and excellent thermal properties have made it one of the best in the aerospace and automotive industry, along with low carbon steel . Steel has better strength and is usually chosen for the structural elements, while titanium is distinguished in medical and aerospace fields due to its biological compatibility and objects’ protection from the corrosion. On the other hand, plastics such as ABS, nylon, PEEK are used if the lighter, non-conducting, corrosion-free parts are required, especially, in the production of electronics and medical devices. Appreciation of the distinct aspects of a material permits the suppliers to attach the material suited to the desired use hence improving the functionality, lifespan, and cost-efficiency of the product.
Types of Materials Used in CNC Machining
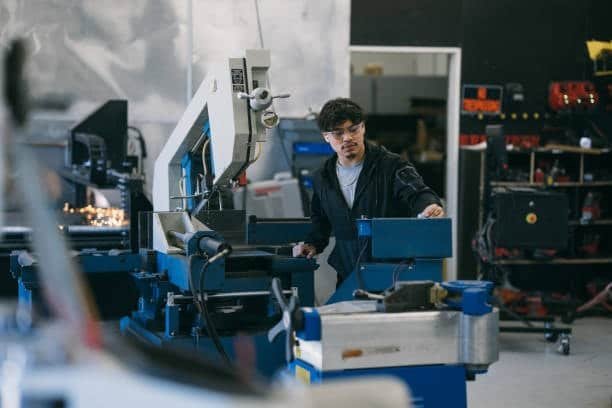
CNC machined materials can be classified as metals, plastics and composites depending on the end product properties which serve as unique advantage based on properties seek on the latter. Let us now take a closer look at each material type:
1. Metals in CNC Machining
CNC machining utilizes metals the most often because they are strong, durable, and have a variety of uses. They include some of the most popular metals such as:
- Aluminum: Aluminum is one of the most widely consumed substances in CNC machining. Characterized for being lightweight, it is resistant to corrosion making it suitable for use in the aerospace, automotive and electronics industries. Its high machinability permits quite complicated designs and very tight tolerances.
- Steel: Another widely used material in CNC machining is steel which is highly strong and irreducible wear. Various levels of steel, such as stainless steel, carbon steel, and tool steel, offer variances for each specific demand. Stainless steel for instance is preferred because of its anticorrosive property, tool steel is preferred for its hardness and cutting nature in service.
- Titanium: Titanium is a high-performance metal, which has an outstanding strength/weight ratio, and which is resistant to corrosion. It is widely applied in the aerospace industry, the medical field and highly performing engineering parts. Titanium calls for a special kind of machining because it is hard and produces heat in its machining.
- Brass: Brass is a copper alloy which is commonly used due to its machinability and corrosion resistance. It is regularly used in the field of precision machining in such applications as valves, fittings, etc. and electricaly connectors.
- Copper: Copper is a very good conductor and it is often used for electric elements and heat exchangers in CNC machining. It is also prized for its corrosion-resistance and ease to machine it to become intricate shapes.
2. Plastics in CNC Machining
Plastics are finding application in CNC machining because they are very light, inexpensive, and versatile. Some common plastics used include: nylon and acrylonitrile butadiene styrene, which are favored for their unique properties.
- Acrylic: Acrylic is a clear plastic that is widely used in CNC machining where clarity of vision is necessary, i.e. sign displays, and optical lenses. It provides quality weather resistance and it is readily machined, this makes it suitable for forming detailed and complex parts.
- Polycarbonate: Polycarbonate is recognized for its toughness and impact resistance and in this respect it is possible to use this material for durable application for example on car parts or on covers for protection. It also has a good machinability but is more w hard to cut compared to acrylic.
- Nylon: Nylon is a tough and wear/ friction resistant plastic material that is perfect for making gears, bearings and other machine parts. It is also extremely resistant to chemicals and moisture and is therefore a common material used on several industrial applications.
- Delrin (Acetal): Delrin or acetal is a very strong plastic used in many different applications that require minimal friction and a high degree of precision, bushings gears, automotive parts and such. The durability against wear and fatigue makes it an ideal for feats environments.
- Polyethylene: Polyethylene is one of the PLC most used in the CNC machining, oil resistant and very low friction to deal with. It has prevalence in applications in such as food processing, packaging and industrial parts.
3. Composites in CNC Machining
Composites are composed of two or more different materials that have been combined together to form a material having improved properties. The CNC machining technology provides accuracy of forming composite materials used in different high-performance applications, ensuring dimensional stability .
- Carbon Fiber Reinforced Plastics (CFRP): CFRP consists of carbon fibers and resin with outstanding strengths to the weight and stiffness. It has a wide application in aerospace and automobile products involving lightweight materials for optimum performance. It is difficult to machine carbon fibre but with CNC machine it is easy to work with such material with their specific tools.
- Glass Fiber Reinforced Plastics (GFRP): Yet, GFRP is another composite material that is quite durable with a high resistance to corrosion. It is used for application where high strength and resistance to environmental conditions are needed. CNC machining is widely used to produce GFRP into parts in industries such as construction, Marine and Automotive.
- Kevlar: Kevlar is a high strength yarn and is used for those applications which require maximum toughness and impact resistance. Ballistic protection, aerospace, and sports equipment are common examples of the it being used. CNC machining of Kevlar is not easy through regular opposite due to its abrasive characteristic.
Factors to Consider When Selecting CNC Machining Materials
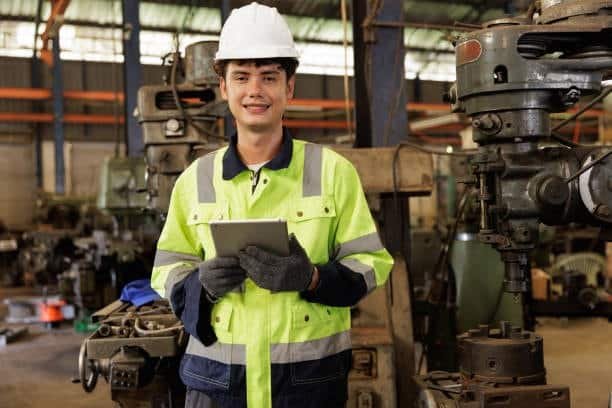
The choice of appropriate material selection for an CNC machining project needs to be thought through carefully with respect to various aspects like industrial applications :
- Mechanical Properties: The required strength, hardness, and fatigue resistance for the part must be consistent with the intended use of the part.
- Machinability: Easier to machine materials will generally cost less and we can produce faster. Aluminium for instance, is more machinable than other metals like hard metals such as titanium.
- Thermal Properties: Some materials can endure high temperatures, such as steel and titanium, but will bend under high temperature and should not be used in parts exposed to heat, whereas others, such as plastics, will melt under heating.
- Cost: The cost of the material is an important parameter, especially in high-volume production. Although metals such as aluminum are comparatively cheap, special metals such as titanium can be costly.
- Corrosion Resistance: In case the part will be exposed to tough or corrosive substances, such as in case of stainless steel or plastic, the focus should be placed on selecting resistant to corrosion.
CNC Machining in Aerospace Industry: Precision and Reliability
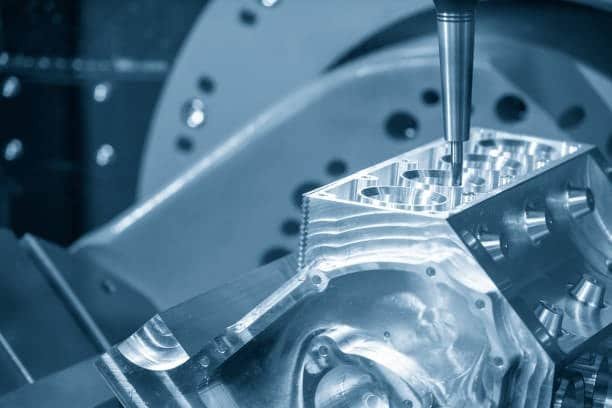
CNC machining is very critical in the aerospace industry, where components produce must have impeccable precision and reliability. The industry has the need for parts that will be able to withstand extreme situations such as high pressure, high heat resistance, and temperatures and corrosive environments. Metals like titanium alloys, aluminum, and high-strength steel are common corrosion resistant materials used in aerospace applications because of their superb strength-to-weight ratios and resistance to environmental degradation. CNC machining guarantees high accuracy when it comes to cutting and shaping of the aforementioned materials, so as to produce complex parts such as turbine blades, airframes, and engine components.
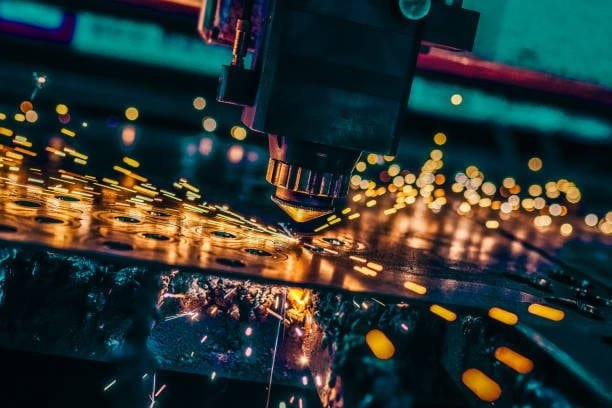
The CNC machines’ capabilities to run with close tolerances and repeatability are paramount in the aspect of ensuring that aerospace parts are safe and regulated as per performance requirements. Additionally, the ease with which the CNC machining is adjustable promotes rapid prototyping and creation of custom products allowing the manufacturers to instantly adapt to the design changes and enhance the performance. Through continued progress in the materials and machining technology, the CNC machining continues to be one of the pillars of the modern aerospace organization where up to the point lighter, stronger and better machinery components for the next generation aircraft are produced, ensuring structural integrity .
CNC Machining in Medicine Industry: Biocompatibility and Precision
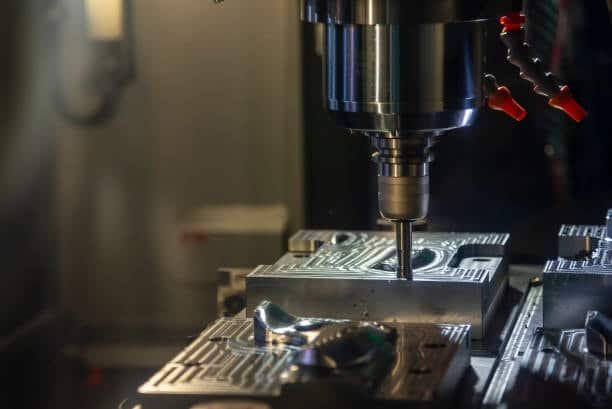
CNC machining is used by the medical industry to provide highly specialized, precise and biocompatible components to satisfy many applications. Examples of the material used in making medical devices and electrical components include titanium, stainless steel, plastic resin and PEEK which are not only strong, corrosion resistant, and compatible with a human but also can be electrically conductive. Through the application of CNC machining, these materials are worked on so as to achieve the stringent demands for medical implants, surgical tools and prosthetics. The close tolerances generated by CNC machines allow for the production of parts with high-level arrangements of micro-features which minimizes the risk of having defects that would jeopardize patient’s safety.
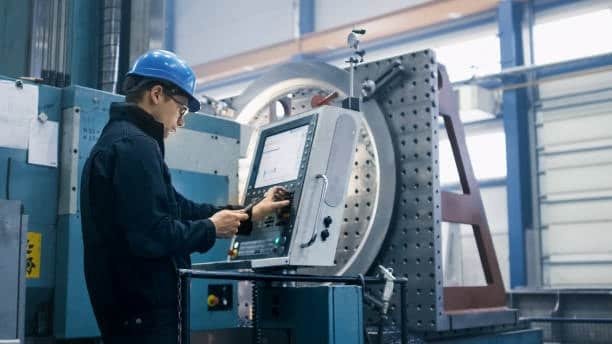
Besides, the machines’ ability to machine complex geometries serves to come with medical devices with unique requirements for individual patients. Whether it’s a customized knee implant or an advanced surgical tool, CNC machining offers the precision that is necessary for machines that operate at the optimal level within the human body. The role CNC machining comes to play as the field of medical technology progresses becomes increasingly more important in the experimentation and development of innovative solutions which improves patient outcomes and performance of medical treatments.
CNC Machining in Automotive Manufacturing: Efficiency and Performance
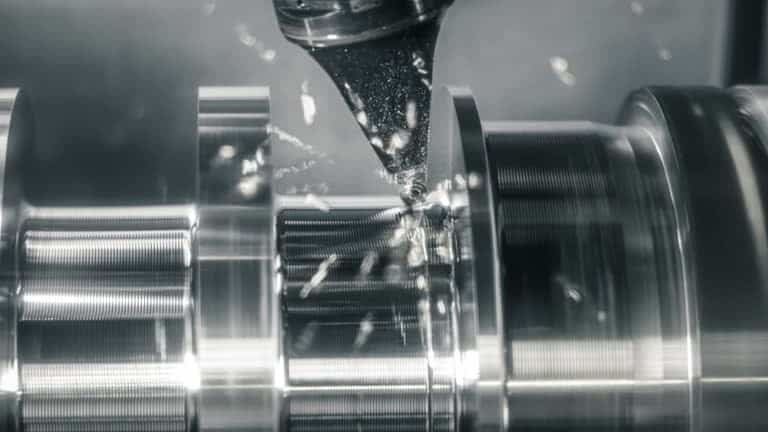
CNC machining cannot be spared in the automotive industry where precision and cost-efficiency plays a crucial role when it comes to high-performance vehicles. While materials including aluminum, low carbon steel, metal alloys and mild steel composites are popular for utilization in the automobile industry, all the way from the creation of engine parts to complicated interior elements are done using CNC machines. The lightweight nature of aluminum makes it a perfect choice for autos in relation to fuel-efficiency, while steel provides strength and endurance for load connected parts such as chassis, and suspension systems. Such precision in working with materials with wear resistance and containing harmful components is ensured by CNC machines, which results in vehicles becoming more safe and efficient.
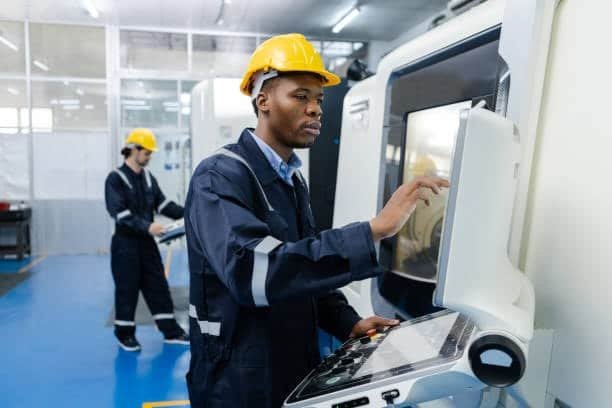
Aside from the creation of structural components, CNC machining is also used in the development of custom parts and prototypes, which enable the automotive manufacturers to work with newer designs and technology. From high-performance engine parts to light body components, the versatility of CNC machining is able to cater to the different needs of the automotive industry by selecting the right materials . CNC machining helps manufacturers to respond to the rising demand for performance, automotive components wear resistance safety, and sustainability in today’s cars due to its ability to allow for faster production cycles and optimized materials for cnc machining with less material waste.
CNC Machining for Prototyping: Time and Efficiency in Product Development
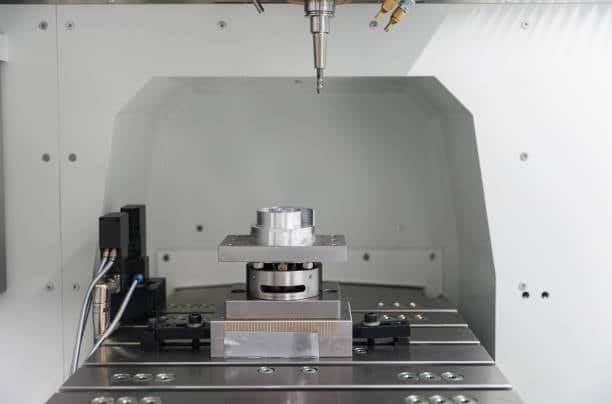
Prototyping is an important part of the product development process, and the speed and precision provided through CNC machining allow bringing ideas to life rapidly and efficiently. Manufacturers are able, using CNC technology, to make finite, functioning prototypes from many different materials so that designers can test their ideas and improve them before full-scale production. When it comes to using metals such as medium carbon steel for structural prototypes or plastics for more lightweight, flexible prototypes, CNC machining guarantees that the prototypes meet high precision levels and there is the reduced probability of costly mistakes at the final production stage.
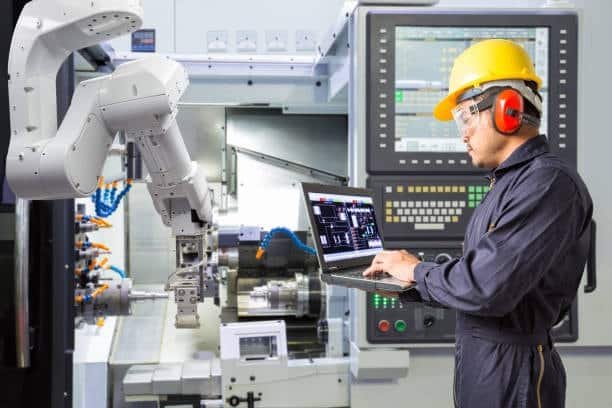
The quick prototyping abilities of the CNC machining can also yield iterative tests and design changes so that engineers can modify their designs after getting real-world feedback. This function makes the process of development faster and easier, and companies can release innovative products to the market without waiting too long. With their ability to cut down on classical prototyping time and cost, CNC machining is a resourceful tool for companies who wish to stay competitive in cutting-edge industries.
The Future of CNC Machining: The progresses in Automation and Smart Manufacturing
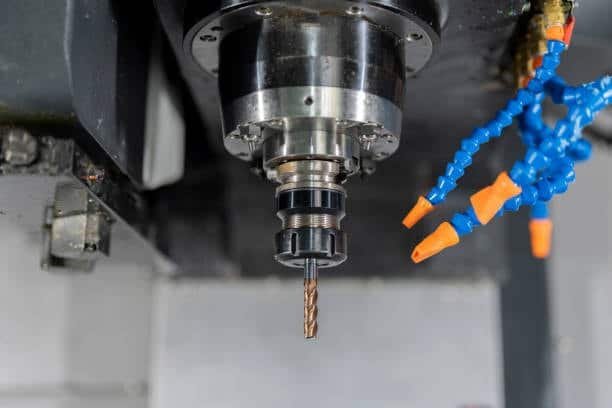
The future of CNC machining is more and more associated with the automation and smart technologies. The combination of IoT (Internet of Things) sensors together with AI-powered analytics and machine learning algorithms is changing the paradigm in the way CNC machines are being operated. Such developments allow monitoring of the machine performances in real time, predictive maintenance, and automatic adjustments to cutting parameters for optimization. Equipped with these abilities, CNC machines can work without laborious human interference and increase production efficiency.
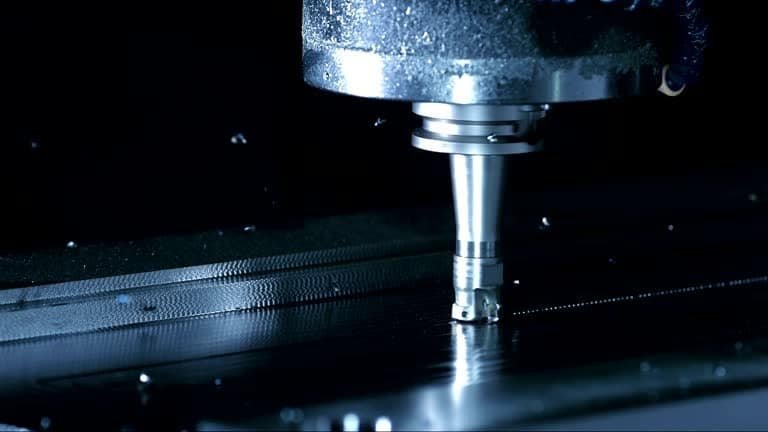
Smart CNC machines can also learn from previous machining processes and improve their accuracy and flexibility constantly using the past processes. Not only do such automation levels decrease labor expenses but they also create product uniformity and quality. With further development of these technologies, the manufacturers can anticipate even higher levels of integration, which will lead to smoother and more efficient production process. In future, CNC machining will continue to be a key area of focus in the development of innovative products in many industries, due to the increasing automation, data analysis, and application of artificial intelligence in it.
Conclusion
CNC machining provides versatility because one can work with a broad range of materials specifically amended to different applications. If you required the power of metals such as Steel and Titanium, including various metal alloys the machinability of free machining brass and plastics such as Nylon and Acrylic, or the advanced properties of composites such as Carbon Fiber, the right cnc machining materials can deliver the precision CNC machining can deliver the precision and capabilities that mechanical engineers and the manufacturing YMCA would demand. The material selection for common cnc materials cnc machined components has a big impact on the machining process and knowing the specifics of all the materials is vital to obtain the best possible outcome.
Also, the machinability of every material affects the choice of tools, cutting speed, the rate of feed and cooling needs, which all have a direct impact on production efficiency and the quality of finishing surfaces. For instance, it may be necessary to use slower cutting speeds with harder materials such as stainless steel which would also require appropriate cutting tools in order to prevent extreme wear and overheating but softer materials like plastics may need more thoughtful handling whereby warping or melting could be avoided. Composites, despite being light and strong, require sophisticated techniques on many occasions because of their layered structures, tendencies to delaminate. As CNC machining progresses, so does its degree of accuracy in its ability to adapt to such a variety of materials which allows manufacturers to drive design frontiers while still remaining cost-effective and product faithful through the gambit of industries.