Custom Mold Design & Manufacturing Services | Professional Mold Making
Comprehensive mold solutions including design, manufacturing, processing, inspection, and maintenance. Precision mold services for a wide range of global industries.
- 12+ years specializing in injection and die-casting mold production.
- Proficient in designing intricate molds, with delivery in as little as 7 days.
- High-quality guaranteed at competitive prices.
If needed, we can sign an NDA agreement before providing the quotation.
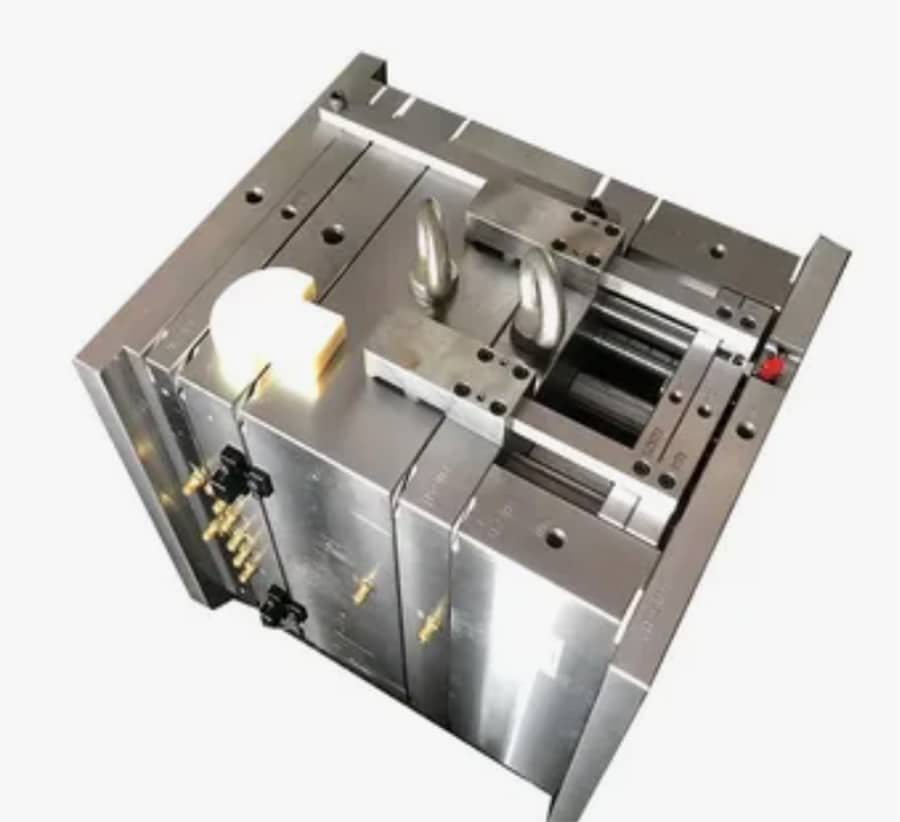
Mold Manufacturing Classification
What Mold Manufacturing Services Does Zcmould Provide?
Injection mould production and die-casting mould production are the two main categories of mould manufacturing services, determined by the type of mould to use in the following processes. The service we are most proud of is designing and making injection moulds.
Services are classified as production tooling or rapid tooling which depends on the longevity or the number of pieces your mould is expected to produce. The shorthist turnaround time for rapid tooling may be seven days.
We also give clients the option of precision mould making, a service valued by clients with very strict requirements for part quality.
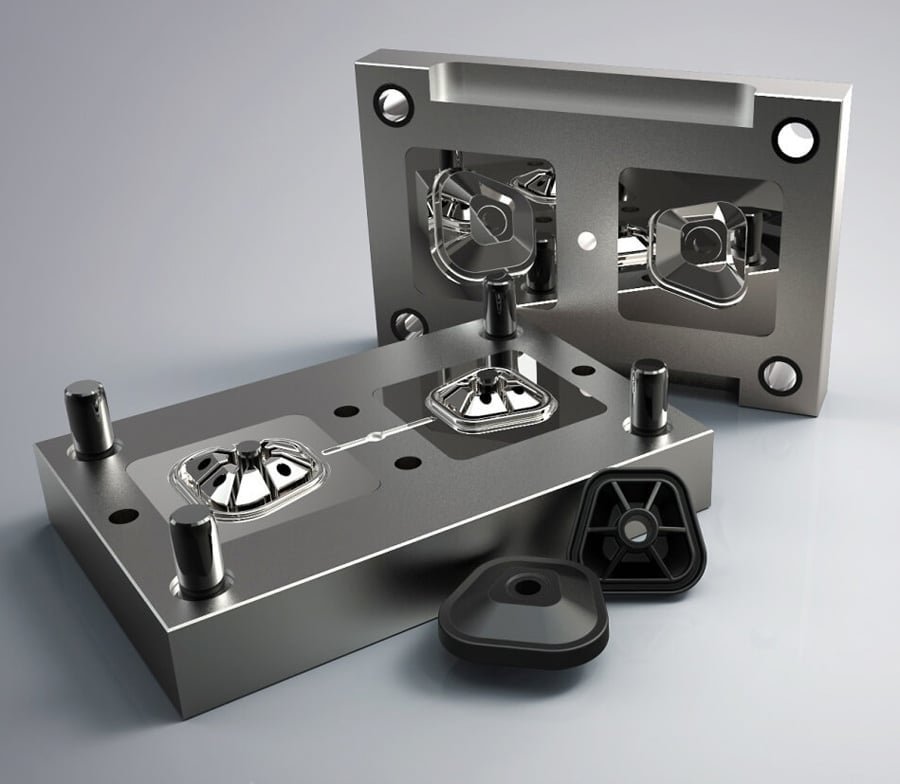
By Molding Process
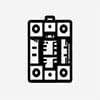
Injection mold making
Efficient for large-scale production of precise plastic components.
By Production Volume
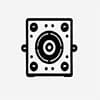
Rapid tooling making
Fast turnaround, ideal for low-volume production.
By Precision
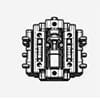
Precision mold making
Exceptional accuracy, tight tolerances, and complex structures.
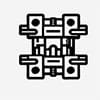
Die casting mold making
Perfect for producing high-strength metal parts with complex designs.
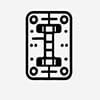
Production tooling making
Moderate lead time, ideal for large-scale production.
Step-by-Step Guide to the Precision Mold Manufacturing Process
Typically, Zcmould breaks the mold manufacturing process down into 12 steps.
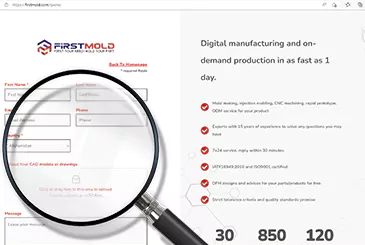
01
Drawings Receiving
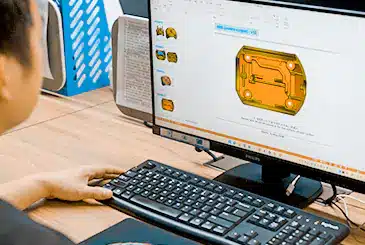
02
DFM Review
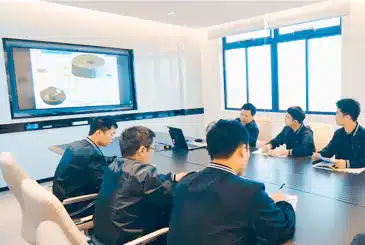
03
DFM Permitted
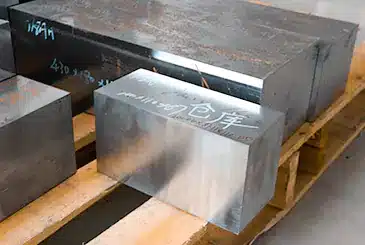
04
Materials Preparation
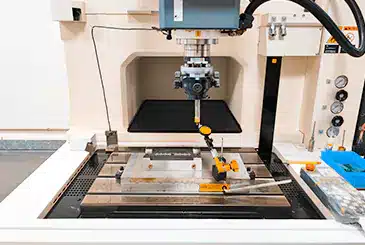
05
EDM Machining
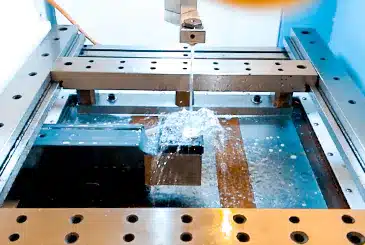
06
Wirecut Machining
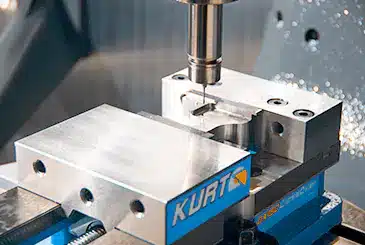
07
Mecanizado CNC
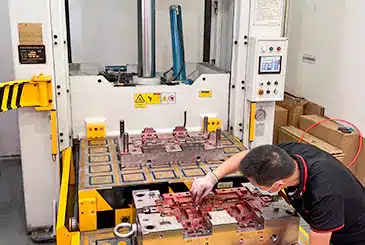
08
Mold Fitting
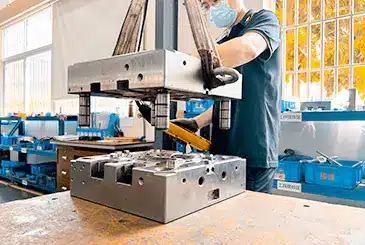
09
Core Fitting
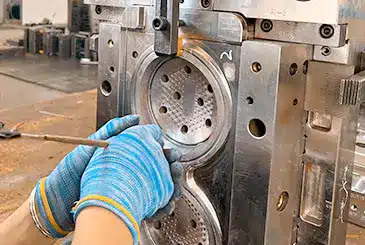
10
Mold Polishing
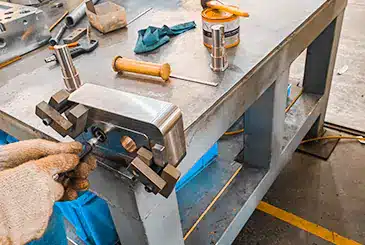
11
Mold Fabrication
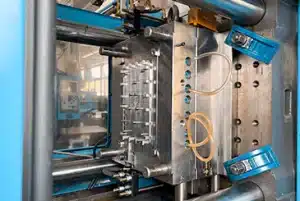
12
Mold Trial
Perfect Design, Precision Perfected
Common Issues You Might Be Struggling With
In the past, your current suppliers may have caused the following challenges.
Excessive Molding Defects
Burns, flow lines, air pockets, uneven depths, flash points and short fills may appear on the product.
Rising Hidden Costs
Longer filling times and poor communication between the producer and the shipper cause additional hidden costs.
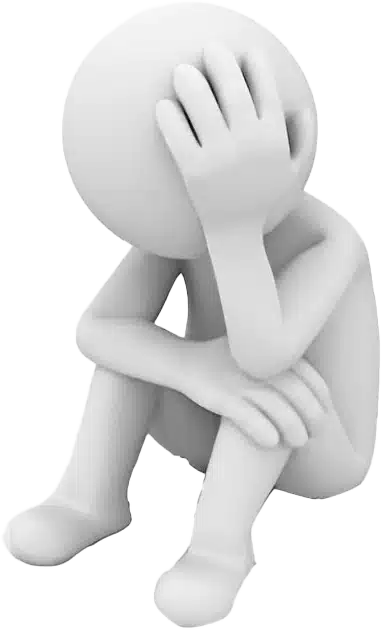
Frequent Mold Trials
Problems with the design or process tend to result in the need for several repairs and more time required for project completion.
Delivery Delays
There are often various reasons suppliers cite, so the delivery schedule keeps being moved back.
How Zcmould Solves Mold Problems
A supplier’s true strength lies in proactive coordination, effective communication, and accurate problem-solving.
Design
Rigorous mold design, Most of the molds can be used in mass production in one mold trial.
- We stop issues from happening at zcmould, not only react to them when they occur. We check wall thickness, observe any deformations and make sure gate placement is correct, all before they can harm your project by looking closely at the properties of the materials and testing the product early on.
- We feel strongly that innovation takes real teamwork as its foundation. To know exactly what the clients expect in terms of bonding lines and finish, we frequently communicate with them. This guarantees the product turns out better than their expectations.
- Architects talk about the structure of the programme before they design. By using detailed checklists, the design is checked without assistance. Business and manufacturing teams collaborate to review everything after designing.
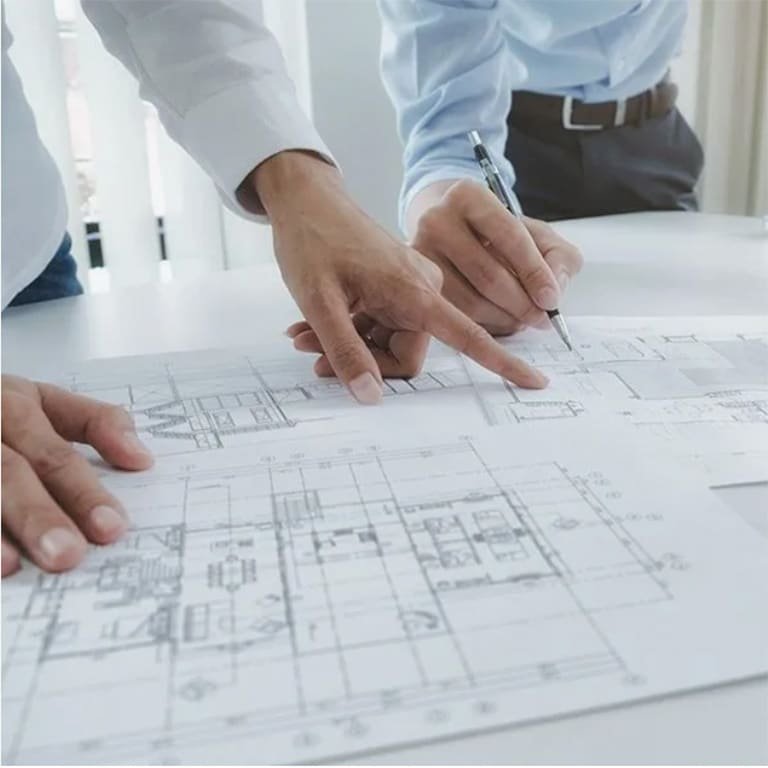
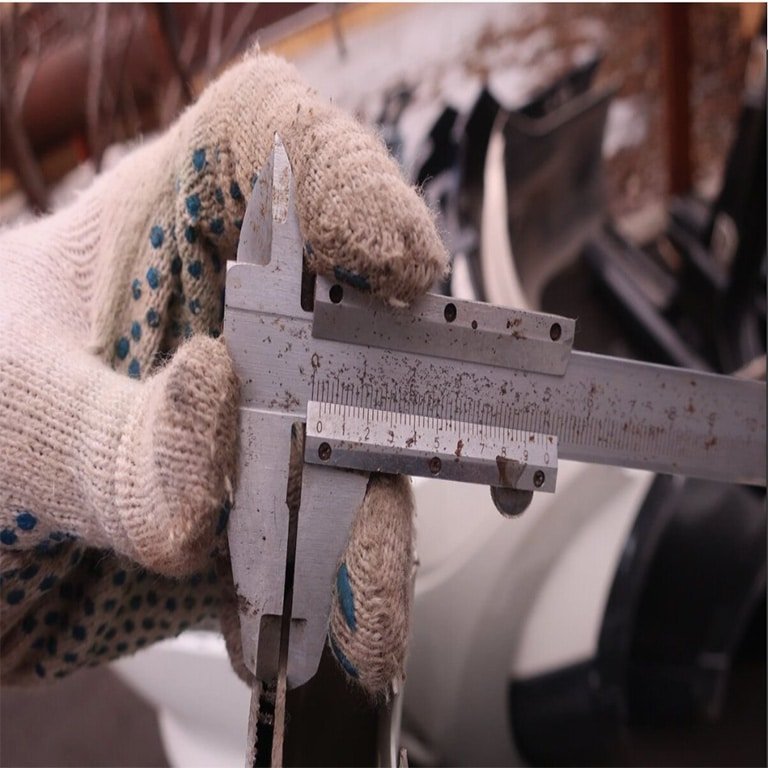
Quality
Quality checks at every stage to identify potential production issues early.
- At each step, from the start with raw materials to production and finishing, quality inspection is done to find possible problems in advance.
- Each product has a set of inspection reports attached so it can be easily traced.
- Our products provide excellent value because we use superior materials and keep closely to the standards set by SPI.
Delivery Time
Provide weekly updates to keep customers informed of the progress at all times.
- A project manager is in charge of every project and the schedule is tracked and respected.
- Clients are given weekly reports and mold pictures to keep them up to date.
- Video clips of the mould trials can be viewed online by clients to watch it working in practice.
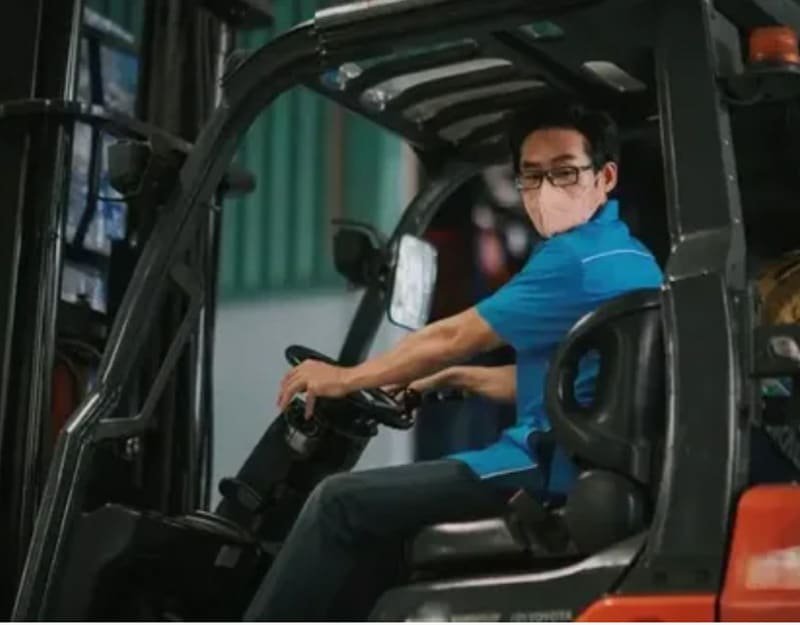
Watch a Video of Our Plastic Mold Making Services
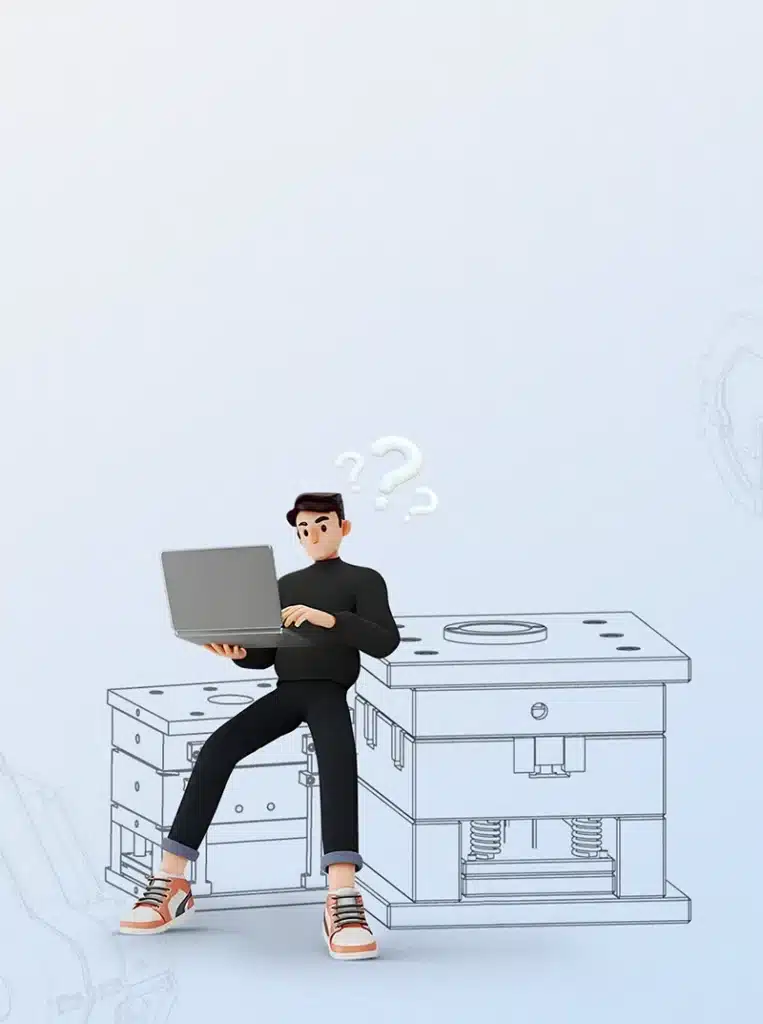