Precision and accuracy are very important in the world of CNC (Computer Numerical Control) machining. Tool radius compensation (TRC) is used to account for cutter radius, to maintain final part dimensions regardless of if the cutter used is perfectly centered. This article defines what tool radius compensation and cutter radius compensation are, how they work, their advantages, and challenges involved –a full picture for those engaged in CNC machining.
What is Tool Radius Compensation?
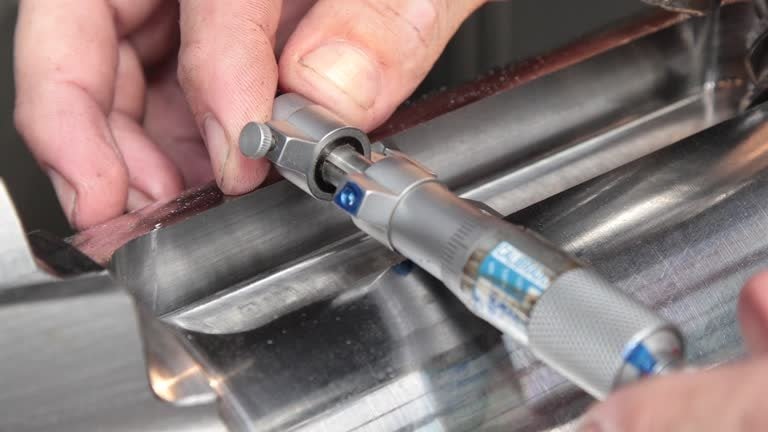
The feature of tool radius compensation makes it possible to take into consideration the radius of the cutting tool for machining during its programming. With machining a part, its own tool diameter and radius of the tool nose has an effect on the dimensions of the finished work, influencing the actual tool path . If uncompensated, a tool size can cause deviations to the geometry of the part making it somewhat large or large.
How Tool Radius Compensation Works
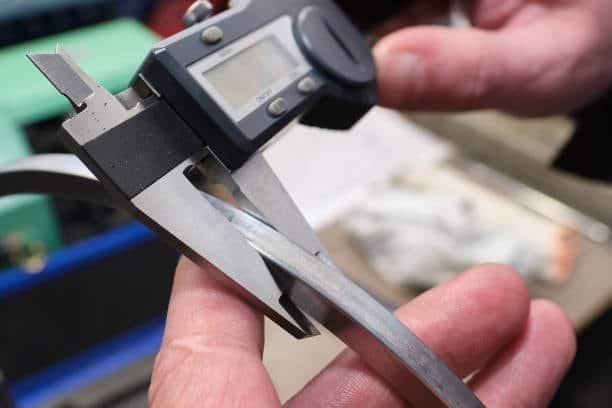
Tool radius compensation involves regulating the CNC machine’s programmed, so that it accommodates the radius of the cutting tool. The process comprises of two main elements: the tool radius as well as the offset value.
1. The Tool Radius
The tool radius is the length between the center of the cutting tool and the point of material cutting, known as the tool tip . Every cutting tool, whether it be a milling cutter or a drill or a lathe tool, has some radius which may hinder the ability of the process to work accurately. When anything is being cut with a tool, including tool nose radius compensation, the machine must take into consideration this radius and remove the proper material thus ensuring the end piece is as is designed.
2. The Offset Value
The offset value is the correction which corrects the programmed path of the machine through compensating. The offset is tabulated data from the tool circular radius and is put to either add or subtract the original program to make sure cutting tool path is appropriately positioned relative to part geometry. This can be done by changing the tool offset and tool path offset in the offset direction of the tool’s radius (increasing or decreasing) or programming of the CNC machine to take into account tool’s radius when machining part’s outline.
Types of Tool Radius Compensation
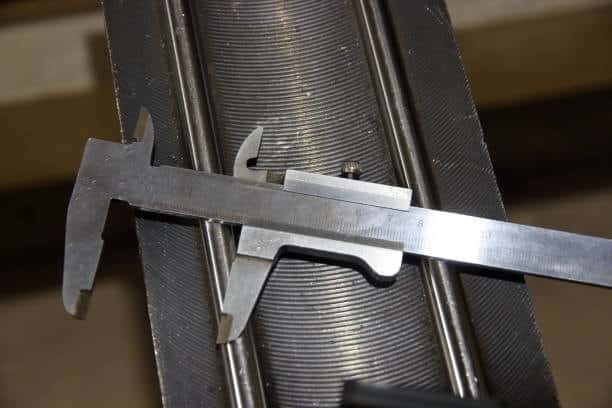
Two main types of tool radius compensation function are applied in CNC machining. G41 (compensation left) and G42 (compensation right). These codes move the CNC machine in a direction that it will adjust the tool path relative to the tool’s radius.
1. G41 – Tool Radius Compensation Left
The CNC machine will offset the tool path from the programmed contour to the left hand side when G41 is used. This is typically used when it is being used for particular operation, say milling the inside of a part or cutting on the left side of a contour, while G42 directs the tool to the right hand side . Such form of compensation guarantees that the tool will be able to keep the proper distance from the surface of the part, and thus a diameter of the tool will not result in the error concerning the dimension.
2. G42 – Tool Radius Compensation Right
Conversely, G42 directs the CNC machine to adjust the tool path to the right of the programmed contour. This compensation type is typically used when machining the outside of a part or performing operations where the tool needs to be positioned to the right of the programmed contour. G42 ensures that the tool moves in the correct direction to maintain dimensional accuracy.
Benefits of Tool Radius Compensation
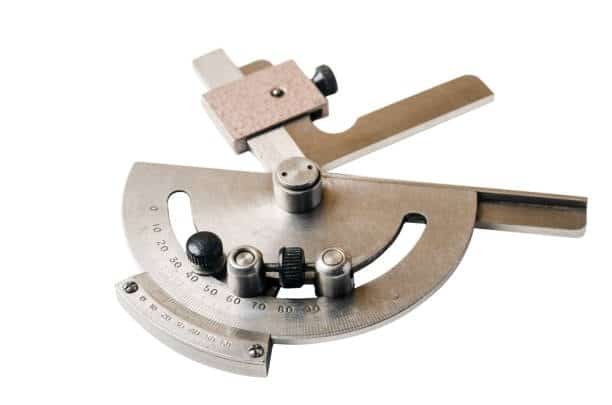
Many advantages are provided for CNC machining processes by tool radius compensation:
1. Increased Accuracy
The major benefit of tool radius compensation is accuracy. By using this method of offsetting the tool’s radius, CNC machines can also feed a part with close tolerances, thereby allowing the part to conform to specifications even if it is not perfectly centered.
2. Tool Wear Compensation
Tool radius compensation can also be used as a rehabilitation for tool wear. Using tools in machining processes cause them to wear over time. Tool radius compensation permits the operator to control the wear offset to the tool to ensure consistent part dimensioning throughout the life of the tool.
3. Enhanced Flexibility in Tool Selection
With tool radius compensation, manufacturers are more flexible in making the choice of cutting tools. The facility to account for varying tool size and radii makes it possible to apply a wider range of tools that would have required reshaping of the entire machining operation, thereby saving time and money.
4. Reduced Programming Errors
Without the tool radius compensation, the programmers would have to manually determine and calculate tool radius in programming the part geometry. This may be difficult and error-prone, especially when considering the input for complex part designs. Tool radius compensation automates the process to minimize probability of making programming errors, especially when dealing with g code, and to provide more consistency in production process.
Challenges in Tool Radius Compensation
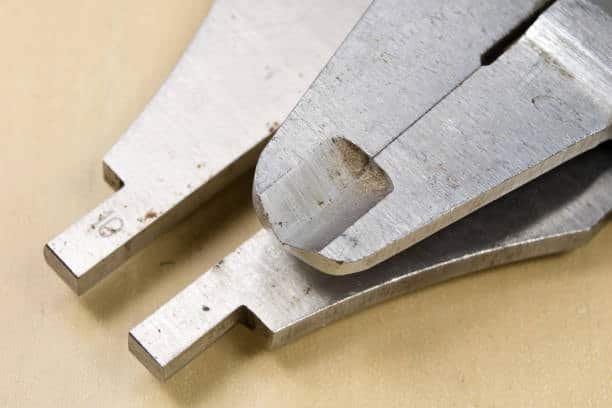
1. Complexity in Programming
Tool radius compensation complicates the programming process. CNC programmers need to know how tool radius affects part geometry and they need to enter the right offsets and conversion codes. Errors in this process will lead to incorrect part size and production delay.
2. Tool Path Accuracy
Accurate tool path adjustments need accurate calculations. If tool radius compensation is not implemented correctly, the tool will not follow the commanded path, and dimensional errors will be introduced in the end piece.
3. Machine Limitations
It is not the case that CNC machines are able to utilize tool radius compensation effectively. Older machines or those without representative CNC controls may have a limited radius of tool compensation that can be employed. Possible improvement of that machine or its software may be necessary to fully take this feature advantage.
Conclusion
Tool radius compensation is another important element of CNC machining where part production is maintained at highest precision and accuracy. By varying the machines tool path that will consider the radius of the tool and the arc radius , manufacturers will be able to prevent dimensional inaccuracies and manufacture parts that meet small tolerances. This technique is especially essential within industries, where accuracy plays a dominant role, such as aerospace, automotive and medical device industry.