Metal Injection Molding (MIM) has transformed the landscape of modern manufacturing, offering unprecedented capabilities for producing complex metal components with precision and efficiency. This advanced manufacturing process combines the versatility of plastic injection molding with the strength and durability of traditional metal components, making it an increasingly popular choice across multiple industries.
The Evolution of Metal Injection Molding
Metal Injection Molding emerged in the 1970s as manufacturers sought more efficient ways to produce small, complex metal parts. Traditional manufacturing methods often required multiple machining steps, resulting in material waste and increased production costs. MIM was developed as a solution to these challenges, offering a more streamlined approach to creating intricate metal components.
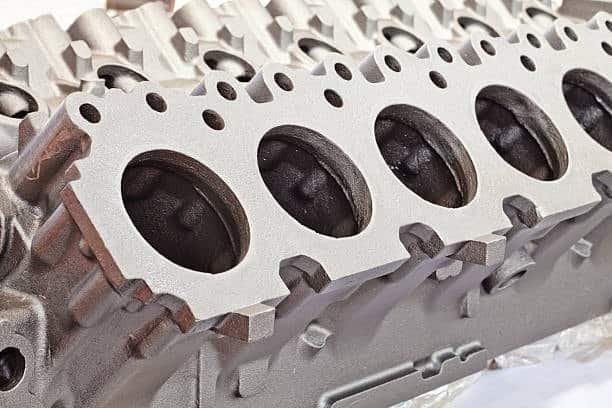
Since its inception, the technology has evolved significantly, with improvements in material formulations, processing techniques, and equipment design. Today, MIM stands as a cornerstone of modern manufacturing, particularly for industries requiring high-precision, high-volume metal components.
Understanding the Metal Injection Molding Process
The MIM process combines metallic powders with binder materials to create a feedstock that can be injected into molds, similar to plastic injection molding. The process, including the sintering process, encompasses several critical stages:
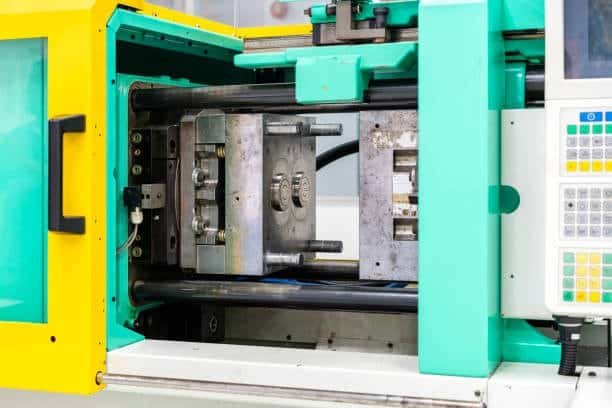
- Feedstock Preparation: Metal powders are mixed with polymer-based binders to create a homogeneous mixture suitable for injection molding.
- Injection Molding: The feedstock is heated and injected into a mold cavity under high pressure, taking the shape of the desired component.
- Debinding: The polymer binder is removed through thermal or chemical processes, leaving a fragile “green” part composed primarily of metal particles.
- Sintering: The component is heated in a controlled atmosphere furnace to temperatures below the melting point of the metal, causing the particles to fuse together while maintaining the part’s shape.
- Secondary Operations: Additional processes such as plating, heat treatment, or machining may be applied to achieve specific surface finishes or mechanical properties..
Key Advantages of Metal Injection Molding
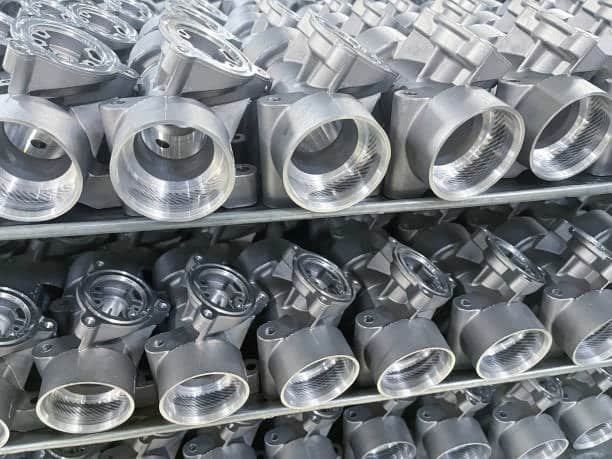
MIM offers numerous benefits that make it an attractive manufacturing option for complex metal components:
Design Freedom and Complexity
One of the most significant advantages of MIM is the ability to produce parts with complex geometries that would be difficult or impossible to achieve through traditional manufacturing methods. Intricate features, internal cavities, and thin walls can be created without the need for secondary machining operations for metal injection molded parts .
Material Versatility
MIM can be used with a wide range of metals and alloys, including:
- Stainless steels (304L, 316L, 17-4PH)
- Low alloy steels
- Tool steels
- Titanium and titanium alloys
- Cobalt-chrome alloys
- Tungsten alloys
- Copper and copper alloys
This versatility allows manufacturers to select materials based on specific performance requirements rather than machining limitations.
Cost-Effective Production
For medium to high-volume production runs, MIM can significantly reduce manufacturing costs compared to traditional machining or casting methods. The process minimizes material waste, reduces or eliminates the need for secondary operations, and allows for efficient batch processing.
Superior Surface Finish and Dimensional Accuracy
MIM parts typically exhibit excellent surface finishes directly from the molding process, often requiring minimal post-processing. The process also delivers tight dimensional tolerances, typically in the range of ±0.3% of the nominal dimension.
Industries Transformed by Metal Injection Molding
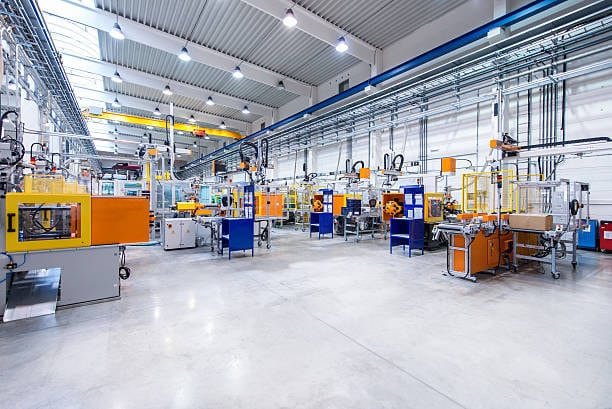
Medical and Dental Applications
The medical industry has embraced MIM for producing surgical instruments, orthopedic implants, and dental components. The biocompatibility of fine metal powders like stainless steel and titanium, combined with the ability to create complex shapes with precision, makes MIM ideal for these critical applications.
Automotive Components
Automotive manufacturers utilize MIM for producing various components including turbocharger vanes, sensor housings, fuel injector parts, and transmission components. The process allows for lightweight yet strong parts that contribute to improved fuel efficiency and performance.
Consumer Electronics
The consumer electronics industry benefits from MIM’s ability to produce small, precise metal components for smartphones, laptops, and wearable devices. These components often include hinges, frames, and internal structural elements that can be produced in multiple cavities and require both strength and aesthetic appeal.
Aerospace and Defense
In aerospace applications, MIM is used to create complex components for aircraft engines, control systems, and structural elements. The ability to work with high-performance alloys while maintaining tight tolerances makes MIM particularly valuable in this demanding sector.
Material Selection for Metal Injection Molding
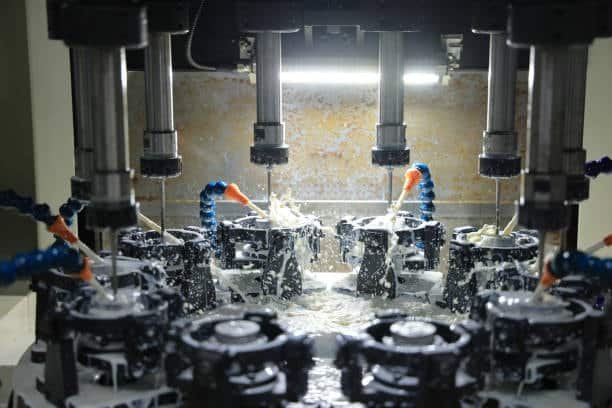
Selecting the appropriate material for a MIM application requires consideration of several factors, including the binder removal process :
Mechanical Properties
Different alloys offer varying levels of strength, hardness, ductility, and wear resistance. Engineers must select materials based on the specific mechanical requirements of the end application, whether that’s high tensile strength for structural components or wear resistance for moving parts.
Thermal Performance
Some applications require materials that can withstand extreme temperatures or thermal cycling. MIM can work with heat-resistant alloys that maintain their properties at elevated temperatures, making them suitable for combustion engine components or high-temperature industrial applications.
Corrosion Resistance
For applications exposed to harsh environments, corrosion-resistant alloys such as stainless steels or titanium may be selected finely powdered metal. These materials provide long-term durability even when exposed to moisture, chemicals, or biological fluids.
Optimizing Design for Metal Injection Molding
To maximize the benefits of MIM, product designers should consider several design principles:
Wall Thickness Considerations
Maintaining uniform wall thickness throughout a component helps ensure even shrinkage during sintering, reducing the risk of warping or distortion. Gradual transitions between different section thicknesses also help to account for any remaining binders and prevent defects catalytic process.
Draft Angles and Undercuts
Proper draft angles facilitate part ejection from the mold, while minimizing undercuts helps reduce tooling complexity and cost wrought materials. When undercuts are necessary, they should be designed to allow for simple mold construction using side-actions or inserts partial melting.
Part Size Limitations
While MIM is exceptionally capable for small to medium-sized components, very large parts may be impractical due to the challenges of maintaining dimensional stability during sintering. Most MIM parts typically weigh less than 100 grams, with dimensions rarely exceeding a few inches thermoplastic binder.
Quality Control in Metal Injection Molding
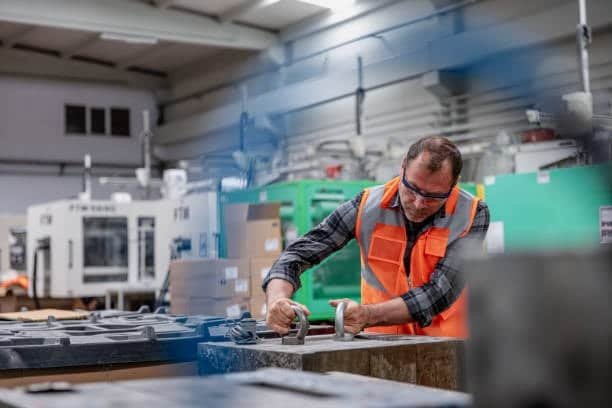
Ensuring consistent quality in MIM production requires rigorous process monitoring and testing internal and external threads:
Non-Destructive Testing
Techniques such as X-ray inspection and computed tomography allow manufacturers to inspect internal features and detect potential defects without damaging the components. These methods are particularly valuable for critical applications in medical or aerospace industries.
Mechanical Testing
Tensile testing, hardness testing, and fatigue testing help verify that finished components meet specified physical properties an mechanical properties. Statistical process control methods are often employed to monitor production consistency metal powder particles.
Sustainability Aspects of Metal Injection Molding
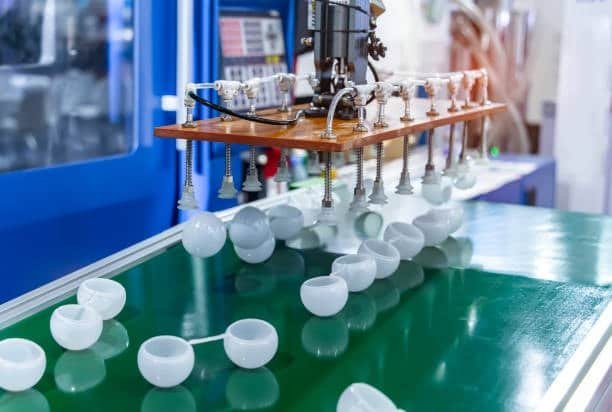
Material Efficiency
MIM is an inherently efficient process with minimal material waste. Unlike traditional machining, which may remove 70-90% of starting material as chips, powder injection molding techniques like MIM utilize nearly all of the input material to create the final part injection molding machine.
Energy Considerations
While sintering requires significant energy input, the overall energy efficiency of MIM can be superior to traditional manufacturing for complex parts that would otherwise require multiple energy-intensive machining operations.
Future Trends in Metal Injection Molding
Micro-MIM for Miniaturization
As devices continue to shrink, particularly in medical and electronics applications, micro-MIM techniques are being developed to produce extremely small components with micron-level features. These advances enable new possibilities in minimally invasive medical devices and compact electronic systems.
Multi-Material MIM
Research is ongoing into methods for creating components with multiple metals or metal-ceramic combinations in a single molding process. These developments could lead to parts with optimized properties in different regions, such as wear-resistant surfaces combined with ductile cores.
Comparing MIM with Alternative Manufacturing Methods
When evaluating manufacturing options, engineers must consider how MIM compares with alternatives like CNC machining, investment casting, or powder metallurgy:
MIM vs. CNC Machining
While CNC machining offers excellent precision and material flexibility, it becomes increasingly costly for complex geometries. MIM provides better economics for higher production volumes of complex parts, especially when internal features would be difficult to machine.
MIM vs. Investment Casting
Investment casting can produce similar geometries to MIM but typically with lower dimensional accuracy and surface finish. MIM generally delivers superior mechanical properties due to its higher density and more refined microstructure.
Conclusion
Metal Injection Molding represents a significant advancement in manufacturing technology, bridging the gap between the design freedom of plastic injection molding and the material properties of metals. As industries continue to demand smaller, more complex, and higher-performing components, MIM’s role in modern manufacturing will likely expand further.
The combination of design flexibility, material versatility, and cost-effectiveness positions MIM as an ideal solution for many challenging applications across medical, automotive, aerospace, and consumer electronics industries. Companies seeking competitive advantages in product development would do well to explore the possibilities offered by this innovative manufacturing process.