Introduction
Behind all modern industries stands plastic manufacturing as one of the most adaptable production methods ever invented, utilizing molten resin in various processes . Manufacturers use injection molding and compression molding as basic methods that differ in their properties and production benefits. The two production methods process plastic materials differently even though they make similar products. This article explains all areas that differentiate between injection molding and compression molding vs including their core productions and product matches.
The Fundamentals of Injection Molding
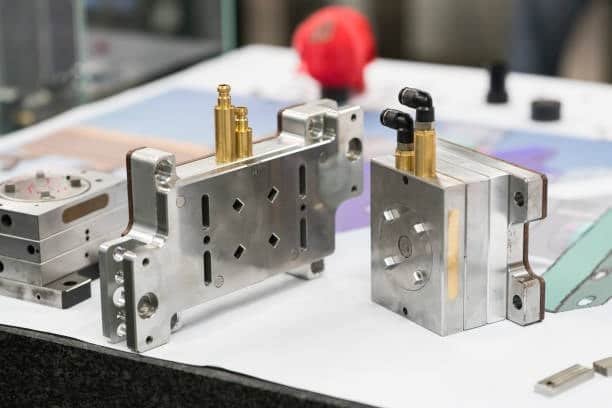
Injection molding works by melting plastic material under high pressure before letting it enter a sealed mold shape where it cools into its final product form. Despite being simple to understand, plastic injection molding has developed for many years into a major global manufacturing technique, especially using molten thermoplastic .
The Injection Molding Process
The manufacturing cycle opens by loading plastic pellets into a heated barrel. Inside the heating barrel, hydraulic rams work in conjunction with a plunger that moves back and forth to feed the material while a heating mechanism Slut melts the raw plastic. Once the required volume of molten plastic reaches the barrel end it receives immediate pressure to spill directly into the mold.
The mold cavity contains at least two pieces that create an empty space matching the specific item shape. The molding material stays under pressure after injecting to create matched pellets and can also be used to produce thin parts, despite its shrinkage during cooling. After the mold reaches proper temperature the mechanism opens to discharge the hardened molded item using ejector pins. Mold closure and part release processes combine in an overall period that stays within minutes of processing time except if the part requires more detailed work.
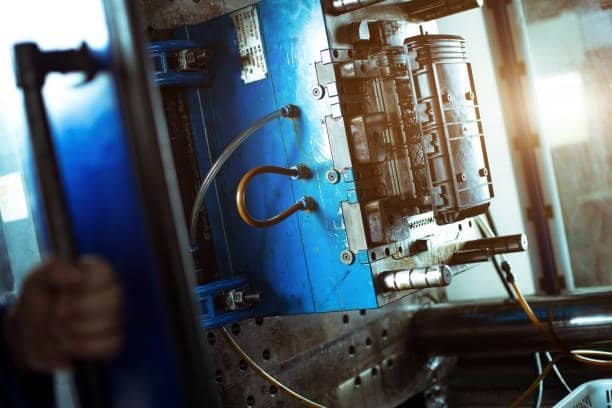
Key Equipment Components
Injection molding systems contain specific necessary pieces to operate properly, including single cavity molds for simpler production runs .
- The injection unit ensures material plasticization and injection.
- The clamping unit prevents the mold from opening under high injection pressure.
- The mold assembly unit creates the open space inside which melted plastic receives its shape
- Our control system oversees temperature pressure and timing settings that direct the whole production process.
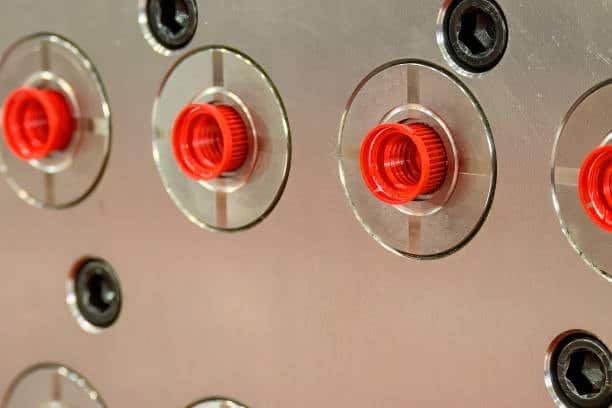
Current injection molding equipment includes advanced control systems that manage the process through closed-loop control systems with live monitoring, making the systems highly automated and statistical process control functions.
Materials Commonly Used
The injection molding process works with various materials, including varied thermoplastic materials such as rigid thermoplastics and plastic resin pellets like PE, PP, PS, ABS, Nylon, PC, PET, and TPE.
- Polyethylene (PE)
- Polypropylene (PP)
- Polystyrene (PS)
- Acrylonitrile Butadiene Styrene (ABS)
- Polyamides (Nylon)
- Polycarbonate (PC)
- Polyethylene Terephthalate (PET)
- Thermoplastic elastomers (TPE)
Specialized injection molding techniques can work with specific thermoset materials yet they are processed less often than thermoplastic materials.
The Fundamentals of Compression Molding
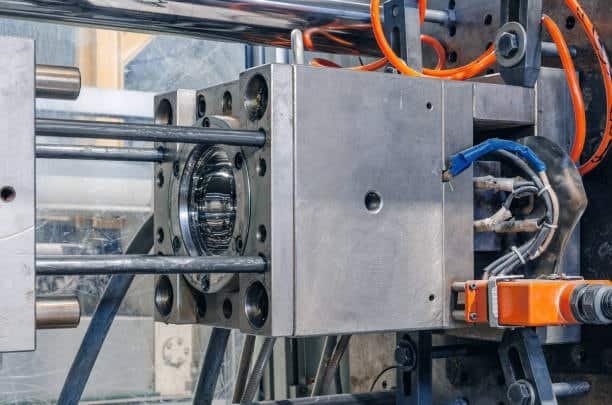
Although injection molding gains more use today the technique of compression molding remains important in its basic form for certain applications, comparing compression molding because of its early beginnings.
The Compression Molding Process
A technician places measured materials—powder or putty shaped chunks or sheet pieces—directly into an open mold for heating. The mold closes with strong pressure behind it which makes the material follow the mold shape two part mold. The material retains pressure and heat until it turns into its final set product state.
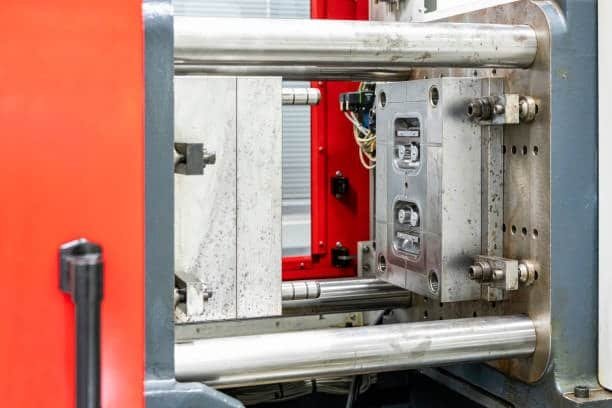
During thermoset material processing chemical crosslinking happens to set the material permanently. A thermoplastic material cools below its softening point and sets under ongoing pressure. After completion of curing or cooling the mold releases the finished part for removal.
Key Equipment Components
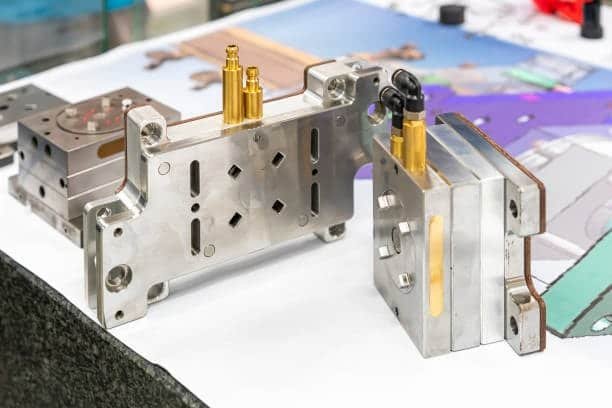
The basic parts of a compression molding system consist of:
- Hydraulic press: Provides the necessary closing force
- Heated platens: Rephrase the following sentence. Heated platen enables the supply of thermal energy used for material movement and bonding stages in the production process.
- Mold assembly: Forms the product shape
- Temperature control system: Maintains optimal processing temperatures
- Material handling equipment: The material handling system supplies material to and exports it from the production area.
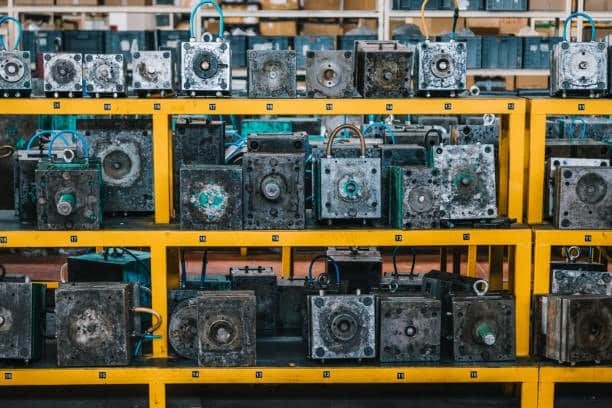
The controls needed for compression molding machines stay basic because their mechanisms remain simple compared to injection molding machinery, enabling easier adjustments of process parameters post processing .
Materials Commonly Used
Compression molding provides excellent processing results in the following areas:
- Products such as phenolics become firm duringñcompression as they solidify into thermosets alongside epoxy and silicon materials.
- Rubber compounds
- Sheet Molding Compounds (SMC)
- Bulk Molding Compounds (BMC)
- Fiber-reinforced plastics with high fiber content
- Engineering thermoplastics need minimal material shearing during production
Comparative Analysis: Injection vs. Compression Molding
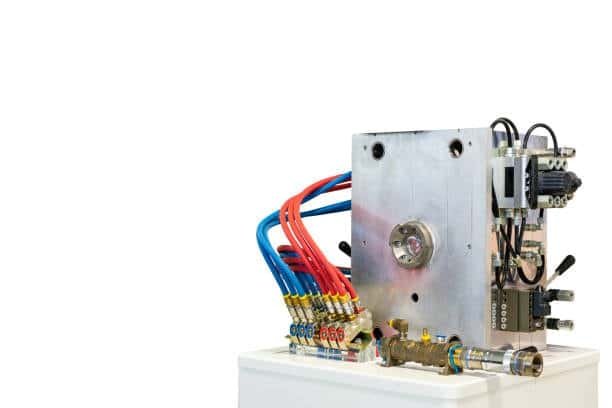
Manufacturers pick between injection and compression molding by weighing product and production requirements against each other, considering the advantages of compression molding other value added services.
Process Characteristics
Cycle Time: Injection molding completes production runs faster than all other methods but requires lower output volumes. Compression molding takes longer because setting up the right heating and curing times depends on the specific thermoset materials used.
Material Flow: During injection molding the material moves through thin runners and gates while enduring intense pressure and shear effects complex shapes. Thermal molding pushes materials outwards from the middle of the mold space without substantial shear pressure.
Pressure Requirements: Pressure during injection molding reaches from 10,000 to 30,000 psi while compression molding operates under lower pressures between 1,000 to 5,000 psi.
Temperature Profile: During injection molding the tool and barrel need constant temperature control to melt material into its correct viscosity. The whole mold surface receives equal heat during this process.
Product Characteristics
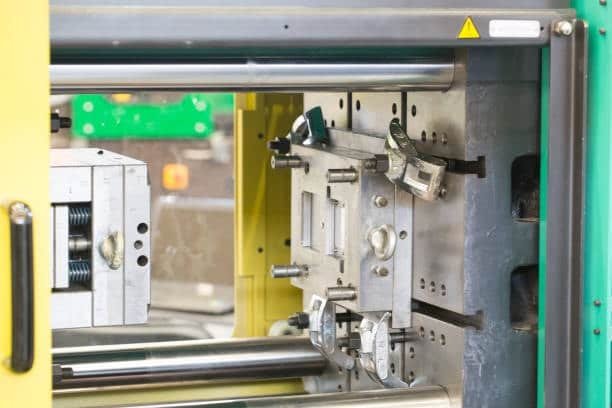
Surface Finish: The injection molding process makes parts look better and keeps more detailed features because of its strong pressure and complete material filling. Compression molding produces excellent flat-or-moderate surface quality without exact detail features, making it less suitable for parts requiring sharp edges .
Dimensional Accuracy: Injection molded parts show reliable dimensional precision through all production batches because their tolerances remain near 0.1 millimeters. Compression molding gives smaller than ideal dimensional ranges but meets most engineering needs.
Internal Stress: Parts made by compression molding generate lower internal tension than parts made through injection molding techniques. Lower processing forces and more even curing create these results raw materials.
Wall Thickness: The material changes easily to thin wall sections around 0.5-4mm in injection molding whereas compression molding tackles thicker parts without injection difficulties door panels.
Advantages and Limitations
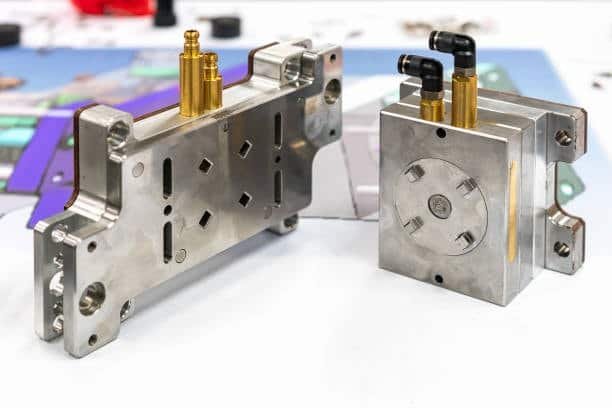
Injection Molding Advantages
- Production Efficiency: The system produces high-quality outputs at fast cycle times with light Human-touch operations.
- Design Flexibility: Innovation in tool design allows producers to make detailed parts with intricate shapes including threads and hidden features.
- Material Conservation: The equipment can control material amounts precisely while reusing unused plastic runners and sprues pliable materials.
- Automation Potential: The manufacturing process fits well with automated tools that handle parts, assemble them, and perform device inspections.
- Consistency: Modern process controls ensure high repeatability across production runs.
Injection Molding Limitations
- Initial Investment: A large amount of money needs to be spent on custom-made equipment and special molds before injection molding becomes economically practical.
- Design Constraints: The design of injection molds requires smooth even walls to stop molding issues with sunken areas and shape problems.
- Material Limitations: Plastics with high fiber content or many additives become hard to process because they resist flowing easily through the machine.
- Part Size Restrictions: The production of wide objects needs such costly equipment that it becomes impractical..
Compression Molding Advantages
- Fiber Integrity: During compression molding the method maintains the natural fiber pattern in reinforcing materials to boost performance effectiveness composite panels.
- Low Internal Stress: The parts show minimal in-built stress that helps them resist warpage while keeping their dimensional accuracy.
- Large Parts: Compression molding allows work with bigger parts than normal injection molding machines.
- Lower Tooling Costs: The needed mold pieces need simpler designs and cost less than injection molds.
- Material Versatility: The procedure allows processing materials that resist fluid movement and those with high filler content.
Compression Molding Limitations
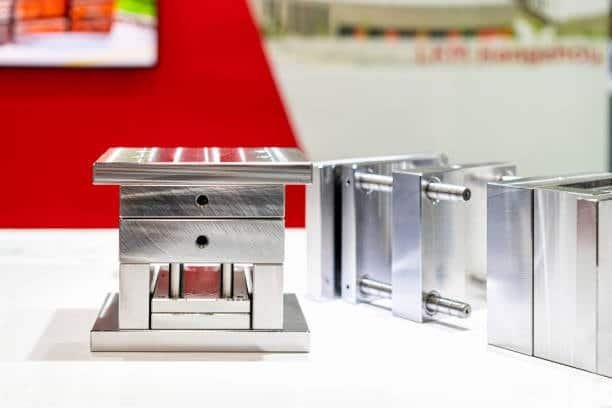
- Labor Intensity: Most compression moulding processing activities entail manual placement of materials to the moulding press and part extraction.
- Production Rate: The cycle time is long compared to injection molding and hence a slow production rate manufacturing capabilities.
- Geometrical Limitations: Complex internal features, undercuts or other even exceptional details cannot be attained easily or at all injection machine.
- Flash and Trimming: The process usually generates trimmings or flash which are found at the parting lines and requires removal closed mold cavity.
Applications and Industries
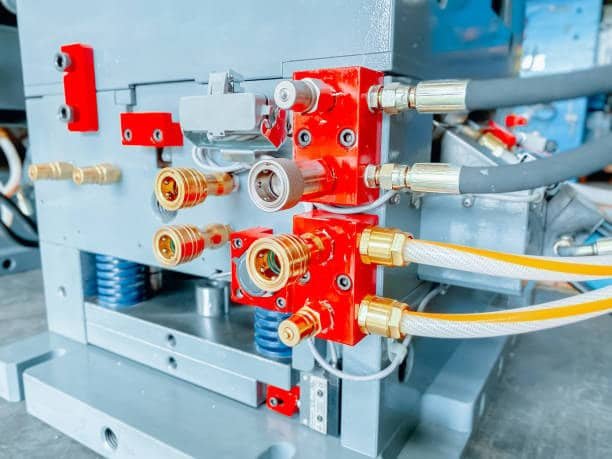
Ideal Applications for Injection Molding
Injection molding excels in producing:
- Small to medium-sized consumer products
- High-precision components with complex geometries
- Products of certain classes that need high quality of millions of parts
- This genealogy of form creation includes products that contain integral features such as snap-fits as well as living hinges.
- It is done through processes such as over-molding
Hence, key industries that utilize the injection molding method are:
- Automotive (interior components, electrical connectors)
- Consumer electronics (housings, buttons, connectors)
- Medical devices (surgical tools, drug delivery systems)
- Packaging (containers, caps, closures)
- Household goods (kitchenware, storage containers)
Ideal Applications for Compression Molding
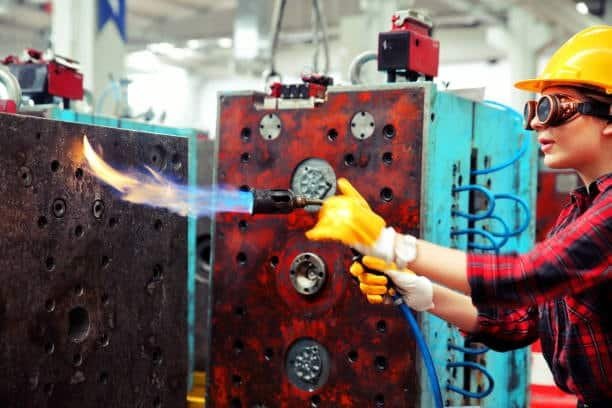
It indicates how compression molding fits into producing items like reinforced panels :
- Large structural components
- Highly reinforced composite parts
- Electrical insulators and switchgear components
- Heat-resistant components
- High-strength mechanical parts
Common uses of compression molded components are as follows, particularly in applications that require large volumes.
- Automotive (body panels, under-hood components)
- Aerospace (interior panels, structural elements)
- Electrical (circuit breakers, insulators)
- Construction (architectural elements, panels)
- Industrial equipment (gears, bearings, structural components)
Economic Considerations
Decisions taken in manufacturing essentially depend on economic factors as those that define the total manufacturing costs and profitability.
Cost Structure Comparison
Injection Molding:
- High initial mold cost ($10,000-$100,000+)
- Expensive equipment ($50,000-$500,000+)
- Low per-part labor cost
- Low material waste (typically 2-5%)
- Economical for high volumes (typically >10,000 parts)
- That is why setting finishing costs low when properly designed
Compression Molding:
- Moderate mold cost ($5,000-$50,000)
- Less expensive equipment ($30,000-$200,000)
- Higher per-part labor cost
- Moderate material waste (typically 5-15%)
- Economical for low to medium volumes
- Higher finishing costs due to flash removal
Break-Even Analysis
There is a definite relationship between these two processes which is determined by the production capacity as follows. For small production quantity ranging between several hundred to few thousands parts, compression moulding is often the most cost effective one in terms of mold pricing factors, because of low tooling cost and the use of bulk material vehicle panels . While the number of parts produced ranges from tens to hundreds of thousands, injection molding becomes more cost-effective to produce rigid composite components by per part and has more efficiency than other methods of molding, often completing production runs in a few minutes complex parts.
Sustainability and Environmental Impact
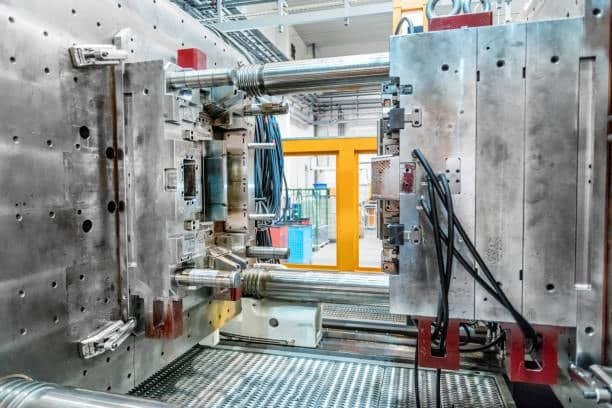
It shows how decisions of today’s manufacturing companies are no longer only made based on cost and time mainly but with an environmental impact factor as well.
Energy Consumption
Injection molding operation consumes more energy since most of the processes need to be carried out at high heat and pressure. Yet, in the case of higher volume production, it is seen that faster cycle times considerably decrease energy use by part large plastic car bumpers. Compression molding is a low pressure process but may take longer melting time especially in the thermoset category of materials, unlike flexible elastomers .
Material Efficiency
Common forms of manufacturing waste in injection molding are the runners and sprues but these are normally recycled using for thermoplastic uses materials tend. Whilst compression molding creates flash that more often is not reusable, this is mainly when working with thermoset material.
End-of-Life Considerations
The products produced with the help of injection molding with thermoplastics are mostly suited for recycling at the end of the product’s life cycle. Some of the thermoset products based on compression molding are harder to recycle, especially when compared to plastic parts; however, new technologies for the reclamation of these products are being developed alongside other processes compression molded parts.
Recent Technological Advances
Both manufacturing methods remain innovative to the current development and technology in improving their abilities and covering some of the past setbacks that were recorded excess material.
Advances in Injection Molding
- All-Electric Machines: Boilers and hydraulic fluids give marker to more energy-efficient servo-electric drives.
- Micromolding: High level of detail is attainable through the tools used in the molding of micro devices for the medical and electronics industries.
- Gas-Assisted Molding: Nitrogen is injected into the thick section to form non-load bearing voids which help also to decrease material usage and cycle time.
- Conformal Cooling: Integrated cooling system constructions where cooling channels are such that they form part of the mould shape result in better cooling and reduced cycle time flexible materials.
- Industry 4.0 Integration: The current machines are equipped with profound sensing mechanisms and data capture system, predictive maintenance is also an integral feature of the machines heated mold.
Advances in Compression Molding
- Automated Material Handling: Proper placement of materials involves the use of robots which reduces the cost of hiring workers and ensures uniformity.
- Rapid Heating/Cooling Systems: Vario thermal processual decreases the cycle time since it allows for fast changing of the mold temperatures during different phases of the process.
- Compression-Injection Hybrid Processes: the two ways of producing Polyurethane foams is through Compression and injection processes and new developments of the two involve incorporating aspects of each in the production.
- Advanced Material Systems: Reduction of traditional cycle time disadvantage by developing new fast curing thermosets as well as sheet molding compounds injection molding compared.
- Computer Simulation: Flow and curing simulation software enables the process to be predicted by the computer and also helps to improve the quality of the part produced very high pressure.
Conclusion
For this reason, injection and compression molding technologies will continue to be relevant in the growing manufacturing industry given that each has its unique advantages are suitable for different applications. Based on the identified trends, further expansion could concentrate on the enhancement of the sustainability aspect of the existing processes, the application of the combined approaches, as well as the integration of the automating technologies into both methods. Understanding the relative strengths and weaknesses of each procedure will enable such manufacturers to make wise choices regarding the best value to be derived from the several critical measures of performance, cost, and environmental impact tailored to their applications involving the desired shape .
This paper will demonstrate that for many applications the difference between injection and compression molding are not between two technologies which are positive and negative but what is better for specific application. If these factors are effectively analyzed and willingness towards changes with the advancement in technology is shown then there is no reason why these time-honored approaches cannot assist the manufactures in catering to the requirements in today’s world which is far more challenging and more conscious of the environment than ever before.