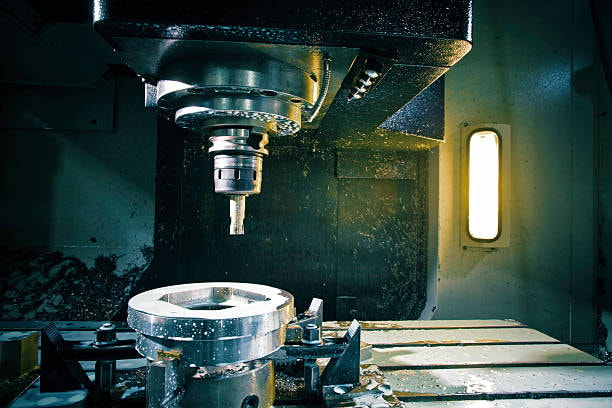
Find out the critical variations between milling and drilling in terms of manufacturing. Find out more about CNC machine applications, selection of tools, accuracy and cost factors to achieve best machining operations.
The choice of the right machining applications to use is vital in the manufacturing excellence, especially as drilling focuses on precision . Mill and drill are some of the most basic techniques of machining that form the basis of contemporary manufacturing in all industries, especially for round holes . Knowledge of all these differences can help manufacturers make wise decisions that can increase productivity of the manufacturing processes, lower costs and attain high quality results in the manufacturing processes.
Technological advancements make the manufacturing environment develop further, so it is essential that professionals understand the specifics of various machine-related approaches. Milling and drilling are both important in the processes of material removal but have their own advantages in line with the application demands. The following reference guide will present the general differences, their application and factors that go into the decision making process of selecting either of the two very important manufacturing processes.
Understanding the Fundamentals of CNC Drilling Operations
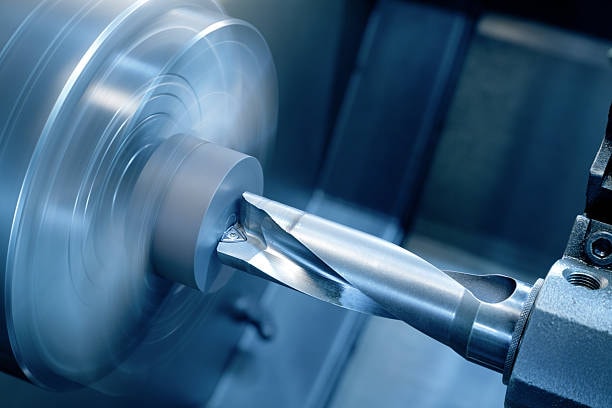
Drilling is one of the simplest machining processes that occur in manufacturing and is concentrated on drilling exact holes of the cylindrical shape in the workpieces. The most important distinction between milling and drilling is in the way of material removal. Drilling involves the drilling of cylindrical holes with the help of a rotating drill bit, thus, is a very critical technique in a number of applications in manufacturing.
The drilling is done in a linear process of penetration as applicable with the drill bit which rotates in a linear motion usually straight into upward downward direction into the work piece. This is a process that should be done with caution since the selection of drill bit, speed of spindle, feed and the use of coolants will make a difference in the outcome of the process, particularly when working on a flat surface . This is because the ease of drilling makes it very effective when it comes to generation of holes of the same diameters and depths.
The field of modern drilling has gone through a lot of transformation as a result of computer numerical control (CNC). The new CNC drilling systems have higher precision, repeatability and automation options not provided by the old method of manual drilling. They are able to follow complicated drilling pattern, achieve close tolerances and operate with minimum human assistance.
Drilling operations are subject to successful drilling operations whose effectiveness is dependent on selection and establishment of proper tools and machine configuration. Various materials call different geometries of drill bits, coatings, and cutting parameters to work best. Due to this fact, it is vital to understand these requirements to be able to maintain tool life, acquire desired surface finishes, reduce waste material, as well as reduce production cost.
Exploring Drilling machines Capabilities and Operations
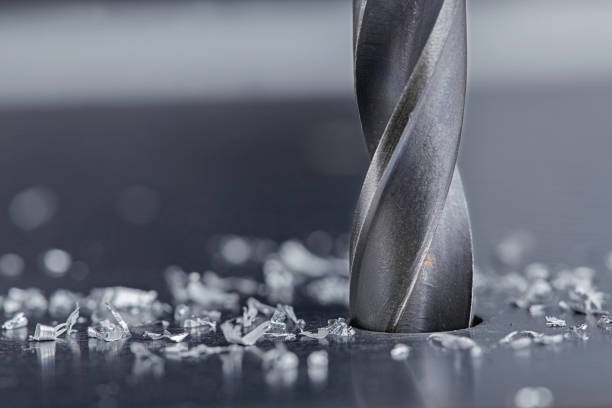
Milling is another more general type of machining process that can be used to remove material by rotating multiple-tool cutting devices touching the surface of the workpiece. Drilling moves up and down to cut the material whereas milling moves laterally, allowing complex shape to be made as well as multiple operations, profiles and surface texts that cannot be made with drilling.
The milling operation provides outstanding removability flexibility, the possibility to elaborate notches, recesses, contours, and three-dimensional shapes. Such flexibility has made millings unassailable when it comes to making parts that need to be highly accurate in their dimensions as well as forms, especially using milling cutters . It is a major addition to the variability of the operations, given that one can come at the work piece on a variety of angles and directions.
CNC milling machines use complex control systems that ensure that a set of cutting tools move with various directions and axes at the same time. This multi-axis provision allows production of highly complex parts with limited changes in set up and handling. The machining technology advanced milling centers enable to complete a variety of operations in the single arrangement and is efficient and provides a high precision of positions.
Precision in the selection of milling parameters needs close consideration of factors such as the geometry of the cutting tool, the speed of the cutting tool spindle speed and feed rate, the depth of cut, and cutting fluids. These parameters need optimization of concrete material characteristics and the results aimed at reaching high productivity without compromising on quality, especially for any drilling project .
Key Technical Differences Between Milling and Drilling
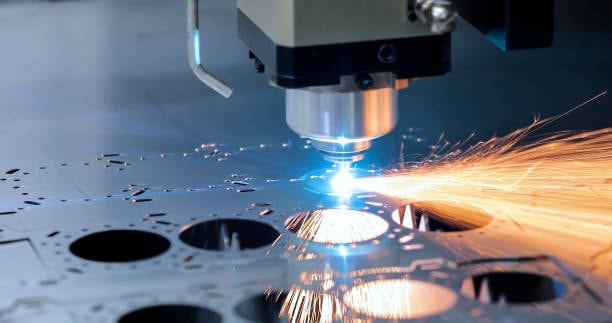
The basic difference between milling and drilling is the mechanics of operations and material removal system. The milling cutting tool works in that the horizontal and vertical constitution of movement is moved during the operation hence more versatile and more complex shapes. Completely the opposite, attachments are to operate mainly in the vertical direction of movements, showing the low directional ability of drilling applications.
In drilling, the single-point cutting tools are normally used to establish the cylindrical holes by linearly penetrating the work piece. The drilling tip is rotated as it pushes toward the material in an axial direction, producing chips, which have to be removed through the flutes of the tool. The process is very effective in hole-making processes, but is geometry challenged.
Milling processes use multi-point cutting tool which involves cutting the workpiece at a different angle and different positions. The tool functions as a cutting tool that rotates on a non radial path and travels laterally across the work piece, recessing off material in successive layers to give the desired shape. This process allows creating complex shapes, such as angular surfaces, curved profile, and detail shapes.
Differences in the tool engagements between the two processes lead to variations in the cutting forces, vibration profile and heating nature. It is important to know these differences so as to apply right tooling, workholding systems and machining parameters to maximize performance and tool life.
Speed and Feed Rate Considerations
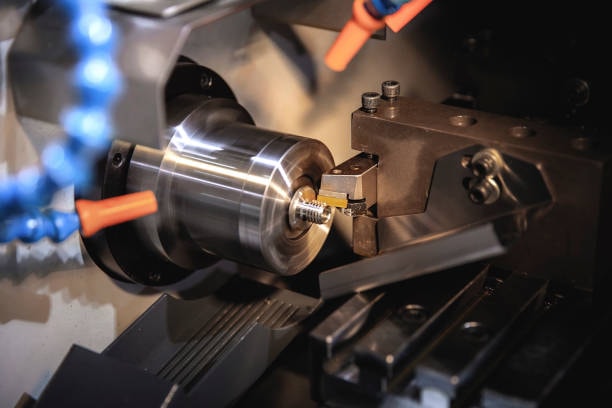
The milling and drilling operations use different operational parameters because the process of material removal and tool engagement process are unique in both cases. Speed is the biggest distinction between drilling and milling. With drills a slow spindle speed is required since there are only a few cutting edges on them but with Milling higher spindle speed is needed so that there is good cutting action on the many cutting edges.
Tool wear and generation of excessive heat are factors that require drilling operations to run typically at lower spindle speeds. The constant interaction of the drill bit to the drilled material needs to be properly controlled thermally in order to preserve the quality and life of the tool. During drilling, the feeds should always be balanced to form acceptable chips without causing a breakage of the tools or inadequate surface finish.
The intermittent nature of cutting by the multi-point tools allows milling operation to handle greater spindle speeds. The continuous movement on and off of the cutting edges permits the dissipation of more heat and also permits a faster rate of removal of more material. But the best speed and feed is a factor of material, tool geometries and surface finish wanted.
There are several important factors to account when choosing the right cutting parameters, including tool manufacturer recommendations, material features and capabilities of the machine. Advances in CNC systems have lead to the inclusion of an adaptive control to continually change parameters depending on real-time feedback in an attempt to maximize system performance and ensure constant quality.
Precision and Accuracy Requirements cnc milling
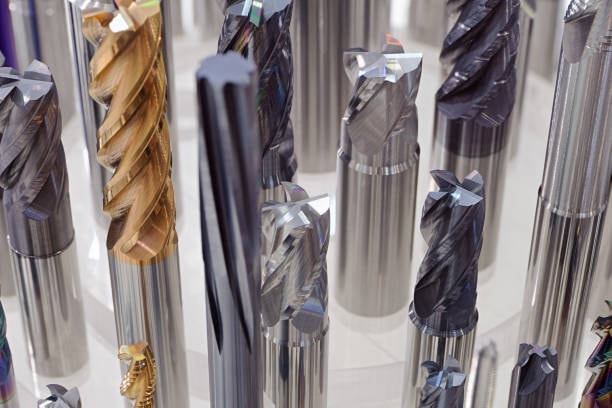
Both milling and drilling may have high precision when done right, but depending on the machining process, one or more characteristics of the accuracy are different. The main difference in the precision level created in the work piece by drilling is the intended hole but in the case of milling, scope is much broader and includes potential volumes and complicated geometries, this means that precision needs of the one process or the other are different and so does the measurement approach.
To drill well is mainly focused on the hole location, case, and straightness. State-of-the-art CNC drilling machines are able to provide position accuracies in the range of micrometers and consistency of diameter in a high volume production of precise holes. Tight tolerances needed by crucial applications can be achieved by precision tooling, large machine structures, and proper cutting parameters.
Milling precision has several dimensions such as positional accuracy, surface finish, geometric tolerances and relationships between feature. New techniques of measuring and verifying, aided by advanced technology, used in the multi-axis environment of milling should provide a high level of innovation to make sure every single specification is satisfied. Milling accuracy is typically checked using coordinate measuring machines, and in-process measurement systems.
High precision in the two processes is achieved depending on the machine rigidity, thermal stability, quality of tools and process control. The environmental effects (temperature change and vibrations) may greatly affect the precision results and should be controlled with special attention in a critical application.
Tool Selection and Material Considerations for cnc drilling processes
Proper choice of cutting tools is one of the determining factors in the effectiveness of the milling as well as the drilling process. To realize the best performance in tool selection, consideration should be based on material characteristics, geometry, the volume of production and cost limitation, including the use of end mill . Their divergences in required cutting tools are explained by the differences in the features of their operations and process of removing the substrate.
Relative in simplicity in designs, drilling tools mainly comprise twist drills, center drills, and customized hole making tools. The selection criteria is based on material of drill bits, coating, geometry of the points and design of the flutes. The performance characteristics of high- speed steel, carbide and coated tools are diverse to comply with the different materials and applications.
A large variety of geometries of milling tools are available such as endmill, face-mill, ball-mill, and specialty cutters. Factors to be taken into account during the process of selection include the number of cutting edges, helix angle, cutting edge geometry as well as tool coating. Milling operations are versatile and hence there must be extensive knowledge in tool capabilities and constraints.
In the two processes, material aspects are very important in the choice of tools. Some materials might need special cutting parameters and tools geometries to be used on hard materials and some might need sharp cutting edges and suitable chip escape techniques when cutting soft materials. Because of this, knowing the material machinability is a must have in order to attain the best results.
Cost Analysis and Economic Factors
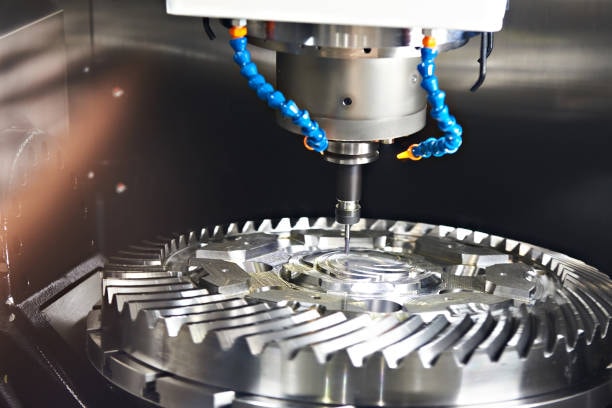
Economic factors in the milling and drilling operations include several factors such as expenses on equipment, toolings costs, setting up time, and the length of a cycle and the number of forced labor. The knowledge of such cost drivers permits decisions to be made by manufacturers that take into account what will be most profitable but still allows the retention of quality standards.
Drilling operations also usually do not need very complicated equipment and can be set up faster with fewer demands, therefore, it costs less to initially invest in this type of operations and operating costs as well. The hole-making operations tend to be simple and thus the resulting cycle times tend to be shorter and the programming requirement lower. Nevertheless, narrow drilling flexibility might mean that complicated parts have to be performed in several preparations or various processes, often resulting in repetitive tasks .
The equipment costs are usually more in milling operations as the multi-axis machines and control are complex. Milling can be multifunctional and thus, the number of operations needed to make a part might be fewer and this can justify the increased per hour operating costs, especially when using multiple axes . The capacity of running several operations on a single set up may greatly cut down the costs of handling and set ups.
To economically optimize both processes, total production costs namely; direct cost/labor cost and materials cost and indirect cost/overhead cost and quality control cost shall be given great consideration in analyzing. With the help of the activity based costing means, it was possible to capture the actual drivers of the costs as also to compare costs in a better manner.
Applications Across Different Industries
Milling and drilling processes have been applied in almost all manufacturing industries and various industries, each process has its special applications depending on required conditions and limitations. Knowledge of application to the industry enables the manufacturers to identify the best process to use that fits their needs and that of the market they are dealing with.
The two processes are important to aerospace manufacturing of tight-tolerance components and components requiring excellent surface finishes. Drilling plays a vital role in making bolt holes, assembly features, rivet holes etc in air craft structures. The milling processes are being used in complex airfoil shapes, structural parts, high accuracy precision fittings wherein it is necessary to have extraordinary precision and surface finish.
Large drilling is also involved in the automotive manufacturing like drilling on engine blocks, transmission housings and body panel assembly. The precision parts produced in milling operations are used in engines, precision molds and complex shapes and it demands detailed shapes and tolerances. Intensity of automotive manufacturing requires optimized processes that are in balance between quality and productivity.
Both processes are necessary in manufacturing medical devices in order to make implants, surgical instruments, and diagnostic devices. This industry has special tooling, processes and special quality controls requirements because of biocompatibility and regulatory demands within the industry, particularly regarding hole drilling . Both drilling and milling need to utilize outstanding surface results and sharp edges with strict dimensional tolerance in serious medical works rotating cutting tool.
Quality Control and Inspection Methods
The control of quality is an important item in the milling and drilling so a thorough inspection procedure and measuring techniques are needed to maintain the quality of the product to the specifications. Effective quality control strategies should be developed with the help of taking into account individual peculiarities of each process and possible failure modes cnc drilling operations.
Hole diameter, position, straightness, hole depth and surface finish have been deemed as the most important aspects of the drilling that should be regulated. Optical comparators and coordinate measuring machines, and special hole gauges allow the critical dimensions to be measured. Strategy statistically controls the processes to help them establish trends and avoid quality problems before they can attain major problems drilling holes.
Automation and CNC Integration (cnc drilling)
Milling With the introduction of computer numerical control technology, milling and drilling have taken a new turn and offered new foundations of precision, repeatability and automation. Becoming aware of the possibilities and the imperfections of CNC systems, specifically the cnc drilling processes, is a key characteristic of effectively exploiting the capacities of such advanced manufacturing systems creating precise holes.
The CNC drilling machines have the ability to control positioning accuracy, automatic tool shifting, and advanced hole-making programs that produce the best productivity and quality create holes. Another subtractive manufacturing process that is a subcategory of machining is CNC drilling which has the objective of machining shape in form of holes in the work piece based on the CAD design uploaded, thereby allows direct design responsibility transfer to the actual manufacturing process hole creation.
Future Trends and Technology Developments
Technological advancement has progressed to the manufacturing industry that affects both milling and drilling activities. The knowledge about trends and technologies will enable the manufacturers to anticipate the challenges and manage opportunities in a more competitive market mass production.
The ideologies of Industry 4.0 are being incorporated into machining processes using the deployment of smart sensors, data analytics, and connectivity titanium alloys. Such technologies make it possible to perform predictive maintenance, effectively plan the process, and improve quality, thus increasing total equipment effectiveness and total cost of ownership.
The cutting tools are broadening the frontiers of the milling and drilling capabilities which are achieved by the use of advanced materials and coating technologies. Advanced carbide grades material waste, nanostructured coatings, and new styles of tool are allowing more economical cutting through higher speeds, longer tool life and better surface finishes to more materials.
In a bid to die with fear of the new, additive manufacturing processes are starting to replace the old subtractive processes with hybrid manufacturing techniques, fusing the powers of both manufacturing processes multi axis movement. The given integration presents new options of part design and manufacturing strategy that previously have been impractical or even impossible.
Environmental Considerations and Sustainability
Environmental awareness is on the rise as far as manufacturing activity is concerned, which translates into the emergence of more environmentally sound milling and drilling methods. The responsible manufacturing activities should know about the environment effects and adopt proper methods to reduce them stationary workpiece.
One important environmental factor in the two processes is cutting fluid management tool paths. Proper choice of eco-friendly coolants, recycling systems and minimum quantity lubrication techniques would thus considerably decrease the stress on the surrounding without adversely affect the processes.
Optimization of energy by better machine efficiency, process engineering, and shortened cycle times also build towards sustainability objectives at the same time lower the operating costs. Substantial savings can be accomplished through the choice of energy-efficient equipment and introduction of intelligent power managing systems construction industry.
Environmental reduction: There are other ways that encourage waste reductions like having tool life optimum, minimized scraps, and recycling of materials drill press. The application of the concepts of lean manufacturing can help recognize the sources of wastes and do away with it across the production process how does cnc.
Conclusion
When choosing between the two processes milling and drilling, various considerations have to be made depending on the various factors such as the geometry of the part to be manufactured, precision demands, the scale of production and cost limits. Both processes are critical in the contemporary manufacturing whereby each has its own benefit in certain applications. The key to successful implementation of each process is the knowledge of its capabilities and limitations, the choice of the tooling and the parameters, and quality controls. Since the manufacturing keeps updating with the pace of technical innovations, the tactical utilization of such drilling and milling operations will be a core unit of gaining competitive differences on the global frontier.