Introduction to Injection Molding Molds
One of the most versatile and efficient manufacturing processes, known as plastic injection, to produce plastic components in scale is Injection Molding, which is essential for understanding injection molding cost . The injection mold, however, is at the heart of this process, as it is considered the foundation of quality plastic production. These tools are very sophisticated but need a large upfront investment to manufacture and they allow manufacturers to manufacture consistent high quality parts with little human intervention. These essential manufacturing tools still have cost structures that are a critical consideration for product developers, manufacturing engineers, and procurement specialists.
The Anatomy of an Injection Mold
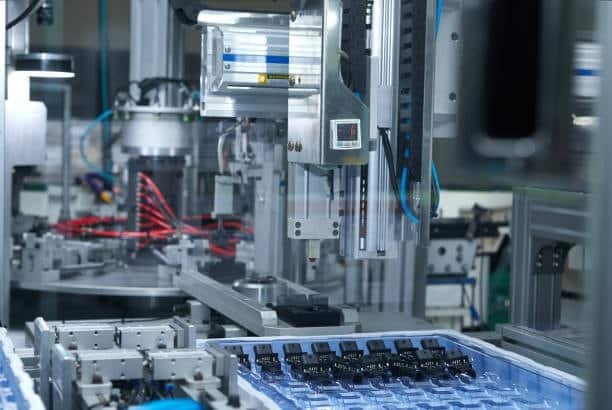
There are numerous sophisticated parts within an injection mold that need to work together in the injection molding process to create accurate plastic parts. Basic mold design consists of two principal areas where the process of making molds begins. most basic mold consists of two principal areas: clearly, cavity side, generally locked to the stationery platen and, obviously, core side, fixed to the moving platen. In each of these sections, a myriad of precision machined components react to very specific tools during the production cycle. Knowing these components gives a clear reason why molds are much of the investment of the production process.
Essential Mold Components and Their Cost Impact
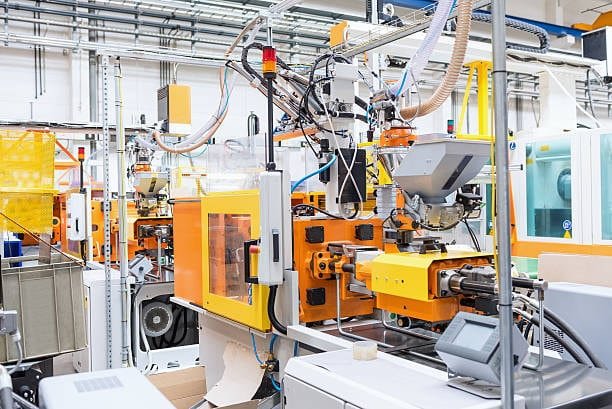
There are several important elements in every injection mold which have an effect on the plastic injection molding costs.
- Core and Cavity: The Host of the forming surfaces, that form the part’s shape.
- Ejector System: The ejector system was composed out of pins, sleeves, and plates that unload the finished part.
- Cooling Channels:Pathways in which temperature regulating fluid has been running during the cooling process.
- Runner System: Channels to direct molten plastic to the cavity (so called Runner System).
- Gates: A precise way to enter the part cavity
- Vents: Small openings that allow air to escape.
- Parting Line: Where the mold halves come together, termed as parting line
- Support Pillars: Structural components maintaining alignment are support pillars.
- Mold Base: Includes all housed Mold Base, it is the foundation housing all components.
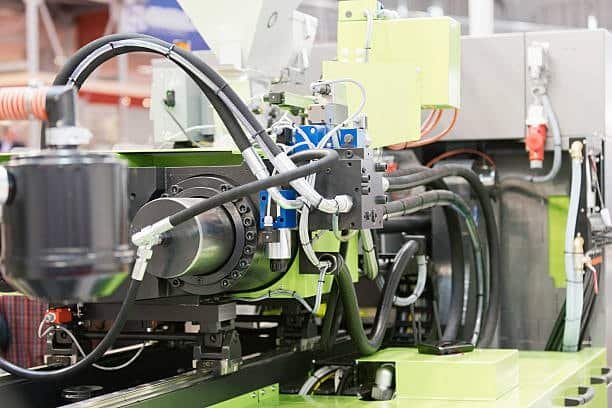
Precision engineering and fabrication of injection molded parts and each of these elements further adds to the overall cost of a mold incrementally.
Mold Classification Systems
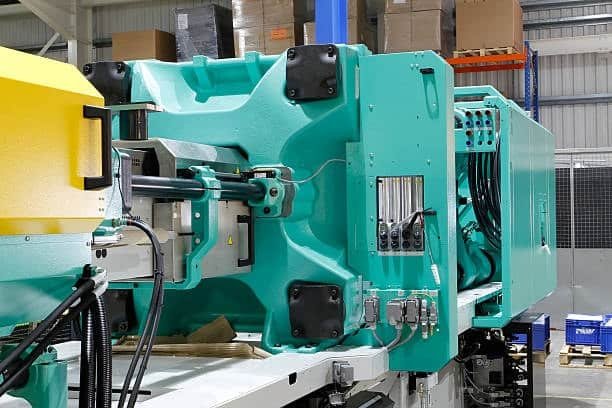
There are several classification systems as regards mold design of injection molds, which affect their cost structure.
By Construction Type
- Two-Plate Molds: The simplest design with a single parting line
- Three-Plate Molds: Additional parting line between the runner system in Three-Plate molds.
- Hot Runner Molds: Keep Plastic in a molten state between shots at a Hot Runner Mold
- Insulated Runner Molds: the Insulated Runner Molds where runners are fabricated as a part of the mold.
By Production Capability
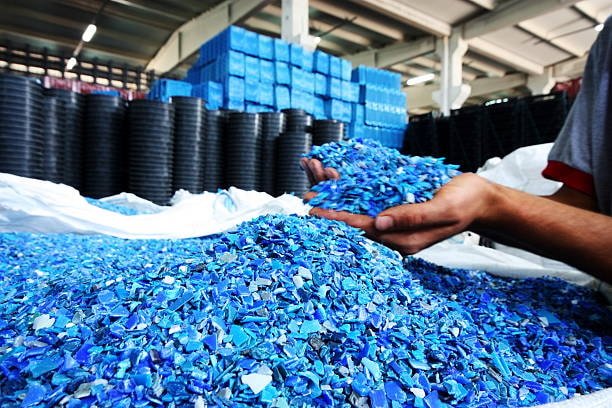
- Prototype Molds: Low-volume production or concept validation
- Bridge Tooling: Medium volume transitional production if bridge tooling is used.
- Production Molds :High-volume manufacturing with maximum durability
- Ultra-Production Molds: Extended lifecycle for millions of parts
Part Complexity as a Cost Driver
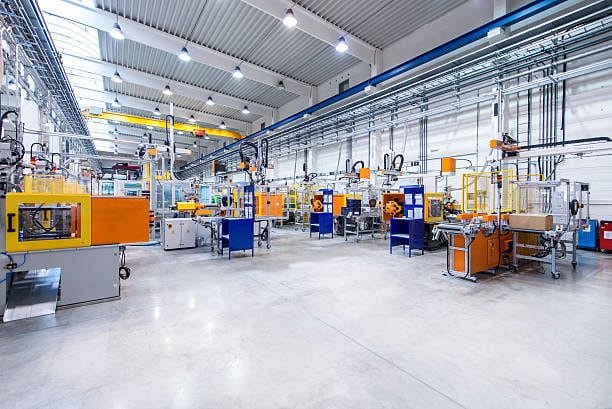
Mold cost is greatly affected by the complexity of the designed part. However, when complex geometries are required, more sophisticated tooling solutions that involve multiple cavities and often require more material re necessary such as:
Geometric Complexity Factors
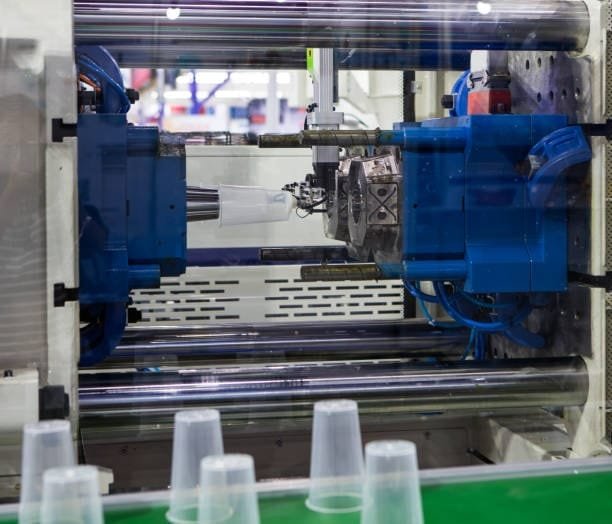
- Undercuts: Slides, lifters and collapsible cores are required (undercuts)
- Thin Walls: Necessitating advanced cooling and flow analysis
- Deep Ribs: extended cores, enhanced cooling.
- Complex Parting Lines: One requirement that necessitates precise machining and fitting is complex Parting Lines.
- Internal Threads: Often need unscrewing mechanisms.
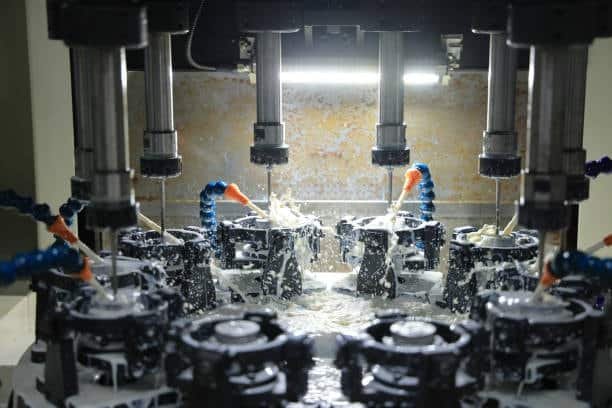
In the case of a simple box shaped part you would only need a for simple molds, which can start at tens of thousands for more complex designs. but for complex molds like an electronic housing with many undercuts this would call for advanced injection mold tooling in excess of $100,000 for the additional mechanical systems.
Dimensional Considerations in Mold Costing
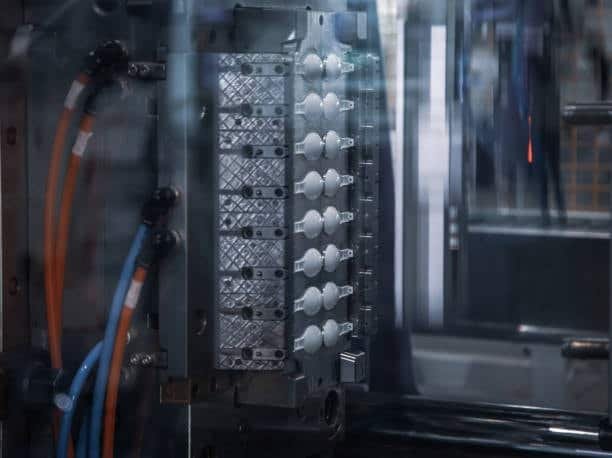
There are multiple reasons why the physical size of injection mold tooling determines the cost.
Size-Related Cost Factors
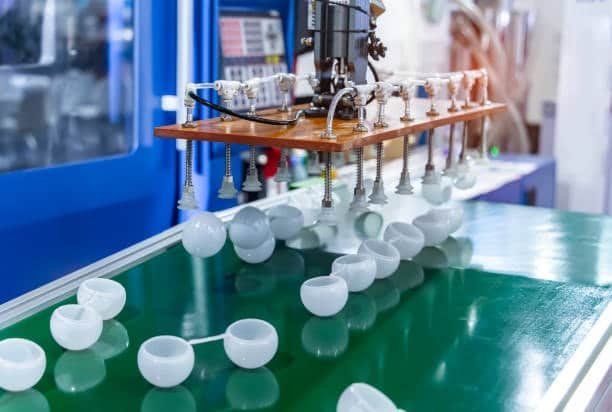
- Raw Material Quantity: Larger steel or aluminum molds need more Raw Material Quantity.
- Machining Time: More cutting time as more surface area
- Equipment Requirements: However, being as large as it is, larger molds are needed for the necessary machines needed to take on the previously mentioned feat.
- Handling Challenges: Large forms were a challenge to handle, and so the factory had to adapt when they tried precision molds larger than 5′ x 4′.
- Press Size Requirements: Surface Growth Requirements: Bigger injection machines are needed for bigger molds.
The rule of thumb is that a mold twice in size will lead to a significant increase in the final price due to various factors., which is higher than twice in cost due to the exponential effect on materials, machining time, and handling.
Cavity Configurations and Cost Implications
Total molding cost is only rank two in the total process cost; however, one of the most important decisions about the total molding cost is to determine how many cavities should be in a mold based on the capabilities of injection molding machines .
Single vs. Multi-Cavity Economics
Exacto’s single cavity mold produces one part per cycle and multi cavity steel molds produce multiple identical parts per cycle.
- Single-Cavity: Lower initial investment but higher per-part cost
- Multi-Cavity: Higher upfront cost but lower per-part cost
- Family Molds: Molds of the type Family Mold made more than one, but related part at a time.
A four cavity mold is not four times the cost of a single cavity—2-2.5x is more typical because of shared components and parallel engineering, which also requires more material .
Mold Material Selection Strategy
Choice of material differences, along with specific design features and most commonly used materials, which can lead to a lower cost, greatly influence the initial cost. , greatly influences the initial cost and long term performance.
Common Mold Materials
- Aluminum (7075, QC-10): $3,000-$25,000
- 50-70% faster to machine than steel
- Suitable for 10,000-50,000 cycles
- Excellent thermal conductivity
- Limited hardness and wear resistance
- Pre-Hardened Steel (P20, 1.2738): $5,000-$50,000
- Hardness of 28-32 HRC
- Good balance of machinability and durability
- Suitable for 100,000-1,000,000 cycles
- Accepts texturing and polishing well
- Hardened Tool Steel (H13, S7): $10,000-$100,000+
- Hardness of 48-52 HRC
- Maximum durability for high-volume production
- Can exceed millions of cycles
- Specialty Alloys (Beryllium-Copper, Ampcoloy): Premium pricing
- Ampcoloy: Premium pricing; Specialty Alloys (Beryllium Copper)
- Superior thermal conductivity
- For cores and inserts in high_heat applications, used.
- Faster cooling reduces cycle time
- Significantly higher material cost
Surface Finish Requirements and Associated Costs
Aesthetics and functionality of part are affected by various surface finishes and can also be influenced by post processing :
Surface Finish Options
- Standard Machine Finish (SPI-C3): No additional cost
- Matte Finish (SPI-B2): Adds $1,000-$3,000
- Semi-Gloss (SPI-A3): Adds $2,000-$5,000
- High Polish (SPI-A1): Adds $3,000 – 10,000 depending on surface area.
- Texturing (Light): Adds $1,500-$5,000
- Texturing (Complex): Adds $5,000-$15,000
- EDM Surface: Adds $2,000-$10,000 for precision surfaces
At a premium, chemical etching, laser texturing, specialized patterns like wood grain or leather texture can add 10-20% to the overall mold cost.
Precision and Tolerance Requirements
The cost of the mold directly depends on the required precision level.
Tolerance Classifications
- Commercial Tolerances (±0.005″): Standard pricing
- Enhanced Tolerances (±0.002″): add 15″ 25 % mold cost
- Precision Tolerances (±0.001″): Add 25-35% to mold cost, but no forming stresses.
- Ultra-Precision (±0.0005″ or less): Double mold cost at plus or minus 0.0005″ (or less than that) Ultra Precision
Creating tighter tolerances involves unnecessary additional machining processes, increased amount of tool changes, specialized measuring equipment and more time on quality verification procedures.
Advanced Mold Features and Their Cost Impact
In addition to basic components, functionality and other factors that affect cost are added by advanced features.
Sophisticated Mold Technologies
- Hot Runner Systems: Add $5,000-$50,000
- However it adds $1,000 – $2,000 per gate for valve gates for precise control.
- The cost increases by $3,000-$15,000 depending on complexity when there are manifold blocks
- Temperature controllers add $2,000-$10,000
- Action Components:
- Hydraulic cylinders: $1,500-$5,000 each
- Slides and lifters: $3,000-$10,000 each
- Unscrewing mechanisms: $10,000-$25,000
- Monitoring Systems:
- Pressure sensors: $800-$2,000 per sensor
- Temperature probes: $500-$1,500 per probe
- Position sensors: $1,000-$3,000 per sensor
Geographic Manufacturing Considerations
Cost is substantially affected by the location where a mold is manufactured, including setup costs :
Regional Cost Comparisons
- North America: $10,000-$100,000+
- The shipping and communication costs are lower but the labor rates are higher.
- Stronger intellectual property protection
- Local technical support
- Faster delivery and sampling cycles
- Western Europe: $12,000-$120,000+
- Premium engineering and quality systems
- Advanced automation and precision
- Stringent documentation and validation
- Higher overhead costs
- China/Southeast Asia: $3,000-$50,000+
- Lower labor costs
- Variable quality control systems
- Intellectual property concerns
- Extended communication and shipping timelines
- The fact that the chip would also have to cover additional import duties and freight costs would minimize any upswing.
- Eastern Europe/Mexico: $6,000-$70,000+
- Balanced cost-quality equation
- Growing technical capabilities
- Closer proximity to Western markets
- Developing quality systems
The Engineering and Design Phase Cost Analysis
Prior to physical production beginning, design engineering incurs significant costs.
Design Phase Cost Components
- CAD Design: $2,000-$10,000
- Mold Flow Analysis: $1,500-$5,000
- Design Review Cycles: $500-$2,000 per iteration
- Tolerance Stack Analysis: $1,000-$3,000
- Documentation Package: $1,000-$3,000
Mold upfront costs are 10-20% of total mold cost, yet reduce risk and optimize the final tool design.
Machining and Fabrication Cost Factors
Here are the multiple manufacturing processes of creating mold parts.
Fabrication Technologies
- Gia công CNC:$75-$150 per hour
- EDM (Wire and Sinker): $85-$200 per hour
- Grinding Operations: $80-$150 per hour
- Heat Treatment: $500-$3,000 depending on size
- Specialty Processes: $100-$250 per hour
Approximately 30–40% of total cost is created by 100–500 hours of combined machining operations in most production molds.
Assembly and Testing Expenditures
Skilled technicians assemble and test the mold when components are fabricated.
Final Production Stages
- Component Fitting:$75-$125 per hour
- Spotting and Adjustments: $80-$150 per hour
- Initial Testing: $500-$2,000
- First Article Inspection: $1,000-$3,000
- Mold Sampling: $1,500-$5,000 including press time
The final phases of this process ensure that the mold will do what is expected before the full production begins.
Industry-Specific Mold Requirements and Costs
Pricing of the molding processes depends on mold requirements and differences from industry to industry.
Automotive Industry Molds
- Rigorous validation requirements
- Extended production volumes (often 5+ years)
- Enhanced documentation packages
- PPAP requirements
- Premium pricing of $50,000-$500,000+
Medical Device Molds
- Validated manufacturing processes
- Material certifications
- Ultra-precision requirements
- Clean room manufacturing environments
- Comprehensive documentation
- Typical range of $25,000-$250,000+
Consumer Electronics Molds
- Complex geometries and thin walls
- Cosmetic surface requirements
- Rapid development timelines
- Frequent design changes
- Price range of $15,000-$150,000+
Packaging Industry Molds
- High-cavity configurations (often 16-128 cavities)
- Rapid cycle times
- Specialized high-speed systems
- $20,000–800,000+ cost range, as you might expect it to be impacted by the number of cavities in the cavity count.
Cost Calculation Methodologies
Mold costs may be calculated by different methodologies among different suppliers.
Common Pricing Approaches
- Bottom-Up Calculation: Itemizing all components, materials, and labor
- Historical Comparison: Basing quotes on assuming as close a resemblance to similar previous projects as is possible and feasible.
- Complexity Multiplier: In which the cost is multiplied by complexity factors.
- Software-Driven Estimation: One is using specialized cost estimation software (known as Software-Driven Estimation).
- Weight-Based Formulas: Calculating by the finished mold weight.
By understanding exactly how a supplier calculates something you already know the areas you can negotiate down on cost.
Detailed Cost Breakdown Structure
The typical cost breakdown of an investment in an injection mold shows how an investment should be broken down between the materials and machines:
Cost Component Distribution
- Raw Materials: 15-25% of total cost
- Design Engineering: 10-20% of total cost
- Cost Obligation: 5–10% programming + setup
- A significant part of cost, 30-40%, is due to Machining and Fabrication.
- Components and Hardware: 10-15% of total cost
- Assembly and Finishing: 10-15% of total cost
- 5-10% of total cost: Testing and Sampling.
- Profit Margin: 15-25% of total cost
It enables one to identify the places where the cost savings can be made via material substitution, design optimization, or process changes.
Small-Part Mold Cost Case Study
For a small consumer product component such as a bottle cap:
Project Specifications
- Part dimensions: 1″ diameter x 0.5″ height
- Material: Polypropylene
- Annual volume: 500,000 pieces
- Surface finish: Light texture
- Tolerance requirements: Standard commercial
Cost Estimation
- 4-Cavity Mold: $15,000-$20,000
- P20 steel construction
- Standard ejection system
- Cold runner design
- Basic cooling channels
- Expected lifespan of 1,000,000 cycles
- Per-Part Amortization: Tooling cost per part was about $0.03 – $0.04 per part with Per-Part Amortization.
Medium-Complexity Mold Cost Case Study
For an automotive interior trim component:
Project Specifications
- Part dimensions: 6″ x 4″ x 2″
- Material: ABS with TPE overmold
- Annual volume: 200,000 pieces
- Surface finish: Textured with high-gloss accents
- Multiple undercuts requiring slides
Cost Estimation
- 2-Cavity Mold Set: $75,000-$95,000
- Hardened steel construction (H13)
- Hot runner system
- 4 mechanical slides
- Conformal cooling channels
- In-mold sensors
- Expected lifespan of 3,000,000 cycles
- Per-Part Amortization:Per part over 3 year program, $0.13–$0.16 in tooling cost.
High-Complexity Medical Device Mold Cost Case Study
For a medical fluid delivery component:
Project Specifications
- Part dimensions: 3″ x 2″ x 1″
- Material: Medical-grade polycarbonate
- Annual volume: 100,000 pieces
- Ultra-precision tolerance requirements
- Clean room production environment
- Full validation requirements
Cost Estimation
- Single-Cavity Mold: $60,000-$80,000
- Validated hardened steel construction
- Hot runner system with valve gates
- Advanced surface finish
- Full documentation package
- Process validation
- Expected lifespan of 1,000,000 cycles
- Per-Part Amortization: $0.60-$0.80 in tooling cost per part
Strategic Cost Reduction Techniques
Some ways to do this include optimizing mold investment with no compromising on quality.
Design Phase Optimization
- Eliminate unnecessary undercuts
- Standardize wall thicknesses
- Design with proper draft angles (1-3°)
- Simplify parting lines
- Non-visible surfaces should be avoided with unnecessary cosmetic features.
- Optimize rib and boss designs
Material Selection Strategies
- Match the material of match mold to production volume requirements.
- Hybrid molds are considered in which the wear areas are hardened inserts.
- Evaluate aluminum for low-volume production
- Propose appropriate surface treatments and coatings
Technology Utilization
- Cut steel only after running advanced simulation
- An approach to consider is conformal cooling channels through additive manufacturing
- Standardize components across multiple molds
- Make use of modular mold bases when possible
Understanding the Total Cost of Ownership
In addition to the two factors of initial investment, the total ownership costs also include:
Lifecycle Cost Components
- Initial Mold Cost: The upfront investment
- Maintenance Costs: Typically 5-15% of mold cost annually
- Budgeting for unexpected damage in the form of repair contingencies.
- Modification Costs: Accommodating design changes repair costs
- Operational Efficiency: Cycle time impact on production cost
- Quality Costs: Scrap and rework expenses
- End-of-Life Considerations: Disposal or refurbishment
In a detailed TCO analysis, more initial investment usually results in lower long term costs due to lower maintenance and better efficiency.
Mold Amortization and Financing Strategies
There are several approaches for dealing with the capital investment of tooling.
Financial Approaches
- Linear Amortization: Spreading cost equally across expected part quantity
- Front-Loaded Recovery: Per part charges are higher near the beginning and less as time goes on.
- Customer-Financed Tooling: Part of payment is separate from part cost.
- Supplier-Financed Tooling: part pricing includes built-in tooling cost.
- Third-Party Financing: Leasing or other financing arrangements by a third party to purchase from the manufacturer.
- Hybrid Models: Partial upfront payment with the balance amortized is termed as Hybrid Models.
The best strategy hinges upon cash flow constraints mold size, production capacities, and business partnerships.
Intellectual Property and Ownership Considerations
Legal and practical reasons, in fact, exist to owning mold:
Ownership Models
- Customer-Owned: Customer retains full ownership and control
- Transferable to different suppliers
- Customer responsible for maintenance costs
- Intellectual property protection
- Storage considerations
- Supplier-Owned: Supplier retains ownership
- Lower upfront costs
- Supplier handles maintenance
- Customer risks supplier dependency
- Potential intellectual property exposure
- Shared Ownership: Negotiated terms between parties
- Reduced initial investment
- Volume commitments
- Defined transfer conditions
- Clear end-of-program provisions
Mold Maintenance and Longevity Planning
Next, proactive maintenance, i.e. other actions taken while the mold is in use, extends mold life and reduces the total cost of the mold.
Maintenance Considerations
- Preventive Programs: Scheduled inspections and service
- Predictive Maintenance: Sensors and data to predict issues (Predictive Maintenance)
- Refurbishment Cycles: Major overhauls carried out at predetermined intervals.
- Spare Parts Strategy: Critical component inventory
- Documentation Systems:Maintaining historical records
- Training Requirements: Operator and technician knowledge training requirements.
Maintenance of the mold is more important than starting a new mold mass production. A well maintained mold can produce 2 to 3 times the parts that a mold with reactive maintenance, can return the return on investment plastic resin.
Supplier Selection Criteria for Optimal Value
It is essential to choose the right mold maker that contributes as much to cost as it does to quality:
Selection Factors
- Technical Capability: Equipment, software, and expertise
- Quality Systems:Certifications and process controls are also represented by Quality Systems.
- Design Collaboration Ability: This allows an ability for Design Collaboration and Engineering Support & Optimization.
- Communication Processes: The Project management and documentation communicate processes.
- Financial Stability: Long-term support capability
- Geographic Considerations: Logistics and support
- Previous Experience: Similar projects and references insert molding.
Most of the time, the lowest bid does not translate to the lowest TCO.
Current Trends Affecting Injection Mold Costs
Injection molding trends, including a focus on low cost injection molding electrical discharge machining, are applying increasing pressure to mold costs, and there are some ways the process is changing:
Emerging Technologies
- Additive Manufacturing: 3D printed inserts and conformal cooling
- Virtual modeling to achieve the most optimum: Digital Twin Technology
- AI-Driven Design: Automated optimization algorithms injection molding project
- Hybrid Manufacturing: Combining traditional and additive methods
- Embedded sensors and monitoring systems embedded in Smart Mold Technology:
Market Factors
- Rising labor costs globally
- Reshoring initiatives
- Supply chain resilience priorities
- Sustainability requirements
- Increased digitalization and connectivity
Future Cost Projections for Mold Manufacturing
There will be several factors that will change future mold costs.
Anticipated Developments
- Additional additive manufacturing of complex cooling reduces its cost
- Laser cutting with 20% – 30% less labor content from more advanced automation.
- New improved mold materials at lower costs
- Initiatives for standardizing the requirements for custom engineering
- Artificial intelligence will use available designs to determine how to build parts that are ultimately optimized and cut development cycles.
These improvements may provide adequate compensation for labor and material increase while enhanced mold performance and lifetime.
Conclusion
The plastic manufacturing process includes a significant but necessary injection mold costs investment. Knowing the full extent of factors that drive these costs from part design and complexity through to material selection and production volume, manufacturers are able to make trade offs between initial investment and long term value. Although the offset may look large now, it is easy to analyse the cost to inject per part and often, injection mold is the most economic way of producing medium to high volume production.
Strategic design optimization, appropriate material selection, selective cavity configuration, and smart supplier partnerships can enable the manufacturers to realize the best of both cost and performance. With advances in technology, more avenues to reduce costs and increase efficiency will become available to keep injection molding an integral and foundational manufacturing process.