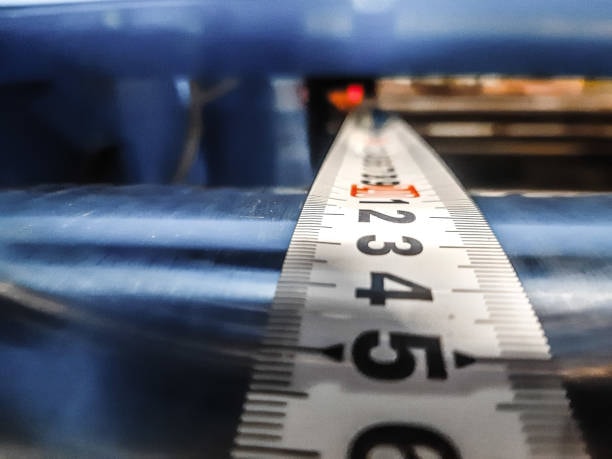
Master press fit tolerances with a complete guide on how to calculate and consider the press fit process along with ISO 286 standard, ANSI standards and fit tolerances in practice and precision making and assembly processes, including the shaft basis system .
Understanding Press Fit Tolerances in Modern Manufacturing
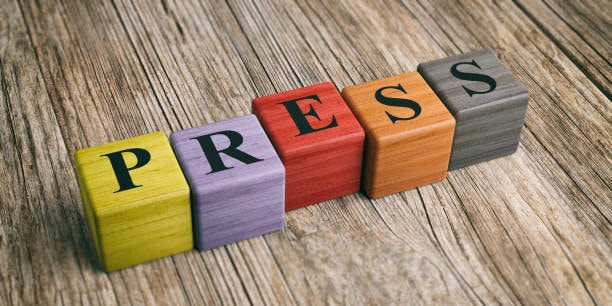
Mechanical engineering Tolerance press fit In mechanical engineering, the tolerance press fit is the allowable variance of the specified dimensions or assigned nominal size of matchable parts which must be carefully assessed through tolerance stack up analysis . This is basic principle that acts as a spine of precision manufacturing as in this method components fit together with the correct amount of interference necessary to provide optimum performance. The press fit allows parts to be built adequately, can hold their structural integrity, and can be used to perform the intended purpose during the operational duration of pieces.
Correct specification of the tolerances, along with precise tolerance calculations, is of crucial importance in the modern manufacturing world. Whether you own a design firm, manufacture automotive components, aerospace parts, consumer electronics, press fit tolerances all have an immediate effect on the quality of the products you manufacture, ease of assembly, and long-life reliability. The current details in manufacturing plants depend on such specifications to create consistency in production runs and produce parts which can be used interchangeably.
The Science Behind Press Fit Engineering
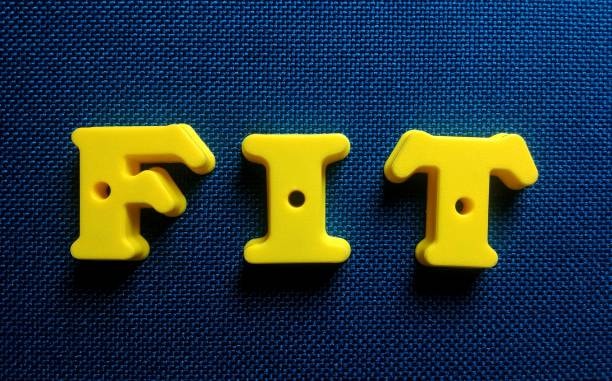
Press fit engineering is the advanced art of combinations of element of material science, mechanical engineering and manufacturing, where understanding of how much interference is critical . In an interference fit between two components, the hole is smaller than the shaft causing internal friction stress maintaining the shaft-hole-fit by friction and elastic straining, but excessive interference can lead to permanent deformation .
Mechanical concepts of press fits are complicated interaction of different variables such as material characteristics, which require thorough material analysis, and pressure-tolerance and press assembly forces. The interference causes strain on the radial and hoop stresses on both the components, where strength varies according to the level of interference, material, and other geometric few, especially at the mating surface . The knowledge of these relationships plays a serious role in anticipating force of assembly, joint strength and the form of failure.
The material considerations are an important element in press fit design, where high precision measuring tools are essential for accurate assessments . Various materials have elastic moduli and yield strengths that vary, as well as the thermal expansion coefficients, and all three factors affect the best amount of interference. These properties are also factors that engineers need to consider when choosing allowed tolerances so that assembly is guaranteed, and no parts get damaged in the process.
ISO 286 Standard: Global Framework for Press Fit Tolerances
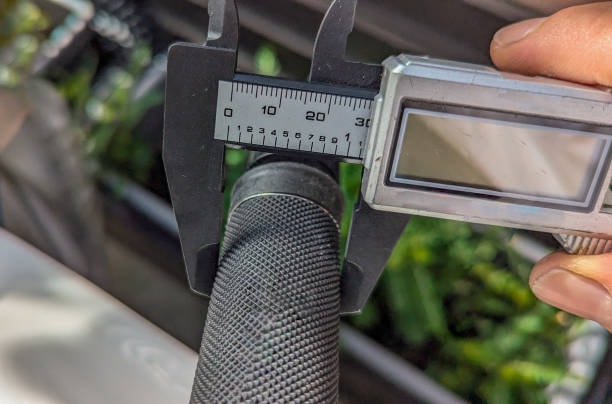
The ISO 286 is the international standard in the definition of engineering fits and tolerance, focusing on the importance of nominal dimensions . This is an overall standard that contains a systemized method of defining both hole and shaft. This standard guarantees world compatibility and replicability of manufactures in various locations. A combination of letters and numbers is incorporated in The ISO system to form a designation of the different tolerance grades and the different types of fits.
The standard ISO 286 proposes basic tolerances using nominal whereas providing a well-ordered level of precision. The grades within the IT range are IT01 (the most precise grade) to IT18 (the least precise grade) whereby each grade has a relaxation of about 60% against the foregoing grade. This geometric sequence permits manufacturers to choose adequate levels of precision, depending upon the functions needed and financial means, allowing for options such as light interference fit .
In the case of press fits, the ISO 286 usually utilizes the interference tolerances designations e.g., H7/p6, H7/r6 or H7/s6, where the first character indicates a tolerance location, within a hole basis system and the second character shows the grade of that location. These naming terms offer high levels of clarity among the designers, manufacturers, and quality control workers and limit ambiguity and consistency throughout various establishments and with varied suppliers, similar to a mechanical fastener .
ANSI B4.1 Standard: North American Approach to Fit Tolerances
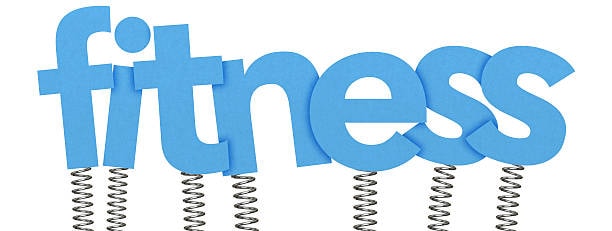
ANSI B4.1 gives the conventional shaft-hole fit generally used in the North American Industry. However, ANSI B4.1 differs in nomenclature and quantity designations compared to ISO 286, particularly in defining terms like loose fit since it has been developed with differing regional manufacturing practice and historical preference. It is necessary to get to know both standards as long as companies work on the international market, or cooperate with international suppliers.
The ANSI system classifies fitting as running and sliding fitting, locational fitting and force fitting (including press fitting), with specifications including the outer diameter of the components . There is a functional requirement where the categories of fit are met, such as friction fit and force fits that deliver the interference in permanent or semi-permanent assembly. The standard gives in tabular form hole, shaft limits both by hole size and by shaft size.
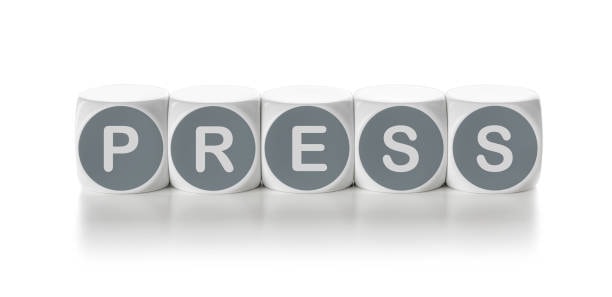
The main points of difference between ANSI and ISO standards are the method of calculation of the tolerance, including tight fit specifications grade designation and size preferences. Where ISO may be more systematic in its use of math, ANSI standards may reflect the real life experience in manufacturing and industry practice. Recent manufacturers have to be familiar with both of the systems and various manufacturing methods in order to be compatible with a variety of customer needs and supply chain partners.
DIN 7157 and Other International Standards
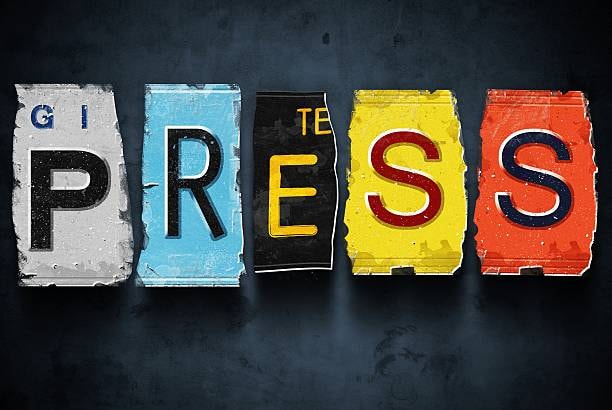
In DIN 7157 another critical resource to the specifications of press fit tolerances exists, including guidelines for in process measurements . German standard system has already left its mark in the practice of European manufacturing and is still referred to in various industries and applications. The awareness of the connection between various national standards allows engineers to work with complex international projects and be sure they will meet the requirements of the region, despite dimensional differences in components .
Other important standards are the JIS (Japanese Industrial Standards), GB (Chinese National Standards) and a vast number of industry-specific standards provided by e.g. ASTM, SAE, and API. Every common system is a reflection of a local culture, technical and economic variables that affect the practice of manufacturing in each area, including the use of soft material in certain applications .
International convergence to ISO standards is a worldwide movement towards standardisation, although practice still varies with legacies, and regional preferences. Effective engineers need to know several standard systems and how they can be related to each other to be able to operate in the current global production world, particularly when factors such as relative motion are involve .
Calculating Press Fit Tolerances: Mathematical Foundations
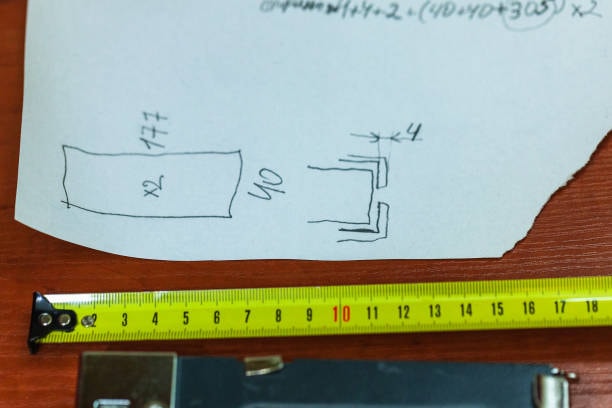
The calculation of tolerances in press fits requires complicated mathematical relations based on material properties, geometry of the part and assembly needs. The basic interference calculation starts with calculation of the necessary holding force that is based on torque transmission and axial resistance to the load or positional accuracy the application may demand.
The simplified expression of the calculation of interference is a calculation of radial interference depending on the needs of contact pressure. Interference and contact pressure relationship is determined by the elastic properties of both the materials, the geometry, such as diameters ratios, and the stress distribution around the joint. The theoretical basis of such calculations is classical thick-walled cylinder theory.
Calculation of tolerance used in practice must be done with regard to variations in manufacturing, and effects of temperature, and assembly considerations. The entire example of tolerance stack up incorporates contributions of both mating parts so that when carefully analyzed the minimal interference should allow a joint with sufficient strength and the closest possible interference should be within the assembly capability limits.
Tolerance Grades and Their Applications
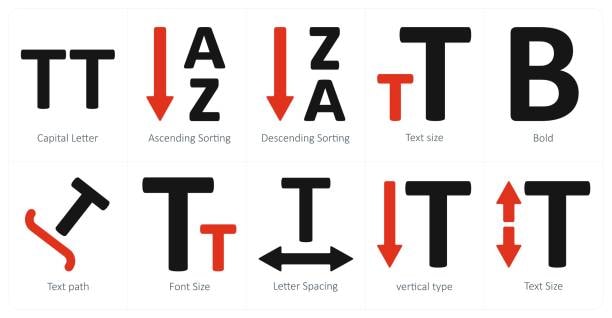
Tolerance grades indicate various manufacturing accuracy, and different types such as clearance fit can be categorized, where smaller tolerance grade means stronger manufacturing procedures and greater prices. The limit of tolerance to each machining part is dependent on the functions of the part. Based on the relationship indicating the correlation between the grades in tolerance and the functional requirements, this provides better design evaluations that balance between the performance and cost of structural components .
The finer grade (IT5, IT6) grades are normally only available where precise positioning, high torque transfer, axial holding force or low runout precision is paramount in the application. The extra manufacturing price may in many cases be recouped by increased performance, long life or minimised maintenance, especially in critical applications such as engine components . Some are bearing installations, precision gear assemblies, and high-speed rotating equipment.
Reduced precision grades (IT7, IT8, IT9) are also useful to more relaxed applications in which moderate interference is acceptable to functional needs. These grades present a huge cost savings at the same level of adequate performance which can be used in making general mechanical assemblies, housing installations, and structural connection, often verified with plug gauges .
Material Properties Impact on Press Fit Design
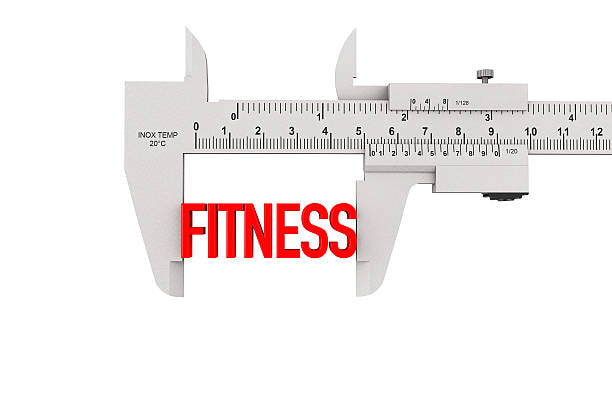
The choice of materials has an immature impact on press fit shapes, particularly concerning hole tolerance and tolerances specification. Elastic moduli vary with different materials thus changing the interference and contact pressure relationship, and this material determines the overall fit performance . Greater modulus materials provide more contact pressure with a given interference, and may need smaller interference values to provide needed performance.
When the level of interference is close to the possible plastic deformation, the matter of yield strength is critical. It should also be taken into consideration that the stresses due to assembly and operating must be within elastic limits in order to maintain structural integrity of the joints and should allow disassembly where it is necessary. The safety factors commonly put into consideration material property changes and possible stress concentration hole diameter.
Use of thermal expansion coefficients influence tolerance and the performance of press fit under varying temperatures considerable pressure. Different expansion rate materials could also have varying interference over a range of temperature, which could hurt joint integrity, or cause excessive stress. Efficient designers have to take into consideration the range of temperature of the operation and use materials that have corresponding thermal performance.
Surface Finish and Its Effect on Press Fit Performance
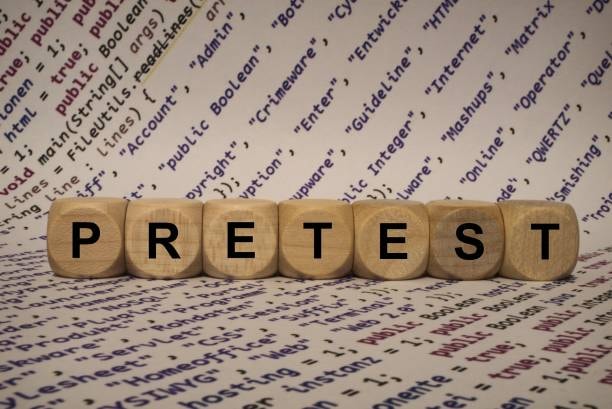
Finishing of a surface greatly influences the performance and press fit assembly. The rougher surfaces further enhance the interference making them effective by introducing peak-to-valley fluctuations to the nominal dimensional interference slightly larger. This can significantly change assembly forces and end contact pressure and the specification of surface finish is very important to obtain repeatable results.
Normal required surface finish of press fits is Ra 0.8 to Ra 3.2 micro-meter based on level grade tolerance, slip fit tolerance, and functional needs. Finer finishes decrease assembly force variations and give a more predictable contact pressure, at an elevated cost of manufacture. The best finish of the surface is based on a trade off between performance and economic factors.
The coefficient of friction during assembly is influenced by surface finish and has an effect upon the forces required to reach assembly and whether galling or seizure is likely to occur. Correct surface preparation such as proper finish and sometimes special coating give dependable process of assembly procedures and excellent performance of joints.
Press Fit Force Calculations and Assembly Considerations
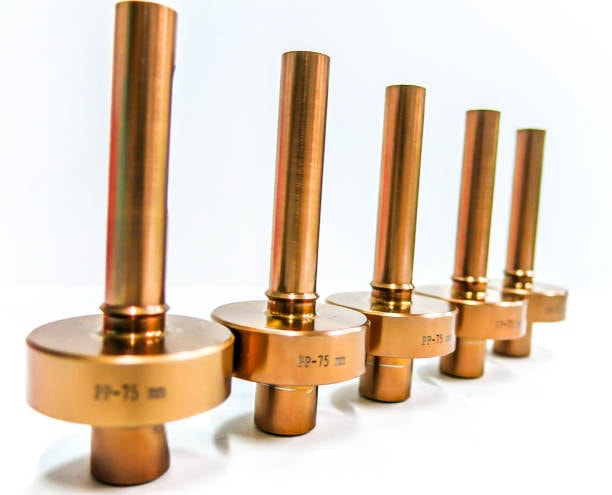
Press fit force calculators compute what the assembly force may be. Accurate computation of the assembly forces is very essential in the selection of the appropriate equipment to be used, safety of the workers and safety of the components to be assembled. It is computed based on friction forces, geometrical quantities and material characteristics.
The simplest force is calculated by multiplication of the contact pressure, contact area and coefficient of friction. But realistic calculations should include changes in stress distribution, edge effects and dynamic conditions when assembly occurs. Stick slip effects and elastic deflections can cause peak forces to be greater than steady-state.
The selection of an assembly method is based on the necessity of forces calculated, geometry and production quantity of the components. There are hydraulic presses, arbor presses, thermal expansion and automated assembly systems that might be considered. The methods have their benefits and restrictions which need to be aligned with the requirements of the application.
Quality Control and Measurement Techniques
The process of controlling quality of press fits will be achieved with more accurate methods of measurement and statistical control procedures. Conventional ways of measuring dimensions by using micrometers, calipers, or coordinate measuring machines, can verify dimensions in the most fundamental sense, but it may not account in all influences that can access fit performance.
Go / no-go gauges provide pragmatic means of production measurement, which verifies acceptable ranges of measurements very quickly. These gauges should be well designed and maintained so as to get the accuracy and repeatability of measurement. To be able to measure, gauge tolerances are normally 10-20% of part tolerance.
Advanced measurement methods incorporate pneumatic gauging, the laseright measurement method and vision measurement method. The technologies provide increased speed of measurement and less operator impact, and permit greater collection of statistical process control and continuous improvement projects.
Common Press Fit Applications Across Industries
Press fits find wide automotive application in holding gears onto shafts, bearings into housings, bushings to suspension parts, etc. They have to be able to work under high dynamic loads, face temperature variations, and lengthy service life conditions without the loss in the precision of the positioning and ease of maintenance.
The most demanding and precision components are those serving in the aerospace where slip fit press fits are used on components of the engine, landing gear assembly, and components of control systems. It has a rigorous operating environment demanding the careful selection of materials and exact specification of tolerances and aggressive quality control to afford mission critical reliability.
The industrial machinery applications are very wide and varied, including heavy-duty mining apparatus, to precision manufacturing apparatus. press fits Power transmission, component positioning and structural connections are some of the functions served by the press fits. The conditions of its operation vary, which demands adaptable design strategies and the in-depth knowledge of the application conditions.
Troubleshooting Press Fit Problems
Problems in assembly are common where tolerance issues, material/compatibility issues or problems on the surface are involved. Unnecessary forces of assembly may be caused by interference values that were higher than calculated on design, deviation of surface roughness or material property deviation. To fix any malfunctions with the help of systematic troubleshooting, one will have to calmly examine all the preceding factors.
Joint failure modes encompass inadequate holding power, stress induced cracking and interference fit calculation relate fretting corrosion. To every failure mode, some root causes and corrective actions are proposed. A low holding power is normally associated with low interference, whereas cracking is a sign of too high interference or stress concentrations.
The preventive strategies involve extensive validation of the design, effective management of the process and active surveillance of the assembly process. Trends of the same show that statistical analysis of assembly data can detect trends which signal that the process has changed before a quality problem causes a production halt.
Advanced Press Fit Design Considerations
Sophisticated geometries also need special analysis tools, like those that do not merely involve use of cylinder press fits. More stresses occur due to tapered press fits, stepped shafts and thin-wall components, which necessitate alternative analyses techniques. Frequently these advanced applications may require finite element analysis.
The effects of temperature during operation may have a large influence on press fit performance, especially regarding the shaft’s outer diameter . Existing effective interference can be boosted or diminished by differential thermal expansion, depending on the material combination of the components, and the change of temperatures. The design analysis should lay into countenance the whole operational temperature range as well as the possibility of thermal cycling.
Rotating machine and vibrating equipment require the consideration of dynamic loading effects. Fatigue analysis, fretting wear analysis and stress concentration factors must be evaluated well so future reliability can be guaranteed under dynamic operating condition.
Digital Tools and Software for Press Fit Analysis
In current CAD systems it is possible to perform press fit analysis, allowing a designer to calculate the effects of tolerance during the design process. They include interference calculations, estimation of assembly forces, and improvement of tolerance specification to given applications. The ability to be integrated with manufacturing planning systems makes transitioning between design and production to be seamless.
High end press fit analysis can be performed by means of specialized software packages that include, finite element integration, material property databases, extensive reporting options and more. Such tools allow optimizing complicated designs and deliver documentation that assists with design choices as well as manufacturing.
Manufacturing execution systems also become more and more capable of monitoring press fits, measuring actual assembly forces, dimensional change, and process variables in real time. This information allows long-running improvement efforts and forecasted maintenance of assembly equipment.
Economic Optimization of Press Fit Tolerances
Tolerance specification cost-benefit analysis has to take into account the cost of manufacturing, the cost of quality and the performance advantage. The application of tighter tolerances improves manufacturing costs that may minimise assembly issues; enhance performance of products; and cut down warranties. The ideal tolerance is the total cost that can be achieved by combining all the factors.
The analysis of the manufacturing capability assists in identifying effective tolerances considering the available processes and equipment. When it comes to specifying tolerances that cannot be produced, this means there will be extra costs, extensions in schedules and quality issues. The possibilities of processes can be comprehended and hence the specification of realistic tolerance and cost-effective production of processes is possible.
The qualification, as well as the development of suppliers, are also important factors in cost-effective press fit production. Collaborating with suppliers to achieve knowledge, improve their processes, and build special skills can offer competitive edge and advance quality of a product.
Future Trends in Press Fit Technology
The use of additive manufacturing technologies in press fit is starting to be felt especially on complex geometries and on the customized components. Although present additive processes cannot offer surface finish and dimensional precision needed in more exacting applications, the process improvements still have more potentialities in special applications in the future.
Real-time press fit assembly process monitoring, predictive quality control and adaptive process control are smart manufacturing concepts. Such technologies can offer better consistency, less wastage, and better quality of products using process optimization based on data.
New options are available in press fit applications with more advanced materials such as composites, engineered plastics and special metal alloys. These materials can just include better performance properties, light weight, or better exposure to the environment, but need renewed design methods and tolerance limits.
Integration with Supply Chain and Global Manufacturing
Such matters as manufacturing abilities, standards of quality and communication procedures among various suppliers involved in different countries must be understood in global supply chains. Various facilities manufacturing press fit components have to uphold the same quality and interchangeability between similar components despite differences in the equipment, processes and quality systems.
Supplier development programs are aimed at the ability of creating capability and communications and the establishment of standard quality throughout the supply base. The programs usually cover training on interpretation of tolerance, techniques measurement and quality control in press fit applications.
The risk management measures mentioned cover possible interruptions of the supply chain, fluctuation of quality, or capacity shortages of these press fit parts that may affect their availability. To keep production going, there is diversification of sources of supply, alternative suppliers who are qualified and inventory strategies.
About GWT Worldwide
Shenzhen Guanwutong International freight Forwarding Co., Ltd. (GWT Worldwide) is a professional logistics service provider, focusing on international freight forwarding, logistics, supply chain and international cross-border e-commerce logistics. With the know-how of air, sea freight, China- Europe railway transport, international express solutions, customs clearance, warehousing to even Amazon FBA shipping support facilities, GWT Worldwide, makes sure that your precision engineered parts and press fit assemblies move safely and efficiently to their destinations. The great logistic technology as well as international network makes our international trade ease when a manufacturer needs a good transportation of mechanical components of high tolerance.
Conclusion
Just like any other aspect of cinema technology, being able to understand press features can only be achieved through a combination of the theory and experience and with the constant update of the available technologies and norms. ISO 286, ANSI B4.1 and DIN 7157 are common standards of press fit tolerance and form the basis of worldwide manufacturing practices. Future success of press fit applications is based on adopting new technologies together with new technologies as well as retaining underlying engineering principles and quality measures which facilitate reliable and cost effective solutions of manufacturing processes.