CNC (Computer Numerical Control) turning is an important manufacturing process known as cnc turning where the workpiece rotates during the rotation of a work piece, accompanied by the cutting of a tool to remove material and to shape the part, showcasing the benefits of computer numerical control. CNC turn machines are used in all the industries for producing high precision cylindrical items like shafts, spindles, and valves. Few things are more important than proper setup and operation of CNC turning machines in order to obtain consistent results, maintain safety, and to be efficient.
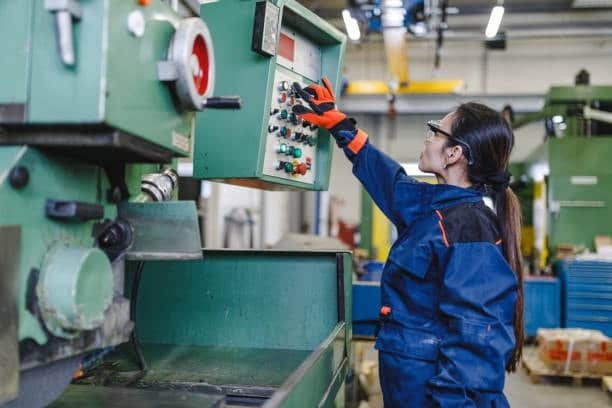
The right setup involves the choice of appropriate tooling, the correction of accurate cutting paths, and the fixing of the workpiece’s workpiece tightly to avoid vibration. Proficient operators need also to observe closely the machining process for any adjustment of parameters and avoid defects or wear of turning tools. Properly carried out, CNC turning operation produces cylindrical parts with small tolerances and high quality of surface, making it undeniable in the industries like automotive, aerospace and industrial production.
This article presents a comprehensive tour of the cnc turning process and CNC machines’ turn-on, the necessary steps for setting up the machine, and the important considerations fo
r a successful operation of the CNC machines, emphasizing the role of cnc technology .
What is CNC Turning?
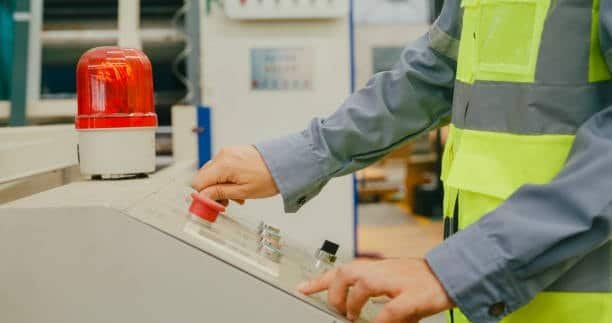
CNC turning is the process in which the work piece held in a rotating spindle while a single point cutting tool which is stationary, removes the material in chips, widely utilized in the manufacturing industry . The cutting tool moves in a programmed path under controlled computing thus enabling the accurate making of complex shapes and geometries.In the domain of manufacturing, CNC turning is used mostly in making cylindrical and conical parts. It is widely used in aeroplane, automobile and medical device manufacturing bodies. CNC turning machineries are of the types whose precision and repeatability of the production of parts with tight tolerances are a forte.
Automation of these fine movements by control of a computer not only increases efficiency but also decreases the human error margin reciprocally guaranteeing continuity of quality in large volumes of production. Besides, the improvement of vertical turning centers technology at present can be performed in a multi-axis mode during the cutting process , making it possible to create more complicated parts without alternative set-ups. Such flexibility is what makes the CNC turning techniques an essential process for industries which require precision and scalability at high levels, including optimal cutting speed for example, aerospace, automotive, and medical devices manufacture.
Steps to Turning On CNC Machines
In order for the horizontal lathe machine to operate safely and efficiently there are a number of important steps that have to be taken when turning on a lathe machine. Such measures are essential not only in preventing damage of the machine tool, but worker’s safety and delivery of high quality parts as well.
1. Check Machine Settings and Environment
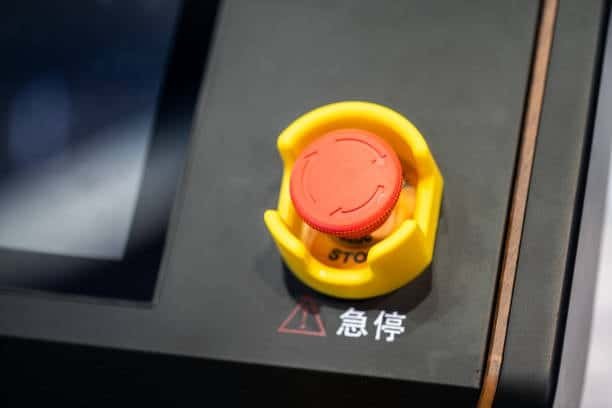
It is very important to check on the environmental conditions in the surrounding place of the CNC machining before operating it. Make sure the cutting edge of specialized tools being used in the cnc machining process s clean free of any debris that might interfere with its working. Well lit workspace is also necessary as well there must be proper ventilation as well particular if the machine utilizes coolant or lube systems. Besides, ensure that for the safety equipment such as emergency stops, safety shields as well as guards are all present on the cnc control panel . Personal protective equipment (PPE) i.e safety glasses, gloves and hearing protection to be worn always before using machine.
More to it, inspection and servicing the CNC machine periodically is essential to avoid break-down and efficient performance. Operators should also ensure that all the turning tools and workpieces and raw material re properly secured before the start of the machining process to avoid accidents as well as material damage. Not only personnel is protected by these environmental and safety protocols during the turning operation , but the equipment lifetime is also extended and the better manufacturing environment is provided.
2. Inspect the Workpiece and Tooling
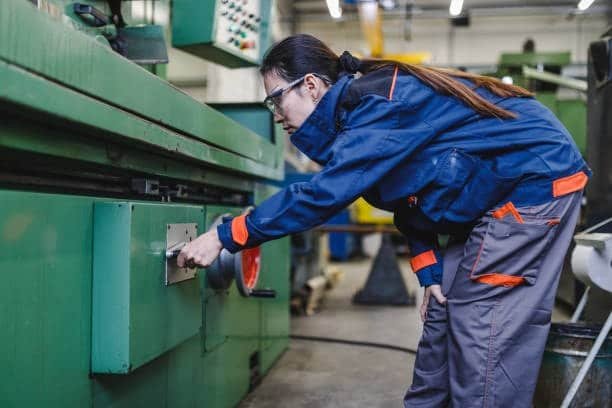
The second action is therefore to examine the workpiece and make sure that is firmly fitted on to the lathe. Double check the material so that it conforms to the requirements on the part to be machined. Make the check on turning tools as well, ensuring they can achieve the desired diameter . Make sure they are correct, and they are sharp and have no damage. If needed replace or tune the tool to achieve the maximum of cutting performance. Correct choosing of tools for different turning operations, including straight turning, is very important to obtain the success and to avoid the damage of the workpiece of machine.
The second action is thus to look at the work piece and ensure that it is well secured into the lathe. Recheck the material to make sure that it is suitable to the needs of the part to be machined. Check the cutting tool too – make sure it is the right kind, sharp and undamaged with excessive wear-and-tear. Replace or recondition the tool if it is necessary to achieve the optimal cutting performance. The selection of the right tools and proper maintenance in cnc turning play a vital role not only in obtaining high quality results but also for ensuring security of work piece as well as the machine. What is more, the testing of the tool’s compatibility with the material also ensures the tool does not break and the production does not halt.
3. Power On the CNC Turning Machine
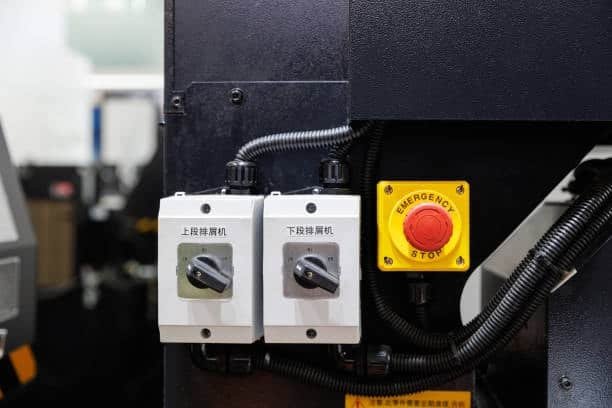
After the machine, workpiece and tooling have been checked, it’s time to switch on the CNC machine. First power on the cnc lathe machine main control panel. On most CNC machines it entails simply flipping a switch on or pushing a button to activate the machine’s electronics. There should be a glow up the control screen revealing the electrical components of main menu or home screen. If there is an error message or alert, check it out now in the display screen. If there are problems, for example, low coolant or wrong settings – correct them and go ahead. In case of some machines, there maybe a need to carry out system diagnostics to ascertain that the machines are functioning properly, particularly when dealing with an existing hole .
After completing the initial startup procedure and there are no errors, the operator should home the machine axes so as to have a reference point for all the movements that follow. This step makes certain that CNC machine is aware of accurate location of the tool and workpiece so that there are no misalignments of the work during machining. It is also advisable to load the right program file and check the source code for correctness, especially when dealing with cnc lathes checking parameters like feed rates, spindle speed, and tool paths prior to the running of the operation. These preparatory steps are important for a flawless rendering of the machining activity with high precision and safety.
4. Home the Machine
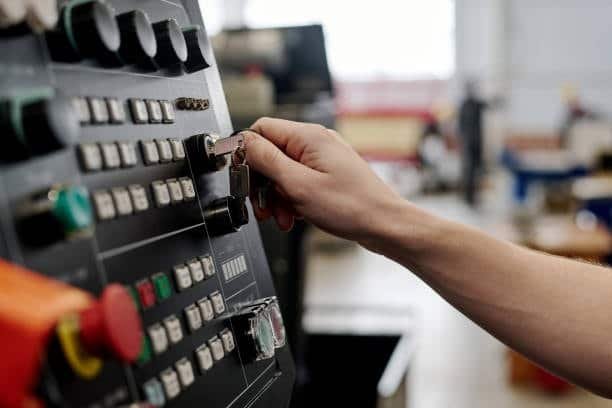
Following turning on of the CNC turning machine, the next step is to “home” the machine. Homing the machine translates into moving every axis to the already programmed zero positions this makes a reference point from where all movements of the machine are made. This helps the machine know the location of that cutting tool and that workpiece properly. Normally, the machine will automatically carry out a homing cycle upon switching it on. However, you might have to activate the homing by using the control panel according to the given model of the CNC lathe.
After switching on of the CNC turning machine, the next action is to “home” the machine. Homing the machine is equivalent to taking all the axes to the zero positions that have been programmed- this is an indication point whereby all the movement of the machine will be made. This assists the machine to be aware of the position of the cutting tool and the workpiece well. Usually, the machine will do homing cycle automatically once it has been switched on. However, you may need to switch on the homing by using the control panel based on the given model of CNC lathe. Proper homing of the machine is very important because any misalignment at this stage can result into inaccurate cuts or collisions when it is put to operation. After homing, verity check that all the axes have set at their zero positions properly before conducting tools like the special purpose knurling tool and work pieces alignment.
5. Load the Program
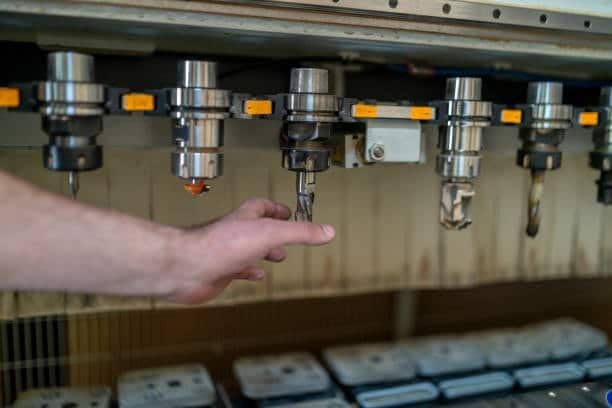
Once homed the machine, download the corresponding CNC program to the machine’s control system. CNC programs are written in G-Code, a language used to tell the machine how to move cutting tool and what operation to do. Make sure that the right program is chosen, and it matches to types of cnc turning centers that are installed on the machine. After loading the program you can run the program on the control system of the machine to make sure everything is done right before you begin machining.
When homed the machine, the download the corresponding CNC program to the machine control system. G-code is the language in which the CNC programs, including cnc milling, are written and it helps in telling the machine how to move the cutting tool and the types of operations that need to be undertaken. Confirm the selection of the appropriate program and ensure that it meets the design of part and the arrangement of toolings on the machine. Once the program is uploaded, one should run it through a dry run or a simulation run in the control system to ensure all tool paths, movements and commands are correct and safe. This step allows avoiding costly mistakes, collision, or even breakage of tools, so that the process of machinating was started smoothly and safely.
6. Set the Work Offset and Tool Offset
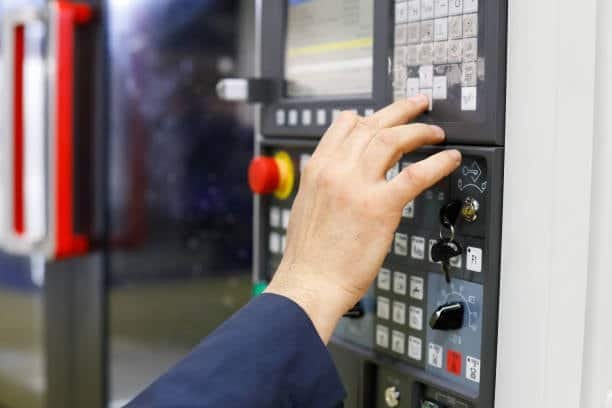
For the turning process to be precise work offsets and tool offsets have to be set well. The work offset, while the tool offset refers to the point of reference to the use piece, and the position of the cutting tool relative to the workpiece. Define work offset by hand maching the tool to that position and then marking it on the control panel of the above machine. The tool offset is normally adjusted with a gauge or probe which determines the tool’s length & diameter automatically. Correct adjustment of these offsets ensures that the tool geometry and tool life will be extended and tool will move the right way in relation to the workpiece and hence minimizing errors.
Proper setting of the work offset and the tool offset in the need to ensure that the machining process is precise. The work offset is associated with the reference point of workpiece, while tool offset is the position of the cutting tool from the reference point of workpiece. To set the work offset, the machine operator usually machines the tool to the presumed zero point on the workpiece by hand, such as the top center or the corner, and inputs this figure in the machine’s control panel. Generally, the tool offset is established with the help of tool setter, gauge, or automatic probe that accurately determines the tool’s length and diameter. Such values are then recorded in the tool library of the CNC system. Even work and tool offsets are adjusted correctly, so that the machine understands and reads the program for precision machining correctly, which is critical when it comes to reducing dimensional errors, avoiding collisions, and having consistently excellent parts.
7. Start the Machining Process
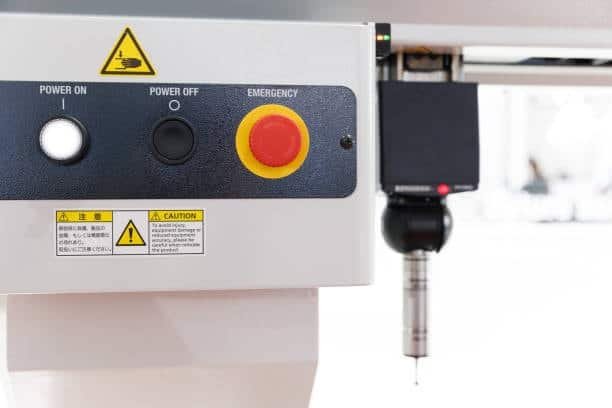
With all the checks over and all settings set, you can now begin the machining process. To initiate the CNC machine activate the “start” button on the control panel. The machine will start turning involves rotating the work piece as the cut tool tracks the programmed path, aiming to efficiently remove material. Keep a wary check on the process for a few minutes at the start to be sure everything is well. Pay attention to unusual sounds, tap vibrations, and monitor a machining process on a screen. Should there be any problems, shut off the machine to avoid additional damage.
After all the checks are done and the required settings are made, you can start the machining process. To start the CNC machine, press “start” button on the control panel. The machine will now rotate the workpiece while the cutting tool will traverse along the programmed G-code path, facilitating effective material removal to give the desired shape. It is necessary to carefully monitor the first moment of operation to make sure that everything works well. Look out for any signs of anomaly – unusual sounds, tool chatter, excessive vibrations, or aberration from expected toolpath. Most CNC systems also show real time machining parameters on screen e.g. spindle speed, feed rate and tool position which may assist to prove the program is running successfully. Do not hesitate to press the emergency stop should any problem occur and avoid potential damage to the workpiece, the tool or the machine as such.
Conclusion
The process of switching on a CNC turning machine is a significant process that demands the key of detail and right setup. Inspecting the machine and the tooling, loading the right program and applying offsets is part and parcel of the process of guaranteeing safe and efficient operation of the cnc turning machine. A perfect start for machine tool is not only beneficial for quality deliverance but also ensures longer life-time for equipment.
The turn on of CNC turning machine is a serious process that involves paying attention to details and set up. Observation of the machine and tooling, Inputting a program in the machine and application of the correct boring tool, horizontal turning center working and tool offsets is crucial in achieving safe, precise, and efficient machine operation. An in-depth startup procedure does not only result in better outputs but also reduces the risk of operational mistakes that may cause expensive reworking or destruction to the cnc milling machines. Furthermore, it helps to ensure the lasting health and reliability of the equipment because of fewer downtimes and maintenance costs. In the industries that require time and accuracy, such strict handling of machines becomes a landmark in their successful production.